Methods of Applying Powder – ELECTROSTATIC SPRAYING
Posted by: doPowder | on January 29, 2022
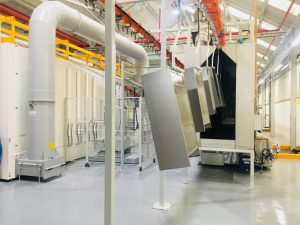
Electrostatic spraying is the most widely used method of applying powder coating materials. Its growth is increasing at an impressive rate. Developed in the mid 60’s , this process is the most efficient means of applying coatings and finishes in a short time. However, acceptance of powder coating in general was initially very slow in the US. In Europe, the electrostatic powder spray concept was accepted more readily, and the technology moved much faster there than else-where in the world. However, many advances were made in both powder materials and application equipment available to manufacturers. These advances generally involved problems associated with electrostatic powder spray coating, as well as improving functional operations of system components. As a result, there is a wide variety of electrostatic powder spray coatings systems available today.
To apply powder coating materials with the electrostatic powder spray process, five basic pieces of equipment are needed:
- Powder feeder unit;
- Electrostatic powder spray gun, or equivalent distribution device;
- Electrostatic voltage source;
- Powder recovery unit;
- Spray booth
There are other devices to enhance the operation of these basic components. In the operation of an electrostatic powder spray system, powder is siphoned, or pumped, from a feeder unit through a powder feed hose to the spray gun(s).Spray guns direct the powder toward the part in the form of a diffused cloud. Propelling force is provided both by air that transports powder from the feeder unit to the spray gun, and by the electrostatic charge imparted to the powder at the gun. Electrostatic voltage is supplied to the spray gun by a source designed to transmit high-voltage, low-amperage electrical power to an electrode(s) attached to the spray gun. As the diffused, electrostatically charged powder cloud nears the grounded part, an electrical field of attraction is created, drawing the powder particles to the part and creating a layer of powder. Overspray-or powder not adhering to the part-is collected for re-use or disposal. In the collector unit, powder is separated from the conveying airflow. Collected powder is then automatically or manually recycled back to the feeder unit to be resprayed. Air is passed through a filter media device into a clean-air plenum and then through a final, or absolute, filter back into the plant environment as clean air. The coated part is then carried from the application area and subjected to heat, which results in the flow out and curing of the powder material.
Economic Advantage
With electrostatic powder spray, up to 99% of the powder overspray can be recovered and reapplied. Material loss experienced with powder is minimal in comparison to liquid coating systems.
In addition, in most cases powder provides one-coat coverage without runs and sags on the finished part. Applying a primer coat prior to the finish coat is unnecessary, reducing time and labor required by multicoat liquid systems.
Reduced fuel cost in curing powder often results from the use of smaller ovens, shorter oven times and, in some cases, lower oven temperatures. There is no need to heat or temper booth makeup air since air is returned to the plant environment as clean air.
Other cost savings, including lower clean-up costs, can be attained with powder. There is no need to mix, recover, and dispose of solvents when coating with powder. Usually, no solvent or chemicals are used in cleaning either the powder application equipment or the spray booths. Since air and vacuum cleaners are generally all that is required for cleaning with powder, labor and cleaning materials are reduce and disposal of hazardous paint sludge is eliminated.
A large percentage of liquid coatings is comprised of sometimes toxic and flammable solvent that are lost in the application process. Shipment storage, and handling costs of solvents are usual very expensive. With powder, costs involving a pollution control equipment, flash-off time, and solvent waste disposal are virtually eliminated.
Eliminating solvent usage also can reduce fire insurance requirements as well as rates paid to maintain fire insurance protection. Finally the applied cost per mil per square foot of film is equivalent to, or lower than, liquid coating costs in most cases.
Ease of Application
The consistent finish characteristics and electrostatic “wraparound” realized in powder spray applications help reduce the need for highly skilled operators. In addition, there is no viscosity balance to maintain when coating with powder. Powder materials come “ready to spray” from the manufacturer. No flash-off time is required with powder. The coated part can be transported directly from the spray area to the oven for curing. Reject rates can be reduced, as can costs involved in reworking rejected parts. Runs and sags are usually eliminated with the powder coating process.
Insufficient or improper coating can be blown off the part (before heat curing) and recoated. This can eliminate the labor and costs involved in stripping, rehandling, recoating, and recuring rejected parts.Users are finding that the powder spray coating process is easily automated. It can utilize automatic gun movers, contouring mechanisms, robots, and stationary spray gun positioning. Total production time can often be reduced, or production volume increased, with powder spray coating. Eliminating various steps required with the liquid coating process can result in a more efficient finishing line.