Powder Coating Materials Today And Tomorrow
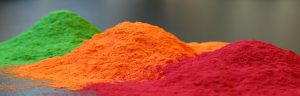
Today, the manufacturers of powder coating materials have solved problems of the past, and ongoing research and technology continue to break down the few remaining barriers to powder coating.
Powder Coating Materials
The most significant material breakthrough has been the development of engineered resin systems designed to meet the diverse and specific needs of the metal finishing industry. Epoxy resins were used almost exclusively during the early years of thermosetting powder coating and are still in broad use today. The use of polyester resins is growing rapidly in the North American market and acrylics are a major factor in many end-users, such as the appliance and automotive industries.
Powders are available with excellent resistance to corrosion, heat, impact, and abrasion. Color selection is virtually unlimited with high and low gloss, and clear finishes available. Texture selections range from smooth surfaces to a wrinkled or matte finish. Film thickness can also be varied to suit the requirements of specific applications.
Development of resin systems resulted in an epoxy-polyester hybrid, which provides thin-layer, low- ~ curing powder coating. Advances in polyester and acrylic resins improved exterior durability of these systems. Specific advances in resin technology include:
- Thin-layer powder coatings based on epoxy-polyester hybrids provide applications in the range of 1 to 1.2 mils for colors with good hiding power. These thin films are currently suitable for indoor applications only. Very thin films, which may require special powder grinds, can be as low as 0.5 mils.
- Low-temperature powder coatings. Powder coatings with high reactivity have been developed to cure at temperatures as low as 250°F (121°C). Such low-curing powders enable higher line speeds, increasing production capacity without sacrificing exterior durability. They also increase the number of substrates that can be powder coated, such as some plastics and wood products.
- Texture powder coatings. These coatings now range from a fine texture with low gloss and a high resistance to abrasion and scratches, to a rough texture useful for hiding the uneven surface of some substrates. These texture coatings have undergone major improvements compared to their counterparts of several years ago.
- Low-gloss powder coatings. It is now possible to reduce gloss values without diminishing the flexibility, mechanical properties, or appearance of powder coatings. Gloss values can be lowered to 1 % or less in pure epoxies. The lowest gloss in weather-resistant polyester systems is about 5%.
- Metallic powder coatings are currently available in an array of colors. Many of these metallic systems are suitable for outdoor application. For excellent exterior durability, a clear powder top coat is often applied over the metallic base. Efforts have been focused on developing perfect matches for standard anodizing colors to meet the needs of the aluminum extrusion market. Another recent development is the replacement of metal flakes with non-ferrous substances like mica.
- Clear powder coatings have undergone significant improvements in the past several years with regard to flow, clarity, and weather resistance. Based on polyester and acrylic resins, these clear powders set quality standards in automotive wheels, plumbing fixtures, furniture, and hardware.
- High weatherability powder coatings. Dramatic advances have been made in developing polyester and acrylic resin systems with excellent long-term weatherability to meet the extended warranties offered by manufacturers. Also under development are fluorocarbon-based powders, which will match or exceed the weatherability of liquid fluorocarbons, with applied costs advantageous to powder
Powder coating has also become a practical finish for products that generate significant heat levels, such as commercial lighting fixtures, and as a primer for grill tops, where it serves as a base for a liquid top coat.
Powder manufacturers continue to perfect resin and curing agent designs. Current research efforts are focused on developing and improving lower-cost, low-curing powders to help expand powder coating application to new substrates. Work continues in developing powders that are more durable with high weatherability for greater use outdoors, exhibiting higher resistance to chalking or fading in sunlight.