پاؤڈر لگانے کے طریقے - الیکٹروسٹیٹک سپرےنگ
کی طرف سے پوسٹ کیا گیا: ڈو پاؤڈر | 29 جنوری 2022 کو
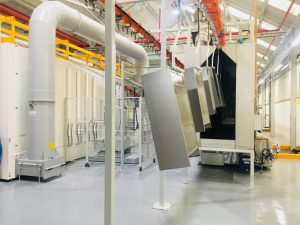
الیکٹروسٹیٹک چھڑکاو لگانے کا سب سے زیادہ استعمال شدہ طریقہ ہے۔ پاؤڈر کوٹنگ مواد. اس کی ترقی متاثر کن شرح سے بڑھ رہی ہے۔ 60 کی دہائی کے وسط میں تیار کیا گیا، یہ عمل کوٹنگز لگانے اور تھوڑے وقت میں ختم کرنے کا سب سے موثر ذریعہ ہے۔ تاہم، جین میں پاؤڈر کوٹنگ کی قبولیتral امریکہ میں شروع میں بہت سست تھا۔ یورپ میں، الیکٹرو سٹیٹک پاؤڈر سپرے کا تصور زیادہ آسانی سے قبول کیا گیا، اور ٹیکنالوجی دنیا کے دیگر حصوں کے مقابلے میں وہاں بہت تیزی سے آگے بڑھی۔ تاہم، مینوفیکچررز کے لیے دستیاب پاؤڈر میٹریل اور ایپلیکیشن آلات دونوں میں بہت سی پیشرفت کی گئی۔ یہ ترقی یافتہ جینralالیکٹرو اسٹاٹک پاؤڈر سپرے کوٹنگ کے ساتھ ساتھ سسٹم کے اجزاء کے فنکشنل آپریشنز کو بہتر بنانے کے ساتھ منسلک مسائل شامل ہیں۔ نتیجے کے طور پر، آج کل الیکٹرو سٹیٹک پاؤڈر سپرے کوٹنگز کے نظام کی ایک وسیع اقسام دستیاب ہیں۔
الیکٹروسٹیٹک پاؤڈر سپرے کے عمل کے ساتھ پاؤڈر کوٹنگ مواد کو لاگو کرنے کے لئے، سامان کے پانچ بنیادی ٹکڑوں کی ضرورت ہے:
- پاؤڈر فیڈر یونٹ؛
- الیکٹروسٹیٹک پاؤڈر سپرے گن، یا مساوی تقسیم کا آلہ؛
- الیکٹروسٹیٹک وولٹیج کا ذریعہ؛
- پاؤڈر ریکوری یونٹ؛
- بوتھ چھڑکیں
ان بنیادی اجزاء کے آپریشن کو بڑھانے کے لیے دیگر آلات موجود ہیں۔ الیکٹرو اسٹیٹک پاؤڈر سپرے سسٹم کے آپریشن میں، پاؤڈر کو فیڈر یونٹ سے پاؤڈر فیڈ ہوز کے ذریعے اسپرے گن (ز) میں ڈالا جاتا ہے۔ سپرے گنز پاؤڈر کو پھیلے ہوئے بادل کی شکل میں حصے کی طرف لے جاتی ہیں۔ پروپیلنگ فورس ہوا کے ذریعے فراہم کی جاتی ہے جو فیڈر یونٹ سے پاؤڈر کو اسپرے گن تک پہنچاتی ہے، اور بندوق پر پاؤڈر کو فراہم کردہ الیکٹرو سٹیٹک چارج کے ذریعے۔ الیکٹرو سٹیٹک وولٹیج سپرے گن کو ایک ایسے ذریعہ کے ذریعے فراہم کیا جاتا ہے جو اسپرے گن سے منسلک الیکٹروڈ کو ہائی وولٹیج، کم ایمپریج الیکٹریکل پاور منتقل کرنے کے لیے ڈیزائن کیا گیا ہے۔ جیسے ہی پھیلا ہوا، الیکٹرو سٹیٹیکل چارجڈ پاؤڈر کلاؤڈ زمینی حصے کے قریب آتا ہے، ایک برقی کشش کا میدان پیدا ہوتا ہے، جو پاؤڈر کے ذرات کو اس حصے کی طرف کھینچتا ہے اور پاؤڈر کی ایک تہہ بناتا ہے۔ اوور سپرے - یا پاؤڈر جو حصہ پر عمل نہیں کرتا ہے - دوبارہ استعمال یا ضائع کرنے کے لئے جمع کیا جاتا ہے۔ کلیکٹر یونٹ میں، پاؤڈر کو پہنچانے والے ہوا کے بہاؤ سے الگ کیا جاتا ہے۔ جمع شدہ پاؤڈر کو پھر خود بخود یا دستی طور پر فیڈر یونٹ میں دوبارہ ری اسپرے کیا جاتا ہے۔ ہوا کو فلٹر میڈیا ڈیوائس کے ذریعے صاف ہوا پلینم میں منتقل کیا جاتا ہے اور پھر حتمی، یا مطلق، صاف ہوا کے طور پر پودوں کے ماحول میں واپس فلٹر کیا جاتا ہے۔ اس کے بعد لیپت والے حصے کو درخواست کے علاقے سے لے جایا جاتا ہے اور اسے گرمی کا نشانہ بنایا جاتا ہے، جس کے نتیجے میں پاؤڈر مواد کا بہاؤ اور علاج ہوتا ہے۔
معاشی فائدہ
الیکٹرو سٹیٹک پاؤڈر سپرے کے ساتھ، پاؤڈر اوور سپرے کا 99% تک بازیافت اور دوبارہ لاگو کیا جا سکتا ہے۔ مائع کوٹنگ سسٹمز کے مقابلے میں پاؤڈر کے ساتھ مواد کا نقصان کم سے کم ہے۔
