Brief Introduction of Polyethylene Resin
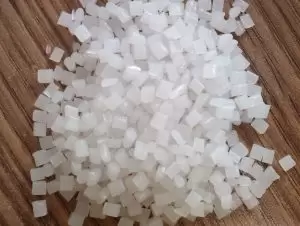
Brief Introduction of Polyethylene Resin
Polyethylene (PE) is a thermoplastic resin obtained by polymerizing ethylene. In industry, copolymers of ethylene with small amounts of alpha-olefins are also included. Polyethylene resin is odorless, non-toxic, feels like wax, has excellent low temperature resistance (minimum operating temperature can reach -100~-70°C), good chemical stability, and can resist most acid and alkali erosion (not resistant to oxidation nature acid). It is insoluble in common solvents at room temperature, with low water absorption and excellent electrical insulation.
Polyethylene was synthesized by the British ICI Company in 1922, and in 1933, the British Bonemen Chemical Industry Company found that ethylene could be polymerized to form polyethylene under high pressure. This method was industrialized in 1939 and is commonly known as the high pressure method. In 1953, K. Ziegler of the Federal Republic of Germany found that with TiCl4-Al(C2H5)3 as a catalyst, ethylene could also be polymerized under lower pressure. This method was put into industrial production in 1955 by the Hearst Company of the Federal Republic of Germany, and is commonly known as low pressure polyethylene. In the early 1950s, the Philips Petroleum Company of the United States discovered that using chromium oxide-silica alumina as a catalyst, ethylene could be polymerized to form high-density polyethylene under medium pressure, and industrial production was realized in 1957. In the 1960s, the Canadian DuPont Company began to make low-density polyethylene with ethylene and α-olefin by solution method. In 1977, Union Carbide Company and Dow Chemical Company of the United States successively used low-pressure method to make low-density polyethylene, called linear low-density polyethylene, of which the gas-phase method of Union Carbide Company was the most important. The performance of linear low density polyethylene is similar to that of low density polyethylene, and it has some characteristics of high density polyethylene. In addition, the energy consumption in production is low, so it has developed extremely rapidly and has become one of the most eye-catching new synthetic resins.
The core technology of the low pressure method lies in the catalyst. The TiCl4-Al(C2H5)3 system invented by Ziegler in Germany is the first-generation catalyst for polyolefins. In 1963, the Belgian Solvay Company pioneered the second-generation catalyst with magnesium compound as the carrier, and the catalytic efficiency reached tens of thousands to hundreds of thousands of grams of polyethylene per gram of titanium. The use of the second-generation catalyst can also save the post-treatment process for removing catalyst residues. Later, high-efficiency catalysts for the gas phase method were developed. In 1975, the Italian Monte Edison Group Corporation developed a catalyst that can directly produce spherical polyethylene without granulation. It is called the third-generation catalyst, which is another revolution in the production of high-density polyethylene.
Polyethylene resin is very sensitive to environmental stress (chemical and mechanical action) and is less resistant to thermal aging than polymers in terms of chemical structure and processing. Polyethylene can be processed by conventional thermoplastic molding methods. It has a wide range of uses, mainly used to manufacture films, packaging materials, containers, pipes, monofilaments, wires and cables, daily necessities, etc., and can be used as high-frequency insulating materials for TVs, radars, etc.
With the development of petrochemical industry, polyethylene production has developed rapidly, and the output accounts for about 1/4 of the total plastic output. In 1983, the world’s total polyethylene production capacity was 24.65 Mt, and the capacity of the units under construction was 3.16 Mt. According to the latest statistics in 2011, the global production capacity reached 96 Mt. The development trend of polyethylene production shows that production and consumption are gradually shifting to Asia, and China is increasingly becoming the most important consumer market.