Category: News
Here are the news for company and powder coating industry.
UV-curable Powder Coatings Advantages
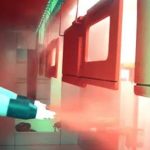
UV-curable Powder Coatings Advantages UV-curable powder coatings is one of the fastest coating chemistries available. From start to finish the entire process for finishing MDF takes 20 min or less, depending on chemistry and part geometry, making it an ideal finish for applications that require a quick turnaround. A completed part requires only one coat, allowing increased production with 40 to 60 percent less energy than other finishing processes. The UV-curing process is much simpler than other finishing technologies. CuringRead More …
Difference Between Cold Rolled Steel and Hot Rolled Steel
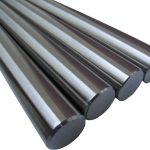
Difference Between Cold Rolled Steel and Hot Rolled Steel COLD ROLLED STEEL: The most common of the metals encountered by the jobshop powdercoater, this product is roll formed to a close tolerance and a fine surface finish, suitable for stamping, forming, and moderate drawing operations. This material can be bent flat upon itself without cracking. Good base for phosphate conversion coating. Pretreatment recommendations are Clean, Phosphate, rinse, and seal or deionize rinse. HOT ROLLED STEEL: A low carbon steel suitableRead More …
TGIC-free powder coatings provide cost-saving benefits
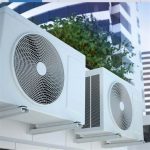
TGIC-free powder coating options are available and are being used by manufacturers worldwide to achieve the same durable finish benefits as TGIC powder coatings. In fact, there are several advantages to the newer technology. It offers not just exterior durability, but enhanced mechanical performance, as well as flow and leveling properties. TGIC-free powder coatings provide cost-saving benefits to finishers by offering superior first-pass transfer efficiencies. Companies that have converted to TGIC-free based coatings have documented first-pass transfer efficiency improvements of asRead More …
The advantages of fluorocarbon powder coating
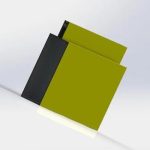
Fluorocarbon powder coating is a poly-vinylidene fluoride resin nCH2CF2 baking (CH2CF2) n (PVDF) as the base material or with metallic aluminum powder coating made for the toner. Bond of fluorine / carbonized the fluorocarbon base material in the chemical structure in conjunction with such a structure of the nature of having a short key is combined with hydrogen ions most stable solid combination, on the stability and solidity of the chemical structure different physical properties of the fluorocarbon paint inRead More …
Eddy current generation in a metallic conductor
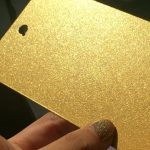
A.1 General Eddy current instruments work on the principle that a high frequency electromagnetic field generated by the probe system of the instrument will produce eddy currents in an electrical conductor on which the probe is placed. These currents result in a change of the amplitude and/or the phase of the probe coil impedance, which can be used as a measure of the thickness of the coating on the conductor (see Example 1) or of the conductor itself (see ExampleRead More …
The important element for recoating powder coating
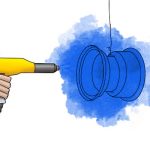
The most important element for recoating powder coating and as a matter of fact, for applying a different topcoating over an applied coating is to be sure the new coating will not lift or wrinkle the old coating. Check the old applied coating with a strong lacquer thinner by wetting the surface and giving it a couple of rubs with a damp cloth. If there is no excessive softening the coating should be OK to recoat with a new liquidRead More …
What Is The Film Hardness

The hardness of the powder paint film refers to the resistance of the paint film after drying has a solid, i.e. the film surface the role another on the greater hardness of the material performance. This resistance exhibited by the film can be provided by a certain weight of the load acts on the relatively small contact area, by measuring the ability of the film antideformation manifested, so the film hardness is a view showing one of the important propertiesRead More …
Characteristics of electrostatic powder coating spraying
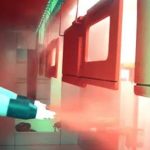
