قسم: پاؤڈر کوٹ گائیڈ
کیا آپ کے پاس پاؤڈر کوٹنگ کے سامان، پاؤڈر کی درخواست، پاؤڈر مواد کے بارے میں پاؤڈر کوٹنگ کے سوالات ہیں؟ کیا آپ کو اپنے پاؤڈر کوٹ پروجیکٹ کے بارے میں کوئی شک ہے، یہاں ایک مکمل پاؤڈر کوٹ گائیڈ آپ کو تسلی بخش جواب یا حل تلاش کرنے میں مدد کر سکتا ہے۔
آٹوموٹو کلیئر کوٹس کی سکریچ مزاحمت کو کیسے بڑھایا جائے۔
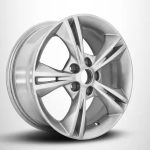
آٹوموٹو کلیئر کوٹس کی خراش مزاحمت کو بڑھانے کے لیے ایک نیا طریقہ ایرانی محققین کی ایک ٹیم نے حال ہی میں آٹوموٹیو کلیئر کوٹ کی خراش مزاحمت کو بڑھانے کے لیے ایک نیا طریقہ پیش کیا ہے، حالیہ دہائیوں کے دوران، اس کو بہتر بنانے کے لیے کافی کوششیں کی گئی ہیں۔ کھرچنے اور کٹاؤ والے لباس کے خلاف آٹوموٹو صاف کوٹ کی مزاحمت۔ نتیجے کے طور پر، اس مقصد کے لئے کئی تکنیکوں کو تجویز کیا گیا ہے. مؤخر الذکر کی ایک حالیہ مثال شامل ہے۔مزید پڑھ …
پاؤڈر کوٹنگ کوریج کا حساب کتاب
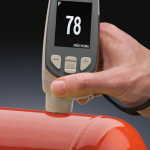
پاؤڈر کوٹنگ کوریج حقیقی منتقلی کی کارکردگی کے عنصر کے لیے بہت اہم ہے جو آپ حاصل کریں گے۔ تخمینہ لگانے والے اکثر اپنے آپ کو درست منتقلی کی کارکردگی کے فیصد میں فیکٹرنگ نہ کرکے مزید پاؤڈر خریدنے کے لیے جھنجھوڑتے ہوئے پاتے ہیں۔ پاؤڈر کوٹنگ کی حقیقی منتقلی کی کارکردگی کا جائزہ لینا بہت ضروری ہے۔ درج ذیل کوریج ٹیبل سطح کے رقبے کی دی گئی مقدار کو کوٹ کرنے کے لیے درکار پاؤڈر کی مقدار کا اندازہ لگانے میں مددگار ہے۔ نظریاتی کوریج کی تشکیل براہ مہربانی نوٹ کریں کہ میں پاؤڈر کوٹنگ کی کوریجمزید پڑھ …
اپنی مصنوعات کے لیے مناسب پاؤڈر کوٹنگ کا انتخاب کیسے کریں۔
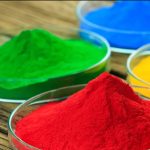
اپنی مصنوعات کے لیے ایک مناسب پاؤڈر کوٹنگ کا انتخاب کیسے کریں رال سسٹم، ہارڈنر، اور روغن کا انتخاب ان خصوصیات کے انتخاب میں صرف آغاز ہے جن کی تکمیل کے لیے کسی کو ضرورت پڑسکتی ہے۔ چمک کا کنٹرول، ہمواری، بہاؤ کی شرح، علاج کی شرح، الٹرا وائلٹ مزاحمت، کیمیائی مزاحمت، حرارت کی مزاحمت، لچک، چپکنے والی، سنکنرن مزاحمت، بیرونی استحکام، دوبارہ دعوی کرنے اور دوبارہ استعمال کرنے کی صلاحیت، کل پہلی بار منتقلی کی کارکردگی، اور بہت کچھ، کچھ ہیں۔ ان عوامل میں سے جن پر غور کیا جانا چاہیے جب کوئی نیا مواد ہو۔مزید پڑھ …
