Author: doPowder
Manufacturers apply electrostatic powder coating to many types of products
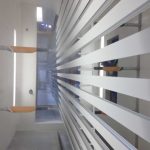
Manufacturers may apply an electrostatic powder coating to many types of products. This type of finish is primarily used on metals ranging from steel to aluminum. It’s also used to finish a variety of consumer goods, from wire shelving to lawn furniture. Electrostatic powder coating is also used on cars and other vehicles, and remains a popular method of finishing exterior metal siding This product may contain a variety of materials, depending on the product and manufacturer. Many include anRead More …
Controlling the moisture content in the MDF is critical

The powder coating process requires an electrostatic charge for the powder to attract to the wood while using a premium grade MDF. This electrostatic charge is created by heating the wood to bring the moisture content to the surface, since it is this moisture that serves as the electrostatic conductor.The adhesion of the powder to the board is so strong that to remove the powder finish from the board it is likely the MDF board substrate will chip off beforeRead More …
Kinds of Phosphate Treatment for Powder Coating
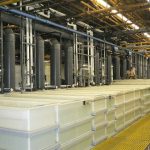
Kinds of Phosphate treatment for powder coating Iron phosphate Treatment with iron phosphate (often called thin layer phosphating) provides very good adhesion properties and has no adverse effects in the mechanical properties of the powder coating. Iron phosphate provides good corrosion protection for exposure in the low and middle corrosion classes, though it cannot compete with zinc phosphate in this respect. Iron phosphate can be used in either spray or dip facilities. The number of steps in the process mayRead More …
What is ABS plastic coating
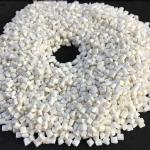
ABS plastic coating ABS plastic Department of butadiene – acrylonitrile – styrene terpolymer, widely used in the production of home appliances products, housing and automobile and motorcycle parts. Ketone, benzene and ester solvent capable of dissolving ABS plastic, alcohol and hydrocarbon solvent dissolution of ABS plastic, so the general use of ethanol – isopropanol solvent for surface treatment, usually air spraying or electrostatic spraying process for construction . ABS plastic coating paints a wide range of options-based thermoplastic acrylic coatings,Read More …
Some Important factors to polyester coating degradation
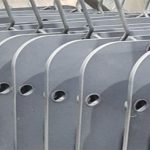
Polyester degradation is affected by solar radiation, photocatalytic admixtures, water and moisture, chemicals, oxygen, ozone, temperature, abrasion, internal and external stress, and pigment fading.Out of all these, the following factors, all present in outdoor weathering, are the most important to coating degradation: moisture, temperatures, oxidation ,UV radiation. Moisture Hydrolysis occurs when a plastic is exposed to water or humidity.This chemical reaction may be a major factor in the degradation of condensation polymers such as polyesters , where the ester groupRead More …
Classification of Adhesion Test Results-ASTM D3359-02
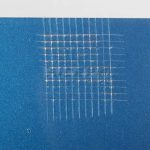
Inspect the grid area for removal of coating from the substrate or from a previous coating using the illuminated magnifier. Rate the adhesion in accordance with the following scale illustrated in Fig. 1: 5B The edges of the cuts are completely smooth; none of the squares of the lattice is detached. 4B Small flakes of the coating are detached at intersections; less than 5 % of the area is affected. 3B Small flakes of the coating are detached along edgesRead More …
TEST METHOD-CROSS-CUT TAPE TEST-ASTM D3359-02
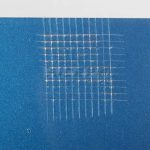
TEST METHOD-CROSS-CUT TAPE TEST-ASTM D3359-02 10. Apparatus and Materials 10.1 Cutting Tool9—Sharp razor blade, scalpel, knife or other cutting device having a cutting edge angle between 15 and 30° that will make either a single cut or several cuts at once. It is of particular importance that the cutting edge or edges be in good condition. 10.2 Cutting Guide—If cuts are made manually (as opposed to a mechanical apparatus) a steel or other hard metal straightedge or template to ensureRead More …
Use of Zinc Rich Primer for steel and ferrous metals
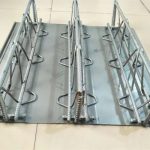
Use of Zinc Rich Primer for steel and ferrous metals Zinc Rich Primer is an organic zinc rich primer for steel and ferrous metals that combines the resistance properties of epoxy and the galvanic protection of zinc.This is a pure zinc epoxy base one-package primer. This high performance epoxy compound fuses zinc to the metal substrate and protects against corrosion equal to Hot Dip Galvanizing (meets and exceeds ASTM A780 specification for touch-up and repair of Hot Dip Galvanize). ClearcoRead More …
Introduction of Fusion bonded epoxy powder coating
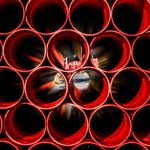
Fusion bonded epoxy coating, also known as fusion-bond epoxy powder coating and commonly referred to as FBE coating, is an epoxy based powder coating that is widely used to protect steel pipe used in pipeline construction, concrete reinforcing bars (rebar) and on a wide variety of piping connections, valves etc. from corrosion. FBE coatings are thermoset polymer coatings. They come under the category of ‘protective coatings’ in paints and coating nomenclature. The name ‘fusion-bond epoxy’ is due to resin cross-linking andRead More …