Characteristics of electrostatic powder coating spraying Electrostatic powder coating spraying because he does not use the solvent will not cause solvent pollution in the atmosphere, while avoiding the danger of fire due to the solvent, is also easy to transport and storage of raw materials. The spraying process, the overspray powder is not coated on the workpiece can be recovered, the recovery rate of up to more than 95%, to improve the utilization of raw materials, to reduce the materialRead More …
Characteristics of the electrostatic spraying
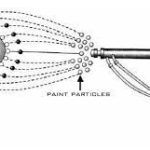
Generally speaking, where does not occur at 200 ℃ deformation, enables the charged powder particles are adsorbed on the surface to be painted, the surface coating can be by electrostatic powder spraying. Therefore, electrostatic powder coating spraying technology can be widely used instruments, household appliances, mechanical and electrical equipment, automobile and shipbuilding, light industry equipment, furniture, machinery and building materials, and other metal parts of the surface protection and decorative painting. View from currently used in spray technology, electrostatic powderRead More …
Clear Powder coating versus Liquid paint on Aluminum Wheels
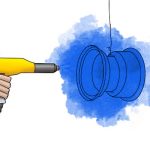
Clear liquid polyurethane coatings are used quite extensively in the automotive industry. They’re primarily used as the clear coat, top coat found on most cars and are formulated to be very durable. Clear powder coating have not yet gained recognition in this area primarily due to aesthetic reasons. Clear powder coating are used quit extensively by automotive wheel manufacturers, are durable and can be very cost-effective Powder coating application requires special electrostatic spray guns, and an oven to melt andRead More …
UV powder coatings bring the benefits to heat sensitive substrates

UV powder coatings bring the benefits to heat sensitive substrates Powder coating provides a durable, attractive and economical alternative to liquid paints and laminates for a wide range of heat-sensitive products such as glass and plastic materials. Powder coatings are dry, 100 percent solids paints that are spray-applied in a process similar to liquid painting. Once coated, products are conveyed through a curing oven, where the powder melts to form a durable, attractive finish. Powder coatings have long been theRead More …
Some HEAT-SENSITIVE SUBSTRATES in coatings industry

HEAT-SENSITIVE SUBSTRATES in coatings industry In recent years, ongoing research and development has been devoted to formulating powder coating powder that can cure at low temperatures, below 212ºF, without compromising durability or quality. These powders can be used on temperature-sensitive materials, as well as on massive parts that require enormous amounts of energy with other curing systems. Wood materials such as particle board and fiberboard, as well as glass and plastic products, can now benefit from a powder coated finishRead More …
Weekly maintenance for powder coating oven
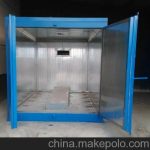
How to Weekly maintenance for powder coating oven Burner blower impeller and motor The cleanliness of the fan impeller directly affects burner blower efficiency . Periodic cleaning keeps the blower in good condition,preventing premature bearing failure. Keep blower motors clean to avoid overheating, which can cause electrical failure. By simply removing dirt buildup on the motor housing and cooling fins, you can eliminate costly motor replacement. Heater shell interior Now is a good time to check the heater shell, orRead More …
The market for electronic components protective coatings exceed US$20 billion In 2025
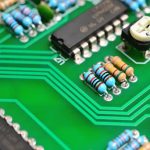
A new report from GlobalMarketInsight Inc. shows that by 2025, the market for protective coatings for electronic components will exceed $20 billion. Electronic component protective coatings are polymers used on printed circuit boards (PCBs) to electrically insulate and protect components from environmental stresses such as moisture, chemicals, dust, and debris. These coatings can be applied using spray techniques such as brushing, dipping, manual spraying or automatic spraying. Increased use of portable electronic products, increased demand for automotive electronics applications, andRead More …
NCS is short for Natural Color System
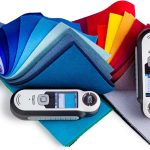