پاؤڈر کوٹنگ کیکنگ کو کیسے روکا جائے۔
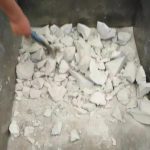
پاؤڈر کوٹنگ کیکنگ کو کیسے روکا جائے مختلف شیشے کی منتقلی کا درجہ حرارت رکھنے والی مختلف رالیں، جیسے ایپوکسی اور پالئیےسٹر رال میں شیشے کی منتقلی کا درجہ حرارت تقریباً 50 ڈگری سینٹی گریڈ ہوتا ہے، لائٹننگ ایجنٹ (701) کا شیشے کی منتقلی کا درجہ حرارت تقریباً 30 ڈگری سینٹی گریڈ ہوتا ہے، مائع لیولنگ مائنس ڈگری سیلسیس میں ایجنٹ۔ پاؤڈر کوٹنگ فارمولیشنز میں کم شیشے کی منتقلی کے درجہ حرارت کے ساتھ مواد کی مقدار جتنی زیادہ ہوگی، شیشے کی منتقلی کا درجہ حرارت اتنا ہی کم ہوگا۔مزید پڑھ …
منسیل کلر چارٹ، منسیل کیٹلاگ
منسیل کلر چارٹ، منسیل کیٹلاگ
عظمت کی منتقلی کا عمل
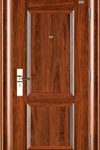
Sublimation کی منتقلی کے عمل کو لاگو کرنے کے لیے، درج ذیل آلات اور مواد کی ضرورت ہے۔ ایک خصوصی منتقلی کا سامان ایک خصوصی سبلیمیشن پاؤڈر کوٹنگ پاؤڈر جو کوٹنگ یونٹ میں اسپرے اور ٹھیک کیا جانا ہے۔ حرارت کی منتقلی کا کاغذ یا فلم (کاغذ یا پلاسٹک کی فلم جس میں مطلوبہ اثر کو خصوصی سربلیمیشن سیاہی کے ساتھ پرنٹ کیا جاتا ہے۔ کام کرنے کا عمل 1. کوٹنگ کا عمل: سبلیمیشن پاؤڈر کوٹنگ کا استعمال، معیاری کوٹنگ یونٹ میں کوٹنگ کا عمل تین مختلف مراحل پر مشتمل ہوتا ہے: پری ٹریٹمنٹ، پاؤڈر چھڑکنا کوٹنگ کی تہہمزید پڑھ …
منسیل کلر سسٹم کی تفصیل
منسل کلر سسٹم کی تفصیل منسل کلر سسٹم پہلی بار امریکی مصور اور آرٹ ٹیچر البرٹ ایچ منسل نے 1900 کے آس پاس قائم کیا تھا، اس لیے اسے "منسل کلر سسٹم" کا نام دیا گیا۔ منسیل کلر سسٹم پانچ بنیادی رنگوں پر مشتمل ہے — سرخ (R)، پیلا (Y)، سبز (G)، نیلا (B)، اور جامنی (P)، علاوہ ازیں پانچ درمیانی رنگ — پیلا سرخ (YR)۔ )، پیلا سبز (YG)، نیلا سبز (BG)، نیلا بنفشی (BP)، اور سرخ بنفشی (RP) بطور حوالہ۔ ہر رنگت کو چار رنگوں میں تقسیم کیا گیا ہے، جس کی نمائندگی نمبر 2.5، 5،مزید پڑھ …
پاؤڈر کوٹنگ کو کیوں اور کیسے ریکوٹ کریں۔
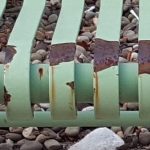
