کوٹنگ بنانے کا عمل
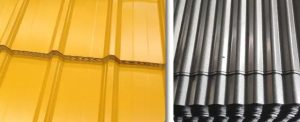
کوٹنگ بنانے کے عمل کو پگھلنے والی کولیسنس میں تقسیم کیا جا سکتا ہے تاکہ کوٹنگ فلم کو تین مراحل میں برابر کیا جا سکے۔
ایک دیئے گئے درجہ حرارت پر، کنٹرول پگھلا ہوا ہم آہنگی کی شرح سب سے اہم عنصر رال کا پگھلنے والا نقطہ ہے، پاؤڈر کے ذرات کی پگھلی ہوئی حالت کی viscosity اور پاؤڈر کے ذرات کا سائز۔ جتنی جلدی ممکن ہو پگھلے ہوئے کی بہترین ہم آہنگی کے لیے، تاکہ لیولنگ مرحلے کے بہاؤ کے اثرات کو مکمل کرنے کے لیے زیادہ وقت مل سکے۔ علاج کرنے والے ایجنٹ کا استعمال وقت کے بہاؤ اور برابر کرنے کے لیے دستیاب ہے، اور اس طرح ان انتہائی فعال پاؤڈر سے بننے والی کوٹنگ فلم اکثر سنتری کے چھلکے کو پیش کرتی ہے۔
کوٹنگ کے بہاؤ اور لیولنگ کو متاثر کرنے والے اہم عوامل رال کی پگھلنے والی چپچپا پن، نظام کی سطح کا تناؤ اور فلم کی موٹائی ہے۔ بدلے میں، پگھلنے والی واسکاسیٹی، خاص طور پر کیورنگ ٹمپریچر، کیورنگ ریٹ اور ہیٹنگ ریٹ پر منحصر ہے۔
اوپر ذکر کردہ مختلف عوامل، ذرہ سائز کی تقسیم اور فلم کی موٹائی کے ساتھ، عام طور پر پینٹ کی جانے والی اشیاء اور پاؤڈر کی تعمیر کے حالات کے مطابق فلم کی مطلوبہ خصوصیات کا تعین کیا جاتا ہے۔ پاؤڈر کوٹنگ نظام کے سطحی تناؤ سے بجلی کے بہاؤ اور برابری کا، اس محاذ کا بھی ذکر کیا گیا ہے۔ اس کے برعکس کوٹنگ فلم میں مالیکیولز کے درمیان کشش پر لاگو ہونے والی قوت، نتیجہ، جیسا کہ پگھلنے والی واسکعثٹی زیادہ ہوتی ہے، بہاؤ اور سطح بندی کے خلاف مزاحمت اتنی ہی زیادہ ہوتی ہے۔ اس طرح، سطح کا تناؤ، اور کشش ثقل کے درمیان فرق کا سالماتی سائز کوٹنگ فلم کی سطح بندی کی حد کا تعین کرتا ہے۔
اچھی بہاؤ کی صلاحیت کے ساتھ کوٹنگ کے لیے، یہ واضح ہے کہ نظام کی سطح کا تناؤ زیادہ سے زیادہ ہونا چاہیے، اور پگھلنے والی واسکاسیٹی ممکنہ حد تک کم ہے۔ یہ نظام کی سطح کی کشیدگی میں additives کا اضافہ کر کے حاصل کیا جا سکتا ہے کو بہتر بنایا جا سکتا ہے اور کم سالماتی وزن کی رال کے کم پگھلنے والے نقطہ کے استعمال سے۔
کوٹنگ بنانے کا عمل
کوٹنگز بہترین بہاؤ کی خصوصیات کے ساتھ مندرجہ بالا حالات کے مطابق تیار کی جا سکتی ہیں، لیکن اس کی اعلی سطح کی کشیدگی کی وجہ سے سکڑنے کا سبب بنتا ہے، کم پگھل viscosity کی وجہ سے sagging پیدا کرے گا، اور کونے غریب coatability. عملی کام میں، نظام کی سطح کی کشیدگی اور پگھلنے والی واسکاسیٹی کو ایک مخصوص رینج کے اندر کنٹرول کیا جاتا ہے، لہذا کوٹنگ کی سطح کی ظاہری شکل حاصل کی جا سکتی ہے۔
کوٹنگ فلم کے بہاؤ کی سطح کے تناؤ اور پگھلنے والی چپچپا پن کا اثر تصویر 2 میں دکھایا گیا ہے۔ جیسا کہ تصویر میں دیکھا جا سکتا ہے، بہت کم یا بہت زیادہ