NCS Introduction NCS is short for Natural Color System. It is the world’s most prestigious color system and the most widely used international color standard and color communication language in practice. It is the highest color quality standard required available internationally. NCS natural color system has been widely used in many fields such as color research and education, planning and design, industry and production, corporate image, commerce, and so on. It is used in many industries such as textiles, clothing,Read More …
Future development prospects of hydrophobic paint
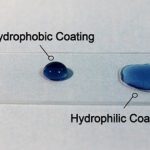
Hydrophobic paint often refer to a class of low surface energy coatings where the static water contact angle θ of the coating on a smooth surface is greater than 90°, whereas superhydrophobic paint are a new type of coating with special surface properties, meaning water contact with a solid coating. The angle is greater than 150° and often means that the water contact angle lag is less than 5°. From 2017 to 2022, the hydrophobic paint market will grow atRead More …
Application of Self-Healing Coating Technology in Powder Coatings
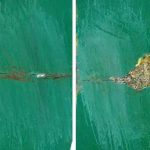
Since 2017, many new chemical suppliers entering the powder coating industry provided new assistance for the advancement of powder coating technology. The coating self-healing technology from Autonomic Materials Inc. (AMI) provides a solution to the increased corrosion resistance of epoxy powder coatings.The coating self-healing technology is based on a microcapsule with a core-shell structure developed by AMI and can be repaired when the coating is damaged. This microcapsule is post-mixed In the preparation of powder coating process . Once theRead More …
The wood furniture manufacturer must know – Powder Coating
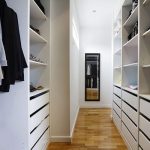
We are often asked about the difference between powder coating and traditional liquid coating. Most people are also interested in wanting to know more about the advantages of powder coating, many of which are incomparable to other coatings. Powder coating is solvent-free 100% dry solid powder, and liquid coating needs solvent to keep liquid, so the most obvious difference is that the powder does not require solvents. Powder coating become more interesting due to its advantages. Let’s take a lookRead More …
The application of powder coating for wood furniture is developing rapidly
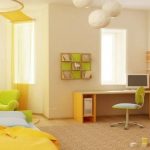
Powder coating has long been applied to metal substrates. In recent years through the industry’s continuous efforts to reduce the curing temperature, improve spraying technology, Powder coatings have been applied in MDF and other wood. Powder spraying can make the industrial application of wood products to minimize water loss and size changes, while the coating can achieve a higher gloss and bright color effect, meanwhile in the state of the more stringent VOC restrictions on the situation, provides a substituteRead More …
Preparation of Carboxylterminated for Fusion-bonded-epoxy Powder Coating
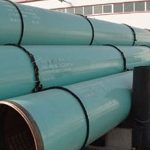
Preparation and Characterization of Carboxylterminated Poly (butadiene-co-acrylonitrile) -epoxy Resin Prepolymers for Fusion-bonded-epoxy Powder Coating 1 Introduction Fusion-bonded-epoxy (FBE) powder coatings which were first developed by 3M Co., are used widely when long-term corrosion protection is critical such as in the oil, metal, gas and water pipelines industries. However, the performance requirements for FBE powder coatings are challenging because of their high cross-linking density. The inherent brittleness of cured coatings is one of the major obstacles preventing wider application for epoxiesRead More …
Magical Light Decoration Is Created By Gold Nanoparticles Coating
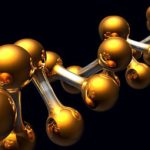
Recently, scientists from the University of California studyed and found that gold nanoparticles change colors when pressure occurs. It is understood that the scientist embedded the particles to the polymer film, film color is bright blue, but after pressure, it will turn red. However, if the pressure is not very large, the color would show purple. In other words, the color change of film may reflect the presure degree. In fact hundreds of years ago, artists started using gold nanoparticlesRead More …
Low Temperature Cure Powder Coatings For Heat-sensitive Substrates