ریکوٹ پاؤڈر کوٹنگ پاؤڈر کی دوسری کوٹ لگانا مسترد شدہ حصوں کی مرمت اور دوبارہ دعوی کرنے کا عام طریقہ ہے۔ تاہم، خرابی کا احتیاط سے تجزیہ کیا جانا چاہئے اور دوبارہ کوٹنگ سے پہلے ذریعہ کو درست کرنا چاہئے. اگر رد کی وجہ من گھڑت خرابی، ناقص کوالٹی سبسٹریٹ، ناقص صفائی یا پری ٹریٹمنٹ کی وجہ سے ہو، یا جب دو پرتوں کی موٹائی برداشت سے باہر ہو جائے تو دوبارہ کوٹ نہ کریں۔ اس کے علاوہ، اگر انڈر کیور کی وجہ سے حصہ رد کر دیا جاتا ہے، تو اسے صرف دوبارہ بنانے کی ضرورت ہے۔مزید پڑھ …
پلاسٹک کی اصطلاحات - انگریزی مخفف اور مکمل انگریزی نام
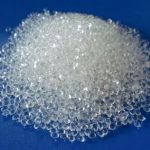
پلاسٹک کی اصطلاحات – انگریزی مخفف اور مکمل انگریزی نام مخفف مکمل نام AAS Acrylonitrile-Bcry ate-styrene opolymer ABS Acrylonitrile-butadiene-styrene ALK Alkyd resin AMMA Acrylonitrile-methylmethacrylate copolymer AMSNitrile-methylmethacrylate copolymer ایکریلونائٹریل ایس اے ایس اے ایس آئی ایس اے ایس آر ایل این ایس اے ایس آئی ایس اے سی -ایکریلیٹ کوپولیمر(اے اے ایس) بی ایم سی بلک مولڈنگ کمپاؤنڈ CA سیلولوز ایسٹیٹ CAB سیلولوز ایسٹیٹ بٹائریٹ CAP سیلولوز ایسیٹیٹ پروپیونیٹ CF کیسین فارملڈیہائڈ رال CFE پولی کلوروٹرفلووروایتھیلین (دیکھیں پی سی ٹی ایف ای) سی ایم کلورینیٹڈ سی پی ای ایل سی پی ایل سی پی ایل سی پی ایل سی پی ایل سی پی ایل سی پی ایل سی ایم سی پولی ایتھلیٹ سی پی ایل سی پی ایل سی پی ایل سی ایم سی پولی ایتھلیٹو propionate(CAP) CPE کلورینیٹڈ پولیتھیلین(PE-C) CPVC کلورینیٹڈ پولی ونائل کلورائد -TPV Elastomer کھوٹ تھرمو پلاسٹک والکنیزیٹEC Ethylene cellulose EEA Ethylene ethylacrylate copolymer EP Epoxide یا epoxy(Cure) EPDM Ethylene propylene diene terpolymer EPS توسیع پذیر پولی اسٹیرین ETFE Ethylene/tetrafluoroethylene EVA Ethylene vinyl accetate copolymerمزید پڑھ …
پاؤڈر کوٹنگ کے دوران سنتری کے چھلکے کو ختم کرنا
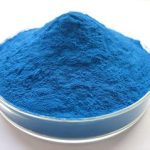
حصے پر الیکٹرو سٹیٹک پاؤڈر پینٹ کی صحیح مقدار کا حصول پائیداری کی وجوہات کے ساتھ ساتھ سنتری کے چھلکے کو ختم کرنے کے لیے بہت اہم ہے۔ اگر آپ اس حصے پر بہت کم پاؤڈر چھڑکتے ہیں، تو زیادہ تر امکان ہے کہ آپ پاؤڈر میں دانے دار بناوٹ کے ساتھ ختم ہوجائیں گے جسے "سنگ سنتری کا چھلکا" بھی کہا جاتا ہے۔ اس کی وجہ یہ ہے کہ اس حصے میں اتنا پاؤڈر نہیں تھا کہ اس کے بہاؤ اور یکساں کوٹنگ بن سکے۔ اس کے غریب جمالیات کے علاوہ، حصہ کرے گامزید پڑھ …
