Author: doPowder
What is Dip Coating Process
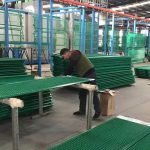
What is Dip Coating Process In a dip coating process, a substrate is dipped into a liquid coating solution and then is withdrawn from the solution at a controlled speed. Coating thickness generally increases with faster withdrawal speed. The thickness is determined by the balance of forces at the stagnation point on the liquid surface. A faster withdrawal speed pulls more fluid up onto the surface of the substrate before it has time to flow back down into the solution.Read More …
How To Increase the Scratch Resistance of Automotive Clear Coats
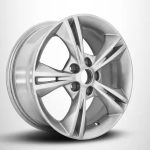
A New method to increase the scratch resistance of automotive clear coats A team of Iranian researchers have recently come up with a new method to increase the scratch resistance of automotive clear coats During the recent decades, there has been a great deal of efforts to improve the resistance of automotive clear coats against the abrasive and erosive wear. As a result, a number of techniques have been proposed for this purpose. A recent example of the latter involvesRead More …
How To Choose A Good Powder Coating Gun
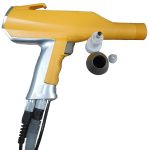
Powder coating electrostatic spray gun is mainly composed of powder supply bucket, powder spray gun and controller. It is a special spray gun for electrostatic spraying of powder coating powder, which is both a paint atomizer and an electrostatic electrode generator. Since its inception, powder coating has been widely used as an important means of surface treatment. Unlike traditional solvent-based coatings, powders do not emit polluting gases or liquids during the coating process. They are environmentally friendly to the processingRead More …
Fully understanding MDF powder coating

Powder coating on metal surfaces is well established, very stable and has good level control. To understand why MDF powder coating and metal surface powder coatings are so different, it is necessary to understand the inherent properties of MDF. It is generally believed that the main difference between metal and MDF is electrical conductivity. This may be true in terms of absolute conductivity values; however, it is not the most important factor for MDF powder coatings Typically, MDF powder coatingRead More …
Properties of Zinc Rich Primer
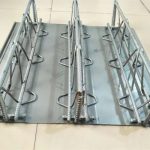
Properties of Zinc Rich Primer Zinc rich primer is a two pack system enriched with metallic zinc to provide outstanding performance in highly corrosive environment. Metallic Zinc imparts Cathodic protection to the base metal and Epoxide groups react with polyamide / Amine adduct hardener to form tough, non convertible film at ambient temp.It resists photo degradation by UV light as it contains UV absorber. RANGE OF APPLICATION Suitable for application as a priming coat on structural steel, pipelines, tank exteriorsRead More …
Antibacterial Epoxy Powder Coating
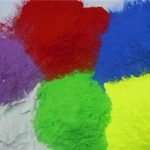
Antibacterial Epoxy Powder Coating Powder In the oil field oil and water pipelines, there are a lot of bacteria, especially sulfate-reducing bacteria, iron bacteria, the existence of saprophytic bacteria and multiply incessantly and pipe scale, and are subject to severe clogging and corrosion, a direct impact on oil production, oil and water injection. Oil field water pipelines, generally using the anti-corrosion of the steel pipe lined with cement mortar, the use of strong alkali in the cement mortar to inhibitRead More …
What is Epoxy Coatings
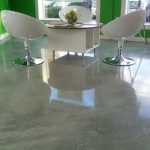
Epoxy-based coatings can be two-component systems (also named two part epoxy coating) or used as a powder coating. The two part epoxy coatings are used for high performance systems on metal substrate. They are a good alternative to powder coating formulations in industrial and automotive applications thanks to their low volatility and compatibility with waterborne formulations. Epoxy powder coating is widely used for metal coating in “white goods” applications like heaters and large appliances panels. Epoxy coating are also widely usedRead More …
Types of Matting Additives Used In Powder Coating or Paint
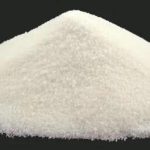
There are four Types of Matting additives Used In Powder Coating Powder or Paint. Silicas In the broad field of obtainable silicas for matting there are two groups which differ in terms of their production process. One is the hydro-thermal process, which produces silicas with a relatively soft morphology. By using the silica-gel process products can be obtained which have a harder morphology. Both processes are capable of producing standard silica and after treated products. After treatment means that theRead More …
Filiform corrosion is appearing mostly on aluminum
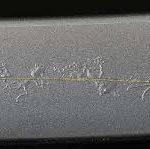
Filiform corrosion is special kind of corrosion appearing mostly on aluminum. The phenomenon resembles a worm creeping under the coating, always starting from a cut edge or a damage in the layer. Filiform corrosion develops easily when the coated object is exposed to salt in combination with temperatures 30/40°C and relative humidity 60-90%. This problem is therefore limited to coastal areas and linked with unfortunate combination of aluminum alloys and pre-treatment. To minimize filiform corrosions it is advised to ensureRead More …
