Author: doPowder
Factors affecting measurement uncertainty -ISO 2360
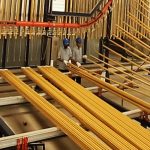
Measurement of coating thickness INTERNATIONAL STANDARD ISO 2360 5 Factors affecting measurement uncertainty 5.1 Coating thickness A measurement uncertainty is inherent in the method. For thin coatings, this measurement uncertainty (in absolute terms) is constant, independent of the coating thickness and, for a single measurement, is at least 0,5μm. For coatings thicker than 25 μm, the uncertainty becomes relative to the thickness and is approximately a constant fraction of that thickness. For measuring coating thicknesses of 5 μm or less,Read More …
Measurement of coating thickness – ISO 2360:2003 -Part 1
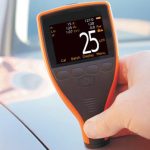
Non-conductive coatings on non-magnetic electrically conductive basis materials — Measurement of coating thickness — Amplitude-sensitive eddy current method INTERNATIONAL STANDARD ISO 2360 Third edition 1 Scope This International Standard describes a method for non-destructive measurements of the thickness of non-conductive coatings on non-magnetic, electrically conductive (generally metallic) basis materials, using amplitude-sensitive eddy current instruments. NOTE This method can also be used to measure non-magnetic metallic coatings on non-conductive basis materials. The method is particularly applicable to measurements of the thicknessRead More …
The key properties of each generic type of thermosetting powder coating
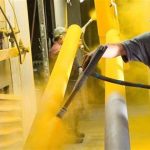
Properties of each generic type of thermosetting powder coating Industrial finishes are custom formulated to individual and end-user requirements. Successful selection depends on a close working relationship between users and suppliers. Selection should be strictly on a demonstrated film performance basis. This is because the film performance of a thermosetting powder coating is completely dependent on the bake it receives in a particular plant, on a particular substrate, with a particular degree of cleanliness, and type of metal pretreatment. ManyRead More …
Characteristics of electrostatic powder coating spraying
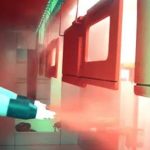
Characteristics of electrostatic powder coating spraying Electrostatic powder coating spraying because he does not use the solvent will not cause solvent pollution in the atmosphere, while avoiding the danger of fire due to the solvent, is also easy to transport and storage of raw materials. The spraying process, the overspray powder is not coated on the workpiece can be recovered, the recovery rate of up to more than 95%, to improve the utilization of raw materials, to reduce the materialRead More …
Characteristics of the electrostatic spraying
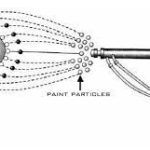
Generally speaking, where does not occur at 200 ℃ deformation, enables the charged powder particles are adsorbed on the surface to be painted, the surface coating can be by electrostatic powder spraying. Therefore, electrostatic powder coating spraying technology can be widely used instruments, household appliances, mechanical and electrical equipment, automobile and shipbuilding, light industry equipment, furniture, machinery and building materials, and other metal parts of the surface protection and decorative painting. View from currently used in spray technology, electrostatic powderRead More …
What is general mechanical properties of powder coatings
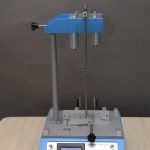
The general mechanical properties of powder coatings include the following. Cross-cut Test (adhesion) Flexibility Erichsen Buchholz Hardness Pencil Hardness Clemen Hardness Impact Cross-cut Test (adhesion) According the standards ISO 2409, ASTM D3359 or DIN 53151. On the coated test panel a cross-cut (indentations in the form of a cross and parallel to each other with a mutual distance of 1 mm or 2 mm) is made on the metal. A standard tape is put on the cross-cut. The cross-cut isRead More …
How to Remove Powder Coating
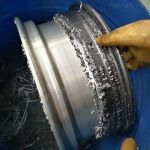
Many methods have been used to remove powder coating from production hooks,racks,and fixtures. Abrasive-media blasting Burn-off ovens Abrasive-media blasting Benefits. Abrasive-media blasting is a common method used in the finishing industry to clean electro-deposition and powder coatings deposits from racks. Abrasive-media blasting provides adequate cleaning and coating removal. One of the benefits of rack cleaning with abrasive media is any rust or oxidation that may be present is removed with the coating, and this is accomplished at ambient, or room, temperature. Concerns. UsingRead More …
The main advantages of NCS Natural Color System
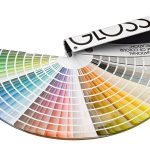
Natural Color System ( NCS ) is the first choice for professionals engaged in sales, promotion and production in various industries.It is also the first choice for daily work of users such as designers, architects and teachers. Universal color language The colors described by the NCS system are consistent with those seen by our eyes and are not limited by language, materials, and culture. In the NCS system, we can define any surface color, and no matter what material isRead More …
Clear Powder coating versus Liquid paint on Aluminum Wheels
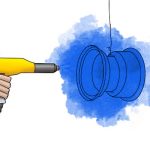
Clear liquid polyurethane coatings are used quite extensively in the automotive industry. They’re primarily used as the clear coat, top coat found on most cars and are formulated to be very durable. Clear powder coating have not yet gained recognition in this area primarily due to aesthetic reasons. Clear powder coating are used quit extensively by automotive wheel manufacturers, are durable and can be very cost-effective Powder coating application requires special electrostatic spray guns, and an oven to melt andRead More …
Phosphate Coatings Pretreatment for Steel Substrates
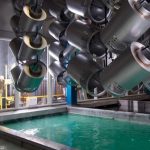