پینٹون پی ایم ایس کلر چارٹ پرنٹنگ اور پاؤڈر کوٹنگ کے لیے استعمال کیا جاتا ہے۔
پینٹون پی ایم ایس کلر چارٹ پینٹون® میچنگ سسٹم کلر چارٹ پی ایم ایس رنگ پرنٹنگ کے لیے استعمال کیا جاتا ہے اپنے رنگ کے انتخاب اور تفصیلات کے عمل میں مدد کے لیے اس گائیڈ کا استعمال کریں۔ یہ چارٹ صرف ایک حوالہ گائیڈ ہے۔ کمپیوٹر اسکرینوں پر پینٹون کے رنگ آپ کے سسٹم میں استعمال ہونے والے گرافکس کارڈ اور مانیٹر کی بنیاد پر مختلف ہو سکتے ہیں۔ صحیح درستگی کے لیے پینٹون کلر پبلیکیشن کا استعمال کریں۔
پاؤڈر کوٹنگ کا عمل کیا ہے؟
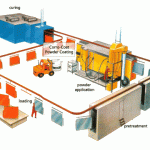
پاؤڈر کوٹنگ کا عمل پری ٹریٹمنٹ – پانی نکالنے کے لیے خشک کرنا – چھڑکاؤ – چیک کرنا – بیکنگ کرنا – چیک کرنا – ختم۔ 1. پاؤڈر کوٹنگ کی خصوصیات پینٹ کی سطح کو توڑنے کے لئے کوٹنگ کی زندگی کو بڑھانے کے لئے مکمل کھیل دے سکتی ہیں پہلے سختی سے سطح سے پہلے کا علاج۔ 2. سپرے، پفنگ کے پاؤڈر کوٹنگ کی کارکردگی کو بڑھانے کے لیے مکمل طور پر گراؤنڈ ہونے کے لیے پینٹ کیا گیا تھا۔ 3. سطح کے بڑے نقائص کو پینٹ کیا جانا ہے، لیپت سکریچ conductive پٹین، تاکہ اس کی تشکیل کو یقینی بنایا جا سکے۔مزید پڑھ …
ناقص مکینیکل خصوصیات اور کیمیائی مزاحمت کا حل
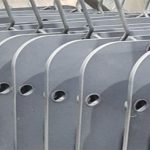
1. ناقص مکینیکل خواص اور کیمیائی مزاحمت کی وجہ: بہت زیادہ یا بہت کم کیورنگ درجہ حرارت یا وقت حل: پاؤڈر کوٹنگ پاؤڈر سپلائر سے تصدیق کریں اور چیک کریں وجہ: تیل، چکنائی، اخراج تیل، سطح پر دھول ناکافی پری ٹریٹمنٹ کی وجہ: ناموافق پری ٹریٹمنٹ اور پاؤڈر کوٹنگ حل: پری ٹریٹمنٹ کا طریقہ ایڈجسٹ کریں، پاؤڈر فراہم کرنے والے سے مشورہ کریں 2. چکنی سطح (سطح پر فلم کی طرح کہرا جس کو صاف کیا جاسکتا ہے) وجہ: پاؤڈر کی سطح پر بلومنگ ایفیکٹ-سفید فلم، جسے صاف کیا جاسکتا ہے۔ :پاؤڈر کوٹنگ فارمولہ تبدیل کریں، علاج کرنے والے درجہ حرارت میں اضافہ کریں وجہ: تندور میں ہوا کی ناکافی گردش حل: ہوا کی گردش میں اضافہ کی وجہ: آلودگی پرمزید پڑھ …
جستی سٹیل کی کنورژن کوٹنگ
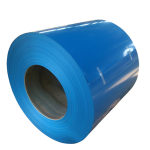