اس کے علاوہ، زیادہ تر معاملات میں پاؤڈر بغیر کسی رنز کے ایک کوٹ کی کوریج فراہم کرتا ہے اور تیار شدہ حصے پر سیگ کرتا ہے۔ لگانا a پرائمر فنش کوٹ سے پہلے کا کوٹ غیر ضروری ہے، جس سے ملٹی کوٹ مائع نظاموں کے لیے درکار وقت اور محنت کو کم کیا جاتا ہے۔
کیورنگ پاؤڈر میں ایندھن کی لاگت میں کمی اکثر چھوٹے اوون کے استعمال، اوون کے کم اوقات اور بعض صورتوں میں اوون کے کم درجہ حرارت کے نتیجے میں ہوتی ہے۔ بوتھ میک اپ ہوا کو گرم کرنے یا غصہ کرنے کی ضرورت نہیں ہے کیونکہ ہوا پودوں کے ماحول میں صاف ہوا کے طور پر واپس آتی ہے۔
دیگر لاگت کی بچت، بشمول کم صفائی کے اخراجات، پاؤڈر کے ساتھ حاصل کیے جا سکتے ہیں۔ پاؤڈر کے ساتھ کوٹنگ کرتے وقت سالوینٹس کو مکس کرنے، بازیافت کرنے اور ٹھکانے لگانے کی ضرورت نہیں ہے۔ عام طور پر، پاؤڈر لگانے کے آلات یا سپرے بوتھ کی صفائی میں کوئی سالوینٹ یا کیمیکل استعمال نہیں کیا جاتا ہے۔ چونکہ ہوا اور ویکیوم کلینر جین ہیں۔ralپاؤڈر، لیبر اور صفائی ستھرائی کے سامان سے صفائی کے لیے درکار تمام چیزیں کم ہو جاتی ہیں اور خطرناک پینٹ کیچڑ کو ختم کر دیا جاتا ہے۔
مائع کوٹنگز کا ایک بڑا حصہ بعض اوقات زہریلے اور آتش گیر سالوینٹس پر مشتمل ہوتا ہے جو درخواست کے عمل میں ضائع ہو جاتا ہے۔ سالوینٹس کی شپمنٹ اسٹوریج، اور ہینڈلنگ کے اخراجات معمول کے مطابق بہت مہنگے ہیں۔ پاؤڈر کے ساتھ، آلودگی پر قابو پانے کے آلات، فلیش آف ٹائم، اور سالوینٹ فضلہ کو ٹھکانے لگانے کے اخراجات تقریباً ختم ہو جاتے ہیں۔
سالوینٹس کے استعمال کو ختم کرنے سے فائر انشورنس کی ضروریات کے ساتھ ساتھ فائر انشورنس تحفظ کو برقرار رکھنے کے لیے ادا کی جانے والی شرحوں کو بھی کم کیا جا سکتا ہے۔ آخر کار لاگو لاگت فی میل فی مربع فٹ فلم زیادہ تر معاملات میں مائع کوٹنگ کی لاگت کے مساوی یا اس سے کم ہے۔
درخواست میں آسانی
پاؤڈر سپرے ایپلی کیشنز میں محسوس ہونے والی مستقل فنش خصوصیات اور الیکٹرو سٹیٹک "ریپراؤنڈ" انتہائی ہنر مند آپریٹرز کی ضرورت کو کم کرنے میں مدد کرتے ہیں۔ اس کے علاوہ، پاؤڈر کے ساتھ کوٹنگ کرتے وقت viscosity کا توازن برقرار نہیں رہتا۔ پاؤڈر کا مواد مینوفیکچرر سے "اسپرے کے لیے تیار" آتا ہے۔ پاؤڈر کے ساتھ فلیش آف ٹائم کی ضرورت نہیں ہے۔ لیپت والے حصے کو ٹھیک کرنے کے لیے اسپرے والے حصے سے براہ راست تندور میں منتقل کیا جا سکتا ہے۔ مسترد شدہ پرزوں کو دوبارہ کام کرنے میں لاگت کے طور پر رد کرنے کی شرح کو کم کیا جا سکتا ہے۔ عام طور پر پاؤڈر کوٹنگ کے عمل کے ساتھ رن اور سیگس کو ختم کیا جاتا ہے۔
ناکافی یا نامناسب کوٹنگ کو اس حصے سے اڑا دیا جا سکتا ہے (گرمی ٹھیک ہونے سے پہلے) اور دوبارہ کوٹ کیا جا سکتا ہے۔ اس سے اسٹرپنگ، ری ہینڈلنگ، ری کوٹنگ، اور مسترد شدہ پرزوں کو دوبارہ بنانے میں شامل لیبر اور اخراجات کو ختم کیا جا سکتا ہے۔ صارفین کو معلوم ہو رہا ہے کہ پاؤڈر سپرے کوٹنگ کا عمل آسانی سے خودکار ہے۔ یہ خودکار گن موورز، کونٹورنگ میکانزم، روبوٹ، اور سٹیشنری اسپرے گن پوزیشننگ کا استعمال کر سکتا ہے۔ پاؤڈر سپرے کوٹنگ کے ساتھ کل پیداوار کا وقت اکثر کم کیا جا سکتا ہے، یا پیداوار کا حجم بڑھایا جا سکتا ہے۔ مائع کوٹنگ کے عمل کے ساتھ درکار مختلف مراحل کو ختم کرنے کے نتیجے میں زیادہ موثر فنشنگ لائن بن سکتی ہے۔