Phosphate Coatings Pretreatment for Steel Substrates The recognised pre-treatment for steel substrates just prior to application of powder is phosphating which can vary in coating weight. The greater the conversion coating weight the greater the degree of corrosion resistance achieved; the lower the coating weight the better the mechanical properties. It is therefore necessary to select a compromise between mechanical properties and corrosion resistance. High phosphate coating weights can give trouble with powder coatings in that crystal fracture can occurRead More …
Test for edge effect – ISO2360 2003
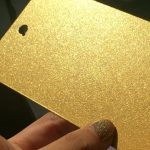
ISO2360 2003 A simple edge effect test, to assess the effect of the proximity of an edge, consists in using a clean uncoated sample of the basis metal as follows. The procedure is illustrated in Figure B.1. Step 1Place the probe on the sample, well away from the edge. Step 2Adjust the instrument to read zero. Step 3Progressively bring the probe towards the edge and note where a change of the instrument reading occurs with respect to the expected uncertaintyRead More …
Alkaline Acid Cleaners of CLEANING ALUMINUM
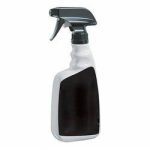
Cleaners of CLEANING ALUMINUM Alkaline Cleaners Alkaline cleaners for aluminum differ from those used for steel; they usually have a blend of mild alkaline salts to avoid attacking the aluminum surface. In some cases, a small to moderate amount of free caustic soda may be present in the cleaner to remove difficult soils, or to provide a desired etch. In the power spray method of application, the parts to be cleaned are suspended in a tunnel while the cleaning solutionRead More …
UV powder coatings bring the benefits to heat sensitive substrates

UV powder coatings bring the benefits to heat sensitive substrates Powder coating provides a durable, attractive and economical alternative to liquid paints and laminates for a wide range of heat-sensitive products such as glass and plastic materials. Powder coatings are dry, 100 percent solids paints that are spray-applied in a process similar to liquid painting. Once coated, products are conveyed through a curing oven, where the powder melts to form a durable, attractive finish. Powder coatings have long been theRead More …
Some HEAT-SENSITIVE SUBSTRATES in coatings industry

HEAT-SENSITIVE SUBSTRATES in coatings industry In recent years, ongoing research and development has been devoted to formulating powder coating powder that can cure at low temperatures, below 212ºF, without compromising durability or quality. These powders can be used on temperature-sensitive materials, as well as on massive parts that require enormous amounts of energy with other curing systems. Wood materials such as particle board and fiberboard, as well as glass and plastic products, can now benefit from a powder coated finishRead More …
How to maintenance cure oven in powder coating
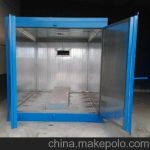
Monthly maintenance and inspection schedule for cure oven in powder coating include the following aspects. Fuel safety shutoff valves These valves stop the fuel supply in an emergency. Check all manual and motorized fuel valves to see if they are operating properly. Fan and airflow interlocks Now is the time to inspect the air switches that regulate air movement and fan operation . These devices assure that that the oven is purged properly before ignition. They also assure that theRead More …
Weekly maintenance for powder coating oven
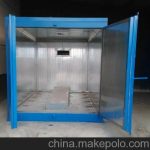
How to Weekly maintenance for powder coating oven Burner blower impeller and motor The cleanliness of the fan impeller directly affects burner blower efficiency . Periodic cleaning keeps the blower in good condition,preventing premature bearing failure. Keep blower motors clean to avoid overheating, which can cause electrical failure. By simply removing dirt buildup on the motor housing and cooling fins, you can eliminate costly motor replacement. Heater shell interior Now is a good time to check the heater shell, orRead More …
Powder Coating Storage and Transportation in Summer
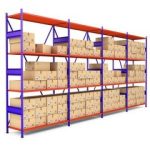
Powder Coating Storage and Transportation in Summer With the advent of summer, powder caking is a problem for many manufacturers. In addition to the process problems in the production process, storage and transportation are factors that affect the final spraying results. In summer, the temperature and humidity is high, and directly affect the final coating quality of the powder coating. The first is the effect of temperature, powder coatings must maintain their particle size in order to operate and use.Read More …
Paint Removal, How To Removal Paint
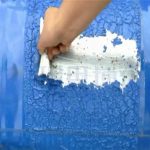
How To Removal Paint When repainting a part,prior to application of the new paint coat the old,paint often must be removed. The waste reduction assessment should start by examining what causes the need for repainting: inadequate initial part preparation; defects in coating application; equipment problems; or coating damage due to improper handling. While no process is perfect, reducing the need for repainting has a direct effect on the volume of waste generated from paint removal. Once the need for paintRead More …
Thermosetting powder coating are much more widely used
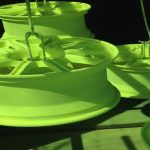
Thermosetting powder coating are applied by the electrostatic spray process, heated to the necessary temperatureand cured and are primarily composed of relatively high molecular weightsolid resins and a crosslinker.The formulation of thermosetting powders contain the primary resins:Epoxy,Polyester,Acrylic. These primary resins are used with different crosslinkers to produce a variety of powder materials. Many crosslinkers, or cure agents, are used in powder coatings, including amines, anhydrides, melamines, and blocked or non-blocked isocyanates.Some materials also use more than one resin in hybridRead More …
What is the application of calcium carbonate in paints?