آئرن فاسفیٹس یا کلینر کوٹر کی مصنوعات زنک کی سطحوں پر بہت کم یا ناقابل شناخت کنورژن کوٹنگز تیار کرتی ہیں۔ بہت سے ملٹی میٹل فنشنگ لائنوں میں ترمیم شدہ آئرن فاسفیٹس استعمال ہوتے ہیں جو صفائی پیش کرتے ہیں، اور چپکنے والی خصوصیات فراہم کرنے کے لیے زنک سبسٹریٹس پر مائیکرو کیمیکل اینچ چھوڑ دیتے ہیں۔ بہت سی میونسپلٹیز اور ریاستوں میں اب زنک پی پی ایم کی حدیں ہیں، جس سے میٹل فائنشرز کو کسی ایسے حل کا علاج فراہم کرنے پر مجبور کیا جاتا ہے جس میں زنک کے ذیلی ذخائر پر کارروائی کی جاتی ہے۔ زنک فاسفیٹ کنورژن کوٹنگ، شاید، سب سے اعلیٰ معیار کی کوٹنگ ہے جو کہ جستی سطح پر تیار کی جا سکتی ہے۔ کومزید پڑھ …
کورونا اور ٹرائیبو چارجنگ ٹیکنالوجی
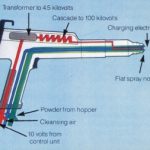
کورونا اور ٹرائیبو چارجنگ کے درمیان فرق کو سمجھنا، یہ فیصلہ کرنے میں مدد کرتا ہے کہ کونسی ٹیکنالوجی ایپلی کیشن کے لیے بہترین ہے۔ ہر قسم کی چارجنگ عام طور پر مخصوص صنعتوں کے لیے استعمال ہوتی رہی ہے۔ ٹریبو چارجنگ عام طور پر ان صنعتوں میں استعمال ہوتی رہی ہے جن میں ایپوکسی پاؤڈر یا ایسی مصنوعات کی ضرورت ہوتی ہے جن کی شکلیں پیچیدہ ہوتی ہیں۔ موصلیت پیدا کرنے والی مصنوعات جیسے برقی آلات جن کے لیے صرف حفاظتی کوٹنگ کی ضرورت ہوتی ہے وہ ٹرائیبو چارجنگ گنز کے بنیادی استعمال کنندہ ہیں۔ یہ حفاظتی کوٹنگ جین ہے۔rally؛ epoxy اپنی سخت تکمیل کی وجہ سے۔ نیز، صنعتیں جیسے تارمزید پڑھ …
درخواست میں پاؤڈر کوٹنگ کی جانچ کے لیے ضروری لیبارٹری کا سامان
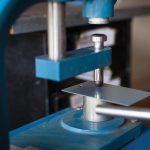
لیبارٹری کے سازوسامان پری ٹریٹمنٹ کیمیکلز کی جانچ کے لیے ضروری سامان، کلی پانی اور حتمی نتائج کے لیے پری ٹریٹمنٹ کیمیکلز کے ٹیسٹ فراہم کنندگان کی ہدایات کے مطابق کیے جانے والے کنڈکٹیویٹی پیمائش گیج فائنل رینس کی جانچ کے لیے ٹمپریچر ریکارڈر کوٹنگ ویٹ کا سامان، DIN 50939 یا مساوی Equipment ایلومینیم پر استعمال کے لیے موزوں پاؤڈر کوٹنگ فلم موٹائی گیج کی جانچ کے لیے ضروری ہے (جیسے ISO 2360, DIN 50984) کراس ہیچ کا سامان، DIN-EN ISO 2409 - 2mm موڑنے والے ٹیسٹ کا سامان، DIN-EN ISO 1519 انڈینٹیشن ٹیسٹ کا سامان، DIN-ENمزید پڑھ …
پاؤڈر کوٹنگ کی درخواست کے عمل کے لیے جانچ کے طریقے
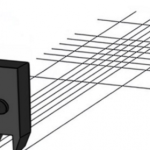
