Category: Powder Coat Guide
Do you have powder coating questions about powder coating equipment,powder application,powder material?Do you have any doubt about your powder coat project, here a complete powder coat guide may help you find the satisfactory answer or solution.
How To Increase the Scratch Resistance of Automotive Clear Coats
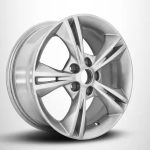
A New method to increase the scratch resistance of automotive clear coats A team of Iranian researchers have recently come up with a new method to increase the scratch resistance of automotive clear coats During the recent decades, there has been a great deal of efforts to improve the resistance of automotive clear coats against the abrasive and erosive wear. As a result, a number of techniques have been proposed for this purpose. A recent example of the latter involvesRead More …
Powder Coating Coverage Calculation
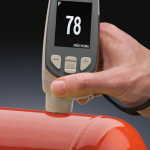
Powder Coating Coverage is very important to factor in the actual transfer efficiency that you will achieve. Estimators often find themselves scrambling to purchase more powder by not factoring in the correct transfer efficiency percentage.To evaluate the actual transfer efficiency of powder coating is very important. The following coverage table is helpful in estimating the amount of powder needed to coat a given amount of surface area. Theoretical coverage formulation Please note that the coverage of powder coating in theRead More …
How To Select A Proper Powder Coating for Your Products
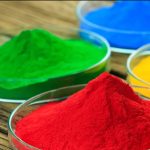
How To Select A Proper Powder Coating for Your Products Choice of resin system, hardener, and pigment is just the beginning in selection the properties that one may require of the finish. Control of gloss, smoothness, flow rate, cure rate, ultra violet resistance, chemical resistance, heat resistance, flexibility, adhesion, corrosion resistance, exterior durability, ability to be reclaimed and reused, total first time transfer efficiency, and more, are some of the factors that must be considered when any new material isRead More …
How to Prevent Powder Coating Caking
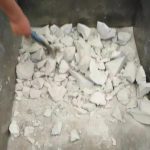
How to prevent powder coating caking Different resins having different glass transition temperatures , such as epoxy and polyester resin has a glass transition temperature of about 50 degrees Celsius, lightening agent ( 701 ) has a glass transition temperature of about 30 degrees Celsius, the liquid leveling agent in minus degrees Celsius. The larger the amount of material with low glass transition temperature the powder coating formulations contain ,the lower the glass transition temperature will become .Glass transition temperatureRead More …
Munsell Color Chart, Munsell Catalogue
Munsell Color Chart, Munsell Catalogue
Sublimation Transfer Process
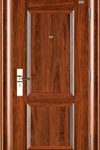
In order to apply the Sublimation Transfer Process , the following equipment and materials are required . A Special transfer equipment A Special sublimation powder coating powder to be sprayed and cured in a Coating Unit. Heat Transfer Paper or Film ( paper or plastic film carrying the desired effect printed with special sublimation inks. Working Process 1.Coating process: Using a sublimation powder coating,coating process in a standard coating unit consists of three different steps: pretreatment ,spraying powder,curing.The coating layerRead More …
Munsell Color System Description
Munsell Color System Description The Munsell color system was first established by the American painter and art teacher Albert H. Munsell around 1900, so it was named “Munsell color system”. The Munsell color system consists of five basic colors—red (R), yellow (Y), green (G), blue (B), and purple (P), plus five intermediate colors—yellow-red (YR). ), yellow-green (YG), blue-green (BG), blue-violet (BP), and red-violet (RP) as a reference. Each hue is subdivided into four colors, represented by the numbers 2.5, 5,Read More …
Why and How To Recoat Powder Coating
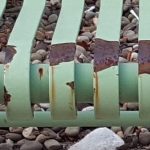
