AntiCorrosive Pigments
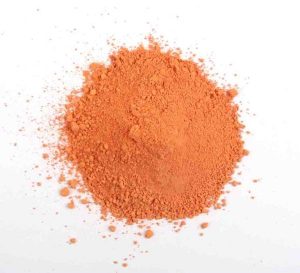
The future trend in anticorrosive pigments is to obtain chromate free and heavy metal free pigments and to go in the direction of sub-micron and nanotechnology anti corrosive pigments and smart coatings with corrosion-sensing. This type of smart coatings do contain microcapsules containing pH indicator or corrosion inhibitor or/and self healing agents. The shell of the microcapsule breaks down under basic pH conditions. The pH indicator changes color and is released from the microcapsule together with corrosion inhibitor and / or self healing agents.
The future is ‘green technology’ and also the different government bodies already give direction in the following directives:
- OSHA PEL proposed 5 µg/m3 for Cr6+ in workplaces Feb 27, 2006.
- OSHA ordered to promulgate new PEL. (aerospace PEL now 20 µg/m3)
- EU Directive 2000/53/EC – End-of-Life Vehicle: Cr6+, Pb, Cd, Hg banned from vehicles marketed after July 1, 2003
- California Air Resources Board (CARB) approved an Airborne Toxic Control Measure (ATCM) for Emissions of Cr6+and Cd from Motor Vehicle and Mobile Equipment Coatings (Automotive Coatings) September 21, 2001.
Anticorrosive pigments which do confirm these regulations are e.g.: Calcium Phosphate; Calcium Borosilicate; Calcium silicagel; Magnesium Phosphate.