پاؤڈر کوٹنگ کے لیے جانچ کے طریقے ٹیسٹنگ کے طریقے دو مقاصد کے لیے بنائے گئے ہیں: 1. کارکردگی کی وشوسنییتا؛ 2. کوالٹی کنٹرول (1) GLOSS TEST (ASTM D523) ٹیسٹ لیپت فلیٹ پینل گارڈنر 60 ڈگری میٹر کے ساتھ۔ کوٹنگ ہر فراہم کردہ مواد پر ڈیٹا شیٹ کی ضروریات سے + یا – 5% مختلف نہیں ہوگی۔ (2) بینڈنگ ٹیسٹ (ASTM D522) .036 انچ موٹے فاسفیٹڈ اسٹیل پینل پر کوٹنگ 180/1″ مینڈریل پر 4 ڈگری موڑ کو برداشت کرے گی۔ موڑ پر کوئی کریزنگ یا آسنجن اور ختم ہونے کا نقصان نہیں ہے۔مزید پڑھ …
سنکنرن کی درجہ بندی کی تعریفیں
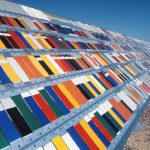
یہ معلوم کرنے میں مدد کے طور پر کہ پری ٹریٹمنٹ کے لیے کیا تقاضے کیے جانے چاہئیں، ہم سنکنرن کی مختلف درجہ بندی کی وضاحت کر سکتے ہیں: سنکنرن کی کلاس 0 گھر کے اندر جس میں نسبتاً نمی 60% سے زیادہ ہے بہت کم سنکنرن کا خطرہ (جارحیت) سنکنرن کلاس 1 غیر گرم، اچھی طرح سے ہوادار گھر کے اندر کمرہ کم سنکنرن کا خطرہ (جارحیت) سنکنرن کلاس 2 گھر کے اندر درجہ حرارت اور نمی کے اتار چڑھاؤ کے ساتھ۔ سمندر اور صنعت سے دور اندرون ملک آب و ہوا میں باہر۔ درمیانی سنکنرن کا خطرہ (جارحیت) سنکنرن کلاس 3 گنجان آباد علاقوں میں یا صنعتی علاقوں کے قریب۔ کھلے پانی کے اوپرمزید پڑھ …
پاؤڈر کوٹنگ اسٹوریج اور ہینڈلنگ
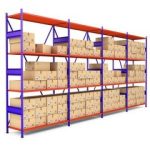
پاؤڈر کوٹنگ اسٹوریج اور ہینڈلنگ پاؤڈر، جیسے کسی کوٹنگ مواد کو پاؤڈر کوٹنگ مینوفیکچرر سے درخواست کے مقام تک اپنے سفر میں بھیجنا، انوینٹوری، اور ہینڈل کرنا ضروری ہے۔ مینوفیکچررز کی تجویز کردہ تاریخوں، طریقہ کار اور احتیاط پر عمل کیا جانا چاہیے۔ اگرچہ مختلف پاؤڈر کی مخصوص ضروریات ہوسکتی ہیں، کچھ آفاقی اصول لاگو ہوتے ہیں۔ یہ ضروری ہے کہ پاؤڈر ہمیشہ ہونا چاہئے: زیادہ گرمی سے محفوظ؛ نمی اور پانی سے محفوظ؛ غیر ملکی مواد، جیسے دیگر پاؤڈر، دھول، گندگی وغیرہ سے آلودگی سے محفوظ۔مزید پڑھ …
پاؤڈر کوٹنگ کا کوالٹی کنٹرول
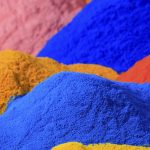
پاؤڈر کوٹنگ کا کوالٹی کنٹرول فنشنگ انڈسٹری میں کوالٹی کنٹرول کو کوٹنگ سے زیادہ توجہ دینے کی ضرورت ہے۔ درحقیقت، مسائل کی اکثریت کوٹنگ کی خرابیوں کے علاوہ دیگر وجوہات کی بناء پر ہوتی ہے۔ معیار کو یقینی بنانے کے لیے جہاں کوٹنگ ایک عنصر ہو سکتی ہے، شماریاتی عمل کنٹرول (SPC) ایک مفید آلہ ہو سکتا ہے۔ SPC SPC میں شماریاتی طریقوں کا استعمال کرتے ہوئے پاؤڈر کوٹنگ کے عمل کی پیمائش کرنا اور مطلوبہ عمل کی سطحوں پر تغیرات کو کم کرنے کے لیے اسے بہتر بنانا شامل ہے۔ SPC عام تغیرات کے درمیان فرق کا تعین کرنے میں بھی مدد کر سکتا ہے۔مزید پڑھ …