Recoat Powder Coating Applying a second coat of powder is the common approach to repair and reclaim rejected parts. However, the defect should be carefully analyzed and the source corrected before recoating. Do not recoat if the reject is caused from a fabrication defect, poor quality substrate, poor cleaning or pretreatment, or when the thickness of two coats together will be out of tolerance. Also, if the part is rejected due to undercure, it merely needs to be rebaked atRead More …
Plastic Terminology – English abbreviation AND full English name
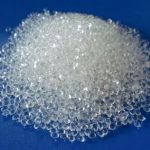
Plastic Terminology – English abbreviation AND full English name Abbreviation Full Name AAS Acrylonitrile-Bcry ate-styrene opolymer ABS Acrylonitrile-butadiene-styrene ALK Alkyd resin AMMA Acrylonitrile-methylmethacrylate copolymer AMS Alpha methyl styrene AS Acrylonitrile-styrene copolymer(see SAN) ASA Acrylonitrile styrene-acrylate copolymer(AAS) BMC Bulk moulding compound CA Cellulose acetate CAB Cellulose acetate butyrate CAP Cellulose acetate propionate CF Casein formaldehyde resin CFE Polychlorotrfluoroethylene(see PCTFE) CM Chlorinated polyethylene(see CPE) CMC Carboxymethyl cellulose CN Cellulose nitrate COPE Polyether ester elastomer CP Cellulose propionate(CAP) CPE Chlorinated polyethylene(PE-C) CPVC Chlorinated polyvinyl Chloride(PVC-C) CS Casein plastics CSM &cspr Chorosulfonated polyethylene CTA Cellulose triacetate DMC Dough moulding tompound E/P Ethylene propylene copolymer CA-MPR Elastomer alloy melt processable rubber EA-TPV Elastomer alloy thermoplastic vulcanizate EC Ethylene cellulose EEA Ethylene ethylacrylate copolymer EP Epoxide or epoxy(cured) EPDM Ethylene propylene diene terpolymer EPS Expandable polystyrene ETFE Ethylene/tetrafluoroethylene EVA Ethylene vinyl accetate copolymerRead More …
Eliminating Orange Peel During Powder Coating
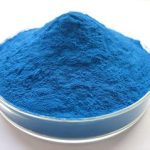
Achieving the right amount of electrostatic powder paint on the part is very important for durability reasons as well as eliminating orange peel. If you spray too little powder on the part, you will most likely end up with a grainy texture to the powder also known as “tight orange peel.” This is because there was not enough powder on the part for it to flow-out and create a uniform coating. Besides the poor aesthetics of this, the part willRead More …
Pantone PMS Colors Chart Used For Printing and Powder Coating
Pantone PMS Colors Chart Pantone® Matching System Color Chart PMS Colors Used For Printing Use this guide to assist your color selection and specification process. This chart is a reference guide only. Pantone colors on computer screens may vary based on the graphics card and monitor used in your system. For true accuracy use the Pantone Color Publication.
What is Powder Coating Process
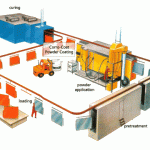
Powder Coating Process Pre-treatment – drying to remove water – spraying – Check – baking – check – Finished. 1.The characteristics of the powder coating can give full play to extend the coating life to break the painted surface first strictly surface pre-treatment. 2.Spray, was painted to be fully grounded in order to increase the efficiency of the powder coating of puffing. 3.The larger surface defects to be painted, coated scratch conductive putty, in order to ensure the formation ofRead More …
Solution of Poor Mechanical Properties and Chemical Resistance
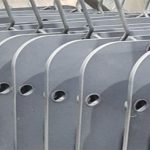
1.Poor Mechanical Properties and Chemical Resistance Cause: Too high or Too low curing temperature or timeSolution: Confirm and check with powder coating powder supplierCause:Oil,grease,extrusion oils,dust on the surfaceSolution:Optimize pretreatmentCause:Differing materials and material colorsSolution:Insufficient pretreatmentCause:Incompatible pretreatment and powder coatingSolution:Adjust pretreatment method,consult powder supplier 2.Greasy Surface(Haze like film on the surface which can be wiped off) Cause: Blooming effect-white film on the powder surface,which can be wiped offSolution:Change powder coating formula,increase curing temperatureCause: Insufficient air circulation in the ovenSolution:Increase air circulationCause: Contamination onRead More …
Conversion Coating of Galvanized Steel
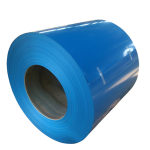