Optimal Performance of UV Powder Coatings
Powder coating cured by ultraviolet light (UV powder coating) is a technology that combines the advantages of thermosetting powder coating with those of liquid ultraviolet-cure coating technology. The difference from standard powder coating is that melting and curing are separated into two distinct processes: upon exposure to heat, UV-curable powder coating particles melt and flow into a homogeneous film that is crosslinked only when it is exposed to UV light. The most popular crosslinking mechanism used for this technology isRead More …
Thermosetting powder coating and thermoplastic powder coating
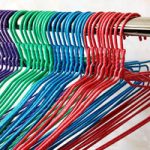
Powder coating is a type of coating that is applied as a free-flowing, dry powder. The main difference between a conventional liquid paint and a powder coating is that the powder coating does not require a solvent to keep the binder and filler parts in a liquid suspension form. The coating is typically applied electrostatically and is then cured under heat to allow it to flow and form a “skin”.They are applied as a dry material and they contain veryRead More …
Methods are used to capture overspray during powder coating
Three basic methods are used to capture over sprayed powder coating powder:Cascade (also known as a water wash),Baffle, and Media filtration. Many modern high volume spray booths incorporate one or more of these methods of source capture in an effort to improve overall removal efficiency. One of the most common combination systems, is a cascade style booth, with multi-stage media filtration, prior to the exhaust stack, or prior to a VOC control technology like an RTO (regenerative thermal oxidizer). Anyone that looks behindRead More …
What is Manganese phosphate coating
Manganese phosphate coating has the highest hardness and superior corrosion and wear resistances of general phosphate coatings. Manganese phosphating is extensively employed to improve the sliding properties of engine, gear, and power transmission systems. The use of manganese phosphated coatings for improved corrosion resistance can be found in virtually all branches of the metal working-industry. Typical examples mentioned here include motor vehicle components in brake and clutch assemblies, engine components, leaf or coil springs, drill bits, screws, nuts and bolts,Read More …
Chromate coating for aluminium surface
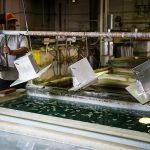
Aluminium and aluminium alloys are treated by a corrosion resistant conversion coating that is called “chromate coating” or “chromating”. General method is to clean the aluminium surface and then apply an acidic chromium composition on that clean surface. Chromium conversion coatings are highly corrosion resistant and provide excellent retention of subsequent coatings. Different type of subsequent coatings can be applied to the chromate conversion coating to produce an acceptable surface. What we call as phosphating to steel an iron isRead More …
Zinc phosphate and its applications
Generally zinc phosphate conversion coating is used to provide long lasting corrosion protection. Almost all automotive industries use this type of conversion coating. It is suitable for the products come against hard weather conditions. Coating quality is better than iron phosphate coating. It forms 2 – 5 gr/m² coating on the metal surface when used as under paint. Application, set up and control of this process are more difficult than other methods and can be applied by immersion or spray.Read More …
What is Zinc Phosphate Coatings
Zinc phosphate coating is preffered in case of requirement of higher corrosion resistance than iron phosphate. It can be used as base for paintings (especially for thermosetting powder coating), before cold drawing / cold forming of steel and prior application of protective oil / lubrication. This is often the method chosen when long life under corrosive conditions is required. Coating is also very good with zinc phosphate because the crystals form a porous surface which can soak up and mechanicallyRead More …
What is Phosphate coatings
Phosphate coatings are used to increase corrosion resistance and improve powder paint adhesion,and are used on steel parts for corrosion resistance, lubricity, or as a foundation for subsequent coatings or painting.It serves as a conversion coating in which a dilute solution of phosphoric acid and phosphate salts is applied via spraying or immersion and chemically reacts with the surface of the part being coated to form a layer of insoluble, crystalline phosphates.Phosphate conversion coatings can also be used on aluminium,Read More …
Fluid Bed Powder Coating Application Process
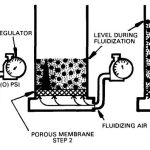
Fluid bed powder coating consists of immersing a hot part into a bed of powder, allowing the powder to melt on the part and build a film, and subsequently providing enough time and heat for this film to flow into a continuous coating. The part should be immersed in the fluidized bed as quickly as possible after removing it from the preheat oven to keep heat loss at a minimum. A time cycle should be established to keep this timeRead More …
What are the common fluidized bed powder coating process parameters?