پاؤڈر کوٹنگ کے لئے پارٹیکل سائز کی تقسیم کا تجزیہ
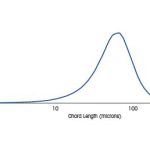
پاؤڈر کوٹنگ لیزر پارٹیکل سائز اینالائزر ٹیسٹ کے نتائج کے لیے پارٹیکل سائز ڈسٹری بیوشن تجزیہ: اوسط ذرہ سائز (درمیانی قطر)، پارٹیکل سائز کی حد اور ڈسپریشن کی پارٹیکل سائز ڈسٹری بیوشن۔ نمونے کا اوسط سائز ذرات کے 50% سے کم اور زیادہ ہے۔ باؤنڈری پارٹیکل سائز: زیادہ سے زیادہ اور کم از کم ذرہ سائز کے عام فہم کے قریب۔ تاہم، نمونے کے ذرہ کے سائز کی اوپری اور نچلی حدوں کو بیان کرنے کے لیے ذرہ کا زیادہ سے زیادہ اور کم از کم سائزمزید پڑھ …
پاؤڈر کوٹنگ کے جلنے والے دھماکے کی کیا وجہ ہے۔
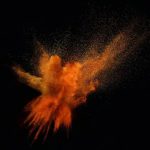
پاؤڈر کوٹنگ کے جلنے والے دھماکے کی وجہ کیا ہے درج ذیل پہلو وہ عوامل ہیں جو پاؤڈر کوٹنگ کے جلنے والے دھماکے کا باعث بنتے ہیں (A) دھول کا ارتکاز نچلی حد سے بڑھ جاتا ہے ان وجوہات کی وجہ سے، پاؤڈر روم یا ورکشاپ میں دھول کا ارتکاز کم سے زیادہ ہو جاتا ہے۔ دھماکے کی حد، اس طرح پاؤڈر جلانے کے دھماکے کے لئے اہم حالات کی تشکیل. اگر اگنیشن کا ذریعہ اعتدال پسند ہے تو، جلنے والے دھماکے ہونے کا امکان ہے (B) پاؤڈر اور پینٹ کی دکان میں مکسنگ کچھ فیکٹریوں میں، وجہمزید پڑھ …
پاؤڈر کوٹنگ کا محفوظ ذخیرہ
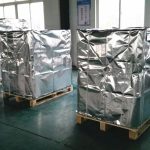
پاؤڈر کوٹنگ کے لیے مناسب ذخیرہ ذرہ جمع ہونے اور رد عمل کی ترقی کو روکتا ہے، اور تسلی بخش اطلاق کو یقینی بناتا ہے، یہ اہم ہے۔ ایپلی کیشن کے دوران پاؤڈر کوٹنگز کو آسانی سے فلوڈیز ایبل، فری فلو، اور اچھے الیکٹرو سٹیٹک چارجز کو قبول کرنے اور برقرار رکھنے کے قابل ہونا چاہیے۔ پاؤڈر کوٹنگز کے ذخیرہ کو متاثر کرنے والے عوامل پاؤڈر کوٹنگز کے ذخیرہ کو متاثر کرنے والے اہم عوامل کی شناخت اس طرح کی جا سکتی ہے: درجہ حرارت نمی / نمی کی آلودگی براہ راست سورج کی روشنی پاؤڈر کوٹنگ کے ذخیرہ کرنے کے لیے تجویز کردہ بہترین حالات یہ ہیں: درجہ حرارت <25°C رشتہ دار نمی 50-65% براہ راست سے دورمزید پڑھ …
الیکٹروسٹیٹک پاؤڈر پینٹنگ کے دوران سنتری کے چھلکے کو کیسے صاف کریں۔
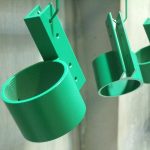