Introduction of electrostatic spraying equipment
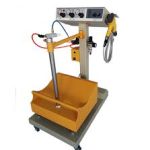
Electrostatic spraying equipment Dusting equipment electrostatic powder coating commonly known as “electrostatic spray”. The spray can be manual, automatic or manual + automatic. 100% of the spray material is a solid powder, the free powders can recycle the paint recycling rate up to 98%. Suspension of the transport system, a high degree of automation. The coated microporous less, good corrosion resistance, and can be a thick film. Electrostatic powder coating based on having an atomizing Tsui (the paint atomizing), andRead More …
What is Zinc Casting and Zinc Plating
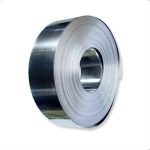
What is Zinc Casting and Zinc Plating ZINC:A bluish-white, metallic chemical element, usually found in combination such as in the zinc rich epoxy primer,used as a protective coating for iron, as a constituent in various alloys, as an electrode in electric batteries, and in the form of salts in medicines. Symbol Zn atomic weight = 65.38 atomic number = 30. Melts at 419.5 degrees C, or approx. 790 degrees F. ZINC CASTING:Zinc in a molten state is poured into aRead More …
How To Select A Proper Powder Coating for Your Products
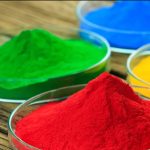
How To Select A Proper Powder Coating for Your Products Choice of resin system, hardener, and pigment is just the beginning in selection the properties that one may require of the finish. Control of gloss, smoothness, flow rate, cure rate, ultra violet resistance, chemical resistance, heat resistance, flexibility, adhesion, corrosion resistance, exterior durability, ability to be reclaimed and reused, total first time transfer efficiency, and more, are some of the factors that must be considered when any new material isRead More …
Application Method of Teflon Coating
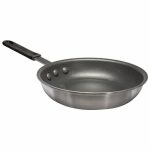
Application Method of Teflon Coating A Teflon coating has the ability to apply many other properties to the item it is being applied to. Of course Teflon’s non-stick properties are probably the most common ones desired, but there are a few other properties, like temperature-related properties, that might be the ones that are actually being sought. But whatever the property that is being sought from Teflon, there are a couple of methods of application: The surface of the item thatRead More …
How to Prevent Powder Coating Caking
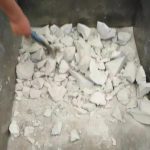
How to prevent powder coating caking Different resins having different glass transition temperatures , such as epoxy and polyester resin has a glass transition temperature of about 50 degrees Celsius, lightening agent ( 701 ) has a glass transition temperature of about 30 degrees Celsius, the liquid leveling agent in minus degrees Celsius. The larger the amount of material with low glass transition temperature the powder coating formulations contain ,the lower the glass transition temperature will become .Glass transition temperatureRead More …
Powder coating line matters MDF powder coating
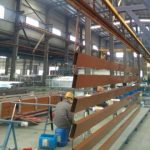
Powder coating line have proven to be the most important factor in obtaining high quality MDF powder coatings. Unfortunately for small metal surface powder coating companies, it is not possible to get high quality MDF powder coatings in old metal powder coating lines The most important part of the powder coating line is the oven technology oven paint melting. In case of thermal curing powder chemical curing. The thing to keep in mind is the low thermal conductivity of MDF.Read More …
Different types of titanium dioxide in different type powder coating
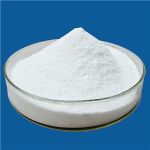
Entering the details of the competition in the powder coating industry, paint coatings are included in the investigation link. Polyester epoxy powder coatings improve the quality of the workmanship, and high titanium dioxides is important because we recognize that titanium dioxide dipolyester has become part of the quality of epoxy powder coating products. Polyester epoxy powder coating has become one of the most important products among many powder coating products due to its excellent performance. It is composed of polyesterRead More …
Chemical surface preparation before powder coating
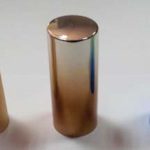
Chemical Surface Preparation Particular application is closely related to the nature of the surface being cleaned and the nature of the contamination. Most surfaces powder coated after cleaning are either galvanized steel, steel, or aluminum. Since not all chemical-type preparations are applicable to all these materials, the preparation process selected depends on the substrate material. For each material, the type of cleaning will be discussed and its unique features for that substrate will be explained. Specific application processes are quiteRead More …
Expanding Application area for UV powder coatings
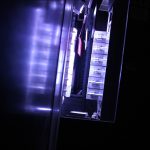