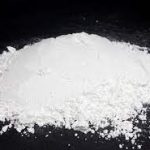
Calcium carbonate is a non-toxic, odorless, non-irritating white powder and one of the most versatile inorganic fillers. Calcium carbonate is neutral, substantially insoluble in water and soluble in acid. According to different calcium carbonate production methods, calcium carbonate can be divided into heavy calcium carbonate and light carbon. Calcium acid, colloidal calcium carbonate and crystalline calcium carbonate. Calcium carbonate is a common substance on the earth. It is found in rocks such as vermiculite, calcite, chalk, limestone, marble, travertine, etc.Read More …
Repair of parts and hanger stripping in powder coating
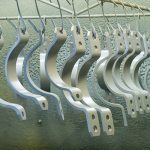
The methods of part repair after powder coating can be put into two categories : touch-up and recoat. Touch-up repair is appropriate when a small area of the coated part is not covered and is unable to meet finishing specifications. When hanger marks are not acceptable, touch-up is required. Touch-up also may be used to repair slight damage from handling, machining, or welding during assembly. Recoat is required when a part is rejected because of a large surface area defectRead More …
The market for electronic components protective coatings exceed US$20 billion In 2025
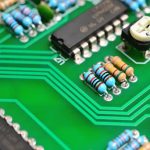
A new report from GlobalMarketInsight Inc. shows that by 2025, the market for protective coatings for electronic components will exceed $20 billion. Electronic component protective coatings are polymers used on printed circuit boards (PCBs) to electrically insulate and protect components from environmental stresses such as moisture, chemicals, dust, and debris. These coatings can be applied using spray techniques such as brushing, dipping, manual spraying or automatic spraying. Increased use of portable electronic products, increased demand for automotive electronics applications, andRead More …
NCS is short for Natural Color System
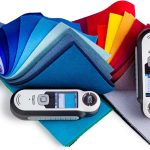
NCS Introduction NCS is short for Natural Color System. It is the world’s most prestigious color system and the most widely used international color standard and color communication language in practice. It is the highest color quality standard required available internationally. NCS natural color system has been widely used in many fields such as color research and education, planning and design, industry and production, corporate image, commerce, and so on. It is used in many industries such as textiles, clothing,Read More …
Future development prospects of hydrophobic paint
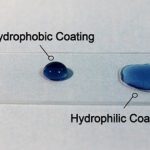
Hydrophobic paint often refer to a class of low surface energy coatings where the static water contact angle θ of the coating on a smooth surface is greater than 90°, whereas superhydrophobic paint are a new type of coating with special surface properties, meaning water contact with a solid coating. The angle is greater than 150° and often means that the water contact angle lag is less than 5°. From 2017 to 2022, the hydrophobic paint market will grow atRead More …
Application of Self-Healing Coating Technology in Powder Coatings
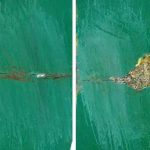
Since 2017, many new chemical suppliers entering the powder coating industry provided new assistance for the advancement of powder coating technology. The coating self-healing technology from Autonomic Materials Inc. (AMI) provides a solution to the increased corrosion resistance of epoxy powder coatings.The coating self-healing technology is based on a microcapsule with a core-shell structure developed by AMI and can be repaired when the coating is damaged. This microcapsule is post-mixed In the preparation of powder coating process . Once theRead More …
New technologies for corona and tribo gun
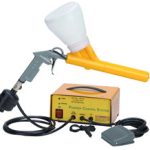
Equipment manufacturers have tried many different guns and nozzles to optimize the coating process over the years. However, most new technologies are developed to meet the needs of specific market requirements. A corona gun technology that has been used in different forms is the grounding ring or sleeve. This grounding ring is usually located either inside or outside the gun at some distance from the electrode and opposite the product being coated. It can be located on the gun itselfRead More …