حصے پر الیکٹرو سٹیٹک پاؤڈر پینٹ کی صحیح مقدار کا حصول پائیداری کی وجوہات کے ساتھ ساتھ سنتری کے چھلکے کو ختم کرنے کے لیے بہت اہم ہے۔ اگر آپ اس حصے پر بہت کم پاؤڈر چھڑکتے ہیں، تو زیادہ تر امکان ہے کہ آپ پاؤڈر میں دانے دار بناوٹ کے ساتھ ختم ہوجائیں گے جسے "سنگ سنتری کا چھلکا" بھی کہا جاتا ہے۔ اس کی وجہ یہ ہے کہ اس حصے میں اتنا پاؤڈر نہیں تھا کہ اس کے بہاؤ اور یکساں کوٹنگ بن سکے۔ اس کے غریب جمالیات کے علاوہ، حصہ کرے گامزید پڑھ …
پاؤڈر کوٹنگ پاؤڈر کے معیار کو جاننے کے لیے کچھ نکات
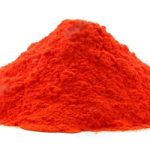
بیرونی ظاہری شکل کی شناخت: 1. ہاتھ کا احساس: ریشمی ہموار، ڈھیلا، تیرتا ہوا محسوس ہونا چاہیے، پاؤڈر جتنا ہموار ڈھیلا، معیار کا اتنا ہی بہتر، اس کے برعکس، پاؤڈر کھردرا اور بھاری، ناقص معیار، آسان چھڑکاؤ، پاؤڈر محسوس نہیں کرنا چاہیے۔ دو بار مزید بربادی. 2. حجم: حجم کا جتنا بڑا، پاؤڈر کوٹنگز کا فلر جتنا کم ہوگا، قیمت جتنی زیادہ ہوگی، کوٹنگ پاؤڈر کا معیار اتنا ہی بہتر ہوگا۔ اس کے برعکس، حجم کا جتنا چھوٹا، کا مواد زیادہمزید پڑھ …
الیکٹروسٹیٹک پینٹنگ کا عمل کیا ہے؟
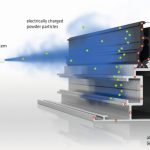
الیکٹرو سٹیٹک پینٹنگ ایک ایسا عمل ہے جس میں سپرے گن کی نوک کو الیکٹرو سٹیٹک طور پر چارج کیا جاتا ہے۔ پینٹ کو بجلی سے چارج کرنا؛ اس طرح پینٹ کو زمینی سطح کی طرف راغب کرنے کی اجازت دیتا ہے۔ یہ عمل عام ہوا کے بہاؤ، ہوا، یا ٹپکنے کے ذریعے تقریباً کوئی پینٹ ضائع نہیں کرتا۔ اس کی وجہ یہ ہے کہ پینٹ کے ذرات دراصل اس سطح کی طرف متوجہ ہوتے ہیں جسے آپ مقناطیس کی طرح پینٹ کر رہے ہیں۔ تاہم، اس عمل کو کام کرنے کے لیے جس چیز کو آپ پینٹ کر رہے ہیں اسے گراؤنڈ کرنا ہوگا۔ الیکٹروسٹیٹک چھڑکاومزید پڑھ …
کوٹنگ چپکنے والی ٹیپ ٹیسٹ کا اندازہ کیسے کریں۔
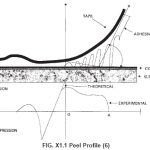
کوٹنگ چپکنے کی جانچ کرنے کے لیے اب تک سب سے زیادہ عام ٹیسٹ ٹیپ اور چھلکا ٹیسٹ ہے، جو 1930 کی دہائی سے استعمال ہو رہا ہے۔ اس کے آسان ترین ورژن میں چپکنے والی ٹیپ کے ایک ٹکڑے کو پینٹ فلم کے خلاف دبایا جاتا ہے اور جب ٹیپ کو ہٹایا جاتا ہے تو فلم ہٹانے کی مزاحمت اور ڈگری کا مشاہدہ کیا جاتا ہے۔ چونکہ قابل تعریف چپکنے والی فلم کو اکثر بالکل نہیں ہٹایا جاتا ہے، اس لیے ٹیسٹ کی شدت کو عام طور پر فلم میں ایک شکل کاٹ کر بڑھایا جاتا ہے۔مزید پڑھ …