Iron phosphates or cleaner-coater products produce little or non-detectable conversion coatings on zinc surfaces. Many multimetal finishing lines use modified iron phosphates which offer cleaning, and leave micro-chemical etch on zinc substrates to provide adhesion properties. Many municipalities and states now have limits on zinc PPMs, forcing metal finishers to provide treatment of any solutions in which zinc substrates are processed. The zinc phosphate conversion coating is, perhaps, the highest quality coating that can be produced on a galvanized surface. ToRead More …
Corona and tribo charging technology
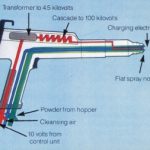
Understanding the differences between corona and tribo charging, assists in deciding which technology is best for an application. Each type of charging has typically been used for specific industries. Tribo charging has typically been used in industries which require epoxy powder or products that have intricate shapes. Insulating products such as electrical equipment that only require protective coating are prime users of tribo charging guns. This protective coating is generally;epoxy due to its tough finish. Also, industries such as wireRead More …
Necessary laboratory equipment for testing powder coating in application
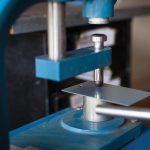
LABORATORY EQUIPMENT Equipment necessary for testing the pre-treatment chemicals, rinsing water and final results Tests of pre-treatment chemicals to be performed according to suppliers’ instructions Conductivity measurement gauge for evaluation of final rinse Temperature recorder Coating weight equipment, DIN 50939 or equal Equipment necessary for testing the powder coating Film thickness gauge suitable for use on aluminum (e.g. ISO 2360, DIN 50984) Cross hatch equipment, DIN-EN ISO 2409 – 2mm Bending test equipment, DIN-EN ISO 1519 Indentation test equipment, DIN-ENRead More …
Testing Methods for Powder Coating Application Process
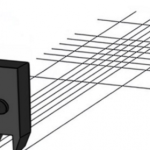
TESTING METHODS FOR POWDER COATING Testing methods are designed for two purposes: 1. Performance reliability ; 2. Quality control (1) GLOSS TEST (ASTM D523) Test coated flat panel with Gardener 60 degree meter. Coating shall not vary + or – 5% from data sheet requirements on each material supplied. (2) BENDING TEST (ASTM D522) Coating on .036 inch thick phosphated steel panel shall withstand 180 degree bend over 1/4″ mandrel. No crazing or loss of adhesion and finish at the bend beRead More …
Definitions for corrosion classification
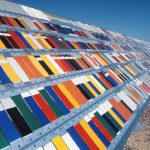
As an aid in finding what requirements should be made for pre-treatment, we can define different corrosion classification: Corrosion Class 0 Indoors with relative humidity over 60% Very little corrosion risk (aggressivity) CORROSION CLASS 1 Indoors in non-heated, well ventilated room Little corrosion risk (aggressivity) Corrosion Class 2 Indoors with fluctuating temperature and humidity. Outdoors in inland climates, far from sea and industry. Medium corrosion risk (aggressivity) CORROSION CLASS 3 In densely populated areas or near industrial areas. Above open waterRead More …
Powder Coating Storage And Handling
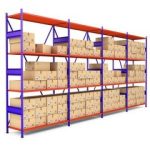
Powder Coating Storage And Handling Powder, like any coating material must be shipped, inventoried, and handled in its journey from the powder coating manufacturer to the point of application. Manufacturers’ recommendations, procedures, and cautions should be followed. Although various powders may have specific requirements, some universal rules apply. It is important that powders should always be: Protected from excess heat; Protected from humidity and water; Protected from contamination with foreign materials, such as other powders, dust, dirt, etc. These areRead More …
Quality Control of Powder Coating
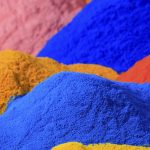
Quality Control Of Powder Coating Quality control in the finishing industry requires attention to more than just coating. In fact, the majority of problems occur for reasons other than coating faults. To assure quality where coating may be a factor, statistical process control (SPC) can be a useful tool. SPC SPC involves measuring the powder coating process using statistical methods and improving it to reduce variation at desired process levels. SPC can also help determine the difference between typical variationRead More …