Low Temperature Cure Powder Coatings For Heat-sensitive Substrates For application on heat-sensitive substrates like MDF, the powder must cure below 302°F (150°C) or even 212°F (100°C). Several approaches have been developed to achieve this goal, ranging from low-temperature-cure conventional chemistries to radiation-curable evolving chemistries. A vast number of published articles and patents have confirmed the ability of UV-curable technologies to produce glossy, smooth coatings on MDF within three to five minutes of process time.8The main advantages of UV-cured powders includeRead More …
What is Benefits of UV Powder Coating on Wood
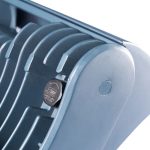
What is Benefits of UV Powder Coating on Wood UV powder coating technology offers a fast, clean and economic attractive method to achieve high-quality finishes on wood-based substrates. The coating process consists of the following steps: First the article is hung or placed onto a conveyor belt and the powder is sprayed electrostatically onto the object. Then the coated object enters the oven (temperatures of 90-140 degC are sufficient) where the powder melts and flows together to form a film.Read More …
The Use of Polyester Epoxy Combined Chemistry for UV Powder coating
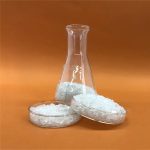
The combination of methacrylated polyester and acrylated epoxy resin offers an interesting blend of properties to the cured film. The presence of a polyester backbone results in good resistance of the coatings in weathering tests. The epoxy backbone gives outstanding chemical resistance, improved adhesion and smoothness. An attractive market segment for these UV powder coating is as replacement for PVC laminates on MDF panels for the furniture industry. The polyester/epoxy blend is achieved in four major steps. The polycondensation in theRead More …
Binder and Crosslinkers for UV Powder Coatings
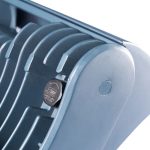
Binder and Crosslinkers for UV Powder Coatings The most suitable approach for a coating formulation is the use of a major binder and a crosslinker. The cross¬linker may control the network density for the coating, while the binder determines properties of the coating such as discoloration, outdoor stability, mechanical properties, etc. Furthermore, this approach will lead to a more homogenous concept in the powder coating applications as a category bringing similitude to thermosetting coatings where crosslinkers such as TGIC andRead More …
ASTM D7803-Standard for Preparing HDG steel for powder coatings
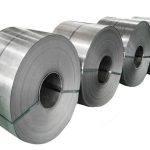
ASTM D7803 Bridges are one example of construction projects that are often built from hot-dip galvanized steel. How to coat this steel without adhesion failure of the powder system is explained in the new ASTM standard. The new standard, ASTM D7803, “Practice for Preparation of Zinc (Hot-Dip Galvanized)Coated Iron and Steel Product and Hardware Surfaces for Powder Coatings” covers surface preparation and thermal pretreatment of iron and steel products and hardware which have not been painted or powder coated previouslyRead More …
Coil coating is a continuous industrial process
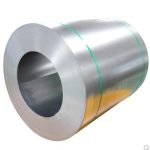
Coil coating is a continuous industrial process in which multiple layers of organic film are applied and cured on a moving metal strip. The paints used are liquid (solvent-based) and are generally composed of polyesters with acid- or hydroxy- endgroups able to crosslink with melamines or isocyanates to form a complete network with film properties that are tailored to the final application of the coated metal panel (building products, beverage cans, domestic appliances, etc.). The total film thickness is aroundRead More …
QUALICOAT SPECIFICATIONS for PAINT, LACQUER AND POWDER COATINGS
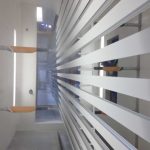
SPECIFICATIONS FOR A QUALITY LABEL FOR PAINT, LACQUER AND POWDER COATINGS ON ALUMINIUM FOR ARCHITECTURAL APPLICATIONS 12th Edition-MASTER VERSION approved by the QUALICOAT Executive Committee on 25.06.2009 Chapter 1 General Information 1. General Information These Specifications apply to the QUALICOAT quality label, which is a registered trademark. The regulations for use of the quality label are set out in Appendix A1. The aim of these Specifications is to establish minimum requirements which plant installations, coating materials and finished products mustRead More …