Category: Powder Coat Guide
Do you have powder coating questions about powder coating equipment,powder application,powder material?Do you have any doubt about your powder coat project, here a complete powder coat guide may help you find the satisfactory answer or solution.
Munsell Color System Description
Munsell Color System Description The Munsell color system was first established by the American painter and art teacher Albert H. Munsell around 1900, so it was named “Munsell color system”. The Munsell color system consists of five basic colors—red (R), yellow (Y), green (G), blue (B), and purple (P), plus five intermediate colors—yellow-red (YR). ), yellow-green (YG), blue-green (BG), blue-violet (BP), and red-violet (RP) as a reference. Each hue is subdivided into four colors, represented by the numbers 2.5, 5,Read More …
Pantone PMS Colors Chart Used For Printing and Powder Coating
Pantone PMS Colors Chart Pantone® Matching System Color Chart PMS Colors Used For Printing Use this guide to assist your color selection and specification process. This chart is a reference guide only. Pantone colors on computer screens may vary based on the graphics card and monitor used in your system. For true accuracy use the Pantone Color Publication.
How to Wipe Out Orange Peel During Electrostatic Powder Painting
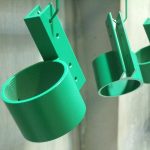
Achieving the right amount of electrostatic powder paint on the part is very important for durability reasons as well as eliminating orange peel. If you spray too little powder on the part, you will most likely end up with a grainy texture to the powder also known as “tight orange peel.” This is because there was not enough powder on the part for it to flow-out and create a uniform coating. Besides the poor aesthetics of this, the part willRead More …