Particle size distribution analsis for powder coating
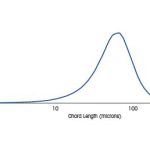
Particle size distribution analsis for powder coating laser particle size analyzer test results: Average particle size (median diameter), the boundary of particle size and particle size distribution of the dispersion. The average size of the sample is less than and greater than 50% of particles. The boundary particle size: closer to the common sense to the maximum and minimum particle size. However, the maximum and minimum particle size to describe the upper and lower limits of the sample particle sizeRead More …
What Cause The Burning Explosion of Powder Coating
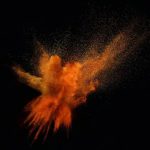
What Cause The Burning Explosion of Powder Coating The following aspects are the factors that lead to the burning explosion of powder coating (A) The dust concentration exceeds the lower limit Due to these reasons, the dust concentration in the powder room or workshop exceeds the lower explosion limit, thus forming the main conditions for powder burning explosion. If the ignition source is moderate, burning explosion are likely to occur (B) Powder and paint shop mixing In some factories, dueRead More …
Safe Storage Of Powder Coating
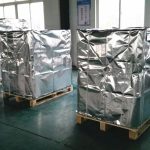
Proper storage for powder coating prevents particle agglomeration and reaction advancement, and ensures satisfactory application,this is pivotal. During application powder coatings must be easily fluidizable, free-flowing, and capable of accepting and maintaining a good electrostatic charges. Factors affecting powder coatings storage The key factors affecting powder coatings storage can be identified as: Temperature Moisture / Humidity Contamination Direct sunlight The recommended optimum conditions for storage of powder coating are: Temperature < 25°C Relative humidity 50 – 65% Away from directRead More …
How to Wipe Out Orange Peel During Electrostatic Powder Painting
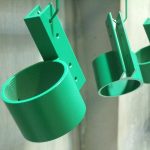
Achieving the right amount of electrostatic powder paint on the part is very important for durability reasons as well as eliminating orange peel. If you spray too little powder on the part, you will most likely end up with a grainy texture to the powder also known as “tight orange peel.” This is because there was not enough powder on the part for it to flow-out and create a uniform coating. Besides the poor aesthetics of this, the part willRead More …
Some Points to Know the Quality of The Powder Coating Powders
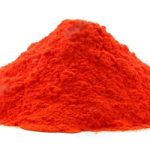
Exterior Appearance Identification: 1. Hand Feel: Should feel silky smooth,loose, floating, the more smooth loose of the powder, the better of the quality, on the contrary, powder feel rough and heavy, poor quality, not Easy spraying, powder falling twice more wastage. 2.Volume: The larger of the volume, the less filler of the powder coatings, the higher of the cost, the better the quality of the coating powders. On the contrary , the smaller of the volume, the higher content ofRead More …
What is Electrostatic Painting Process
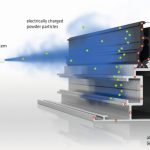
Electrostatic painting is a process in which a spray gun tip is electrostatically charged; making the paint charged electrically; thereby allowing the paint to be attracted to a grounded surface. This process wastes almost no paint through normal air flow, wind, or dripping. This is because the paint particles are actually attracted to the surface you are painting like a magnet. However, in order for the process to work the object you are painting has to be grounded. Electrostatic sprayingRead More …
How To Evaluate Coating Adhesion-Tape Test
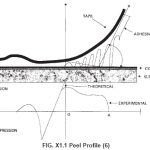
By far the most prevalent test for evaluating coating adhesion is the tape-and-peel test, which has been used since the 1930’s. In its simplest version a piece of adhesive tape is pressed against the paint film and the resistance to and degree of film removal observed when the tape is pulled off. Since an intact film with appreciable adhesion is frequently not removed at all, the severity of the test is usually enhanced by cutting into the film a figureRead More …