Expanding Application for UV powder coating. Blends of specific polyesters and epoxy resins have permitted the development of smooth, high-performance finishes for wood, metal, plastic and toner applications. Wood Smooth, matte clear coats have been successfully applied on hardwood and on veneered composite board, such as beech, ash and oak. The presence of the epoxy partner in the binder has boosted the chemical resistance of all the coatings tested. An attractive market segment for the advanced UV powder coating isRead More …
What is Powder Coating Process
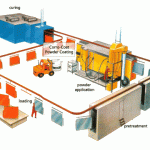
Powder Coating Process Pre-treatment – drying to remove water – spraying – Check – baking – check – Finished. 1.The characteristics of the powder coating can give full play to extend the coating life to break the painted surface first strictly surface pre-treatment. 2.Spray, was painted to be fully grounded in order to increase the efficiency of the powder coating of puffing. 3.The larger surface defects to be painted, coated scratch conductive putty, in order to ensure the formation ofRead More …
Solution of Poor Mechanical Properties and Chemical Resistance
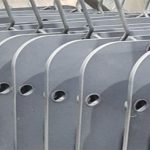
1.Poor Mechanical Properties and Chemical Resistance Cause: Too high or Too low curing temperature or timeSolution: Confirm and check with powder coating powder supplierCause:Oil,grease,extrusion oils,dust on the surfaceSolution:Optimize pretreatmentCause:Differing materials and material colorsSolution:Insufficient pretreatmentCause:Incompatible pretreatment and powder coatingSolution:Adjust pretreatment method,consult powder supplier 2.Greasy Surface(Haze like film on the surface which can be wiped off) Cause: Blooming effect-white film on the powder surface,which can be wiped offSolution:Change powder coating formula,increase curing temperatureCause: Insufficient air circulation in the ovenSolution:Increase air circulationCause: Contamination onRead More …
Cyclone Recycling and Filter Recycling in Powder Coating Powder Manufacturing
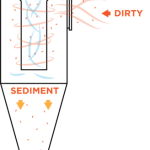
Cyclone Recycling and Filter Recycling in Powder Coating Powder Manufacturing Cyclone recycling Simple construction. Simple cleaning. Effectiveness of separation depends to a large extent on operating conditions. Can produce considerable waste. Filter recycling All powder is recycled. Accumulation of fine-grained particles. May produce problems with spraying process, particularly with friction charging. Extensive cleaning: filter change requirement between colors.
Functional Powder Coating:Insulated and Conductive Powder coatings
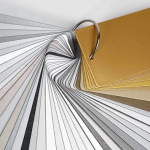
The powder coating is a new type of solvent-free 100% solid powder coating. Has a solvent-free, non-polluting, recyclable, environmentally friendly, saving energy and resources, and reduce labor intensity and the film mechanical strength. The coating form and the formation of the coating solids of up to 100%, because they do not use solvents, thereby reducing environmental pollution, conserve resources and recyclable characteristics. The functional powder coating is a special function, surface coating materials to provide for special purposes. It not onlyRead More …
Conversion Coating of Galvanized Steel
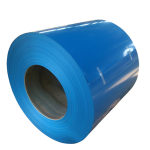
Iron phosphates or cleaner-coater products produce little or non-detectable conversion coatings on zinc surfaces. Many multimetal finishing lines use modified iron phosphates which offer cleaning, and leave micro-chemical etch on zinc substrates to provide adhesion properties. Many municipalities and states now have limits on zinc PPMs, forcing metal finishers to provide treatment of any solutions in which zinc substrates are processed. The zinc phosphate conversion coating is, perhaps, the highest quality coating that can be produced on a galvanized surface. ToRead More …
Iron oxides Use in High-temperature-cured Coatings
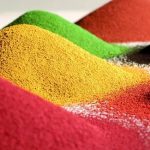
Standard yellow iron oxides are the ideal inorganic pigments to develop a wide range of color shades due to the advantages in performance and cost provided by their high hiding power and opacity, excellent weather, light and chemical fastness, and reduced price. But their use in high-temperature-cured coatings such as coil coating, powder coatings or stoving paints is limited. Why? When yellow iron oxides are submitted to high temperatures, their goethite structure (FeOOH) dehydrates and partially turns into hematite (Fe2O3),Read More …
Glycidyl Methacrylate GMA- TGIC Replacement Chemistries
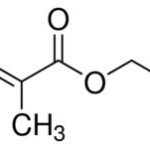
Glycidyl Methacrylate GMA- TGIC Replacement Chemistries Acrylic graft copolymers containing free glycidyl groups These hardeners,which include glycidyl methacrylate(GMA) curatives have recently been promoted as crosslinkers for carboxy polyester. Since the cure mechanism is an addition reaction, film builds that exceed 3 mils(75 um) are possible. So far, accelerated weathering tests of polyester GMA combinations indicate results similar to those of TGIC. Some formulating problems exist when acrylic graft copolymers are used ,for example, flow and leveling properties are relatively poor.Read More …