Prevention of powder coating orange peel
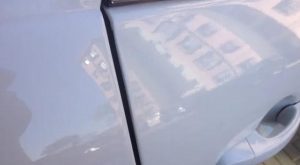
Prevention of powder coating orange peel
The appearance of the coating is becoming increasingly important in the new equipment manufacturing (OEM) Painting. Therefore, one of the main objectives of the coatings industry is to make the final requirements of the user paints to achieve the best performance, which also includes the surface appearance of satisfaction. Affect the visual effects of the surface condition by the factors such as color, gloss, haze, and surface structure. The gloss and image clarity is commonly used to control the appearance of the coating. However that the use of the high gloss coating, the degree of the fluctuation of the surface also affects the appearance of the coating film as a whole, and that the gloss measurement is also impossible to control fluctuation of the visual effects at the same time, this effect is also called the “orange peel”
Orange peel or micro-fluctuations in size between 0.1mm ~ 10mm of the corrugated structure. Wavy, light and dark regions in the high gloss surface of the coating, it can be seen. Can distinguish between two different levels of volatility: long fluctuations, also known as orange peel, which is observed fluctuations in the distance interval of 2 to 3; another called short fluctuations or micro-fluctuations, which is an interval of approximately 50cm at observation fluctuations.
The factors of impacting the flow and appearance during powder coating
In industrial coatings, powder coatings in the change in phase of the preparation and deposition process is unique. Wetting and improve coating flow, resulting in the powder coatings is more difficult to remove than the liquid coating surface defects due to lack of solvent. Although both main parts similar, but compared to the liquid coating, thermosetting powder coatings are based on a very different mechanism
The powder coating is a solvent-free homogeneous system. In the preparation process, a pigment and other components are dispersed by melt-mixing and partially encased in a low molecular weight solid resin. Use of powder coatings is the powder through the air transfer in the end material (powder suspended in the air), and then through the charge so that adhered to the substrate. Heating at a predetermined temperature, so that the powder particles melt together (coalescence), flow (filming), and then leveling, during which, through a viscous liquid phase wetting surface), the final chemical cross-linking forming a high The molecular weight of the coating film, which is the deposition of the powder coating process.
Prevention of powder coating orange peel