There are no common parameters in the process of fluidized bed powder coating since it changes dramatically with part thickness. Two-inch thick bar stock can be coated with functionalized polyethylene by preheating to 250°F, dip coated and will most likely flow out without any post heating. Conversely, thin expanded metal may have to be preheated to 450°F to achieve the desired coating thickness, and then post heated at 350°F for four minutes to complete the flow out. We have neverRead More …
Brief introduction of fluidized bed powder coating
The fluidized bed powder coating system has three main sections. A top powder hopper where the powder is held, a porous plate which allows air to pass through, and a sealed bottom air chamber. When pressurized air is blown into the air chamber it passes through the plate and causes the powder to float or “fluidize”. This allows the metal part to be coated to be moved through the powder with little resistance. Fluidized bed application is accomplished by preheatingRead More …
Acrylic hybrids combine the acrylic resin with an epoxy binder.
They are somewhat better than a epoxy-polyester / hybrid but still not considered acceptable for outdoor use. The mechanical properties that are characteristic in epoxies are a benefit of these materials and they have much better flexibility than other acrylics. Because of their good appearance, tough surface, exceptional weatherability, and excellent electrostatic application characteristics, acrylics are frequently used for applications on products that have very high quality standards. Appliances, automobiles and other products that require durability and long life inRead More …
Adhesion problem of powder coating application
Poor adhesion is usually related to poor pretreatment or under cure. Undercure -Run an electronic temperature recording device with a probe on the part to ensure that the metal temperature reaches the prescribed cure index (Time at temperature). Pretreatment – Perform regular titration and quality checks to avoid a pretreatment problem.Surface preparation is probably the cause of the poor adhesion of the powder coating powder. Not all stainless steels accept phosphate pretreatments to the same extent; some being more reactiveRead More …
Advantages of wood powder coating on wood furniture
Several furniture and cabinetry manufacturers have had success with wood powder coating MDF. Pigmented powder applications to MDF have been developed and used more extensively than coating of natural wood, or clear coating of MDF. Establishing a new system may require significant research and production trials to achieve desired process efficiency and final product quality. Powder coatings has a high transfer efficiency, reduced (or no) emissions, one-step, one-coat process, elimination of edge banding, significant reduction of exhaust and oven ventilation air,Read More …
How to Powder Coat on Wood Products
Some woods and wood products such as MDF have sufficient and consistent moisture content to provide conductivity and can be coated directly. To enhance electrostatic attraction, wood can be pretreated with a spray solution that provides a conductive surface.The part is then preheated to a desired coating temperature, which softens or partially melts the powder when it is applied and helps the powder adhere to the part where it melts a little on impact.A uniform board surface temperature allows forRead More …
Powder coating over non-metal products such as plastic wood
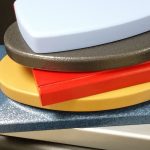
Over the last twenty years, powder coating has revolutionized the finishing industry by providing a superior, durable, environmentally friendly finish, particularly for metal products such as appliances, automotive parts, sporting goods and countless other products.However with the development of powder coatings that can be applied and cured at low temperatures,the market has opened to heat sensitive substrates such as plastics and wood. Radiation curing (UV or electron beam) allows the curing of powder on heat sensitive substrates by reducing theRead More …
Advantages of UV powder coating systems
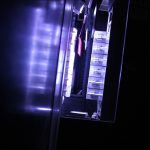
UV powder coating powder formulations consist of:UV powder resin,Photoinitiator,Additives,Pigment / extenders. Curing of powder coatings with UV light can be described as “the best of two worlds”. This new method makes it possible to benefit from the advantages of high cure speed and low cure temperature as well as environmental friendliness. The main advantages of UV curable powder systems are: Low system costs Application of one layer Maximum powder use with overspray recycling Low cure temperature High cure speed HardlyRead More …
Requirements for powder coating over hot dip galvanizing
The following specification is recommended: Use zinc phosphate pretreatment if highest adhesion is required. Surface must be perfectly clean. Zinc phosphate has no detergent action and will not remove oil or soil. Use iron phosphate if standard performance is required. Iron phosphate has a slight detergent action and will remove small amounts of surface contamination. Best used for pre-galvanized products. Pre-heat work prior to powder application. Use ‘degassing’ grade polyester powder coating only . Check for correct curing by solventRead More …
Solutions for the problems of powder coating over hot dip galvanizing
1. Incomplete curing: Polyester powder coating powder is thermosetting resins that cross-link to their final organic form by being maintained at a temperature (typically 180 o C), for about 10 minutes. Curing ovens are designed to provide this time at temperature combination. With hot dip galvanized items, with their heavier section thickness, it is necessary to ensure that sufficient stoving time is allowed to meet the curing specifications. Pre-heating of the heavier work will assist in accelerating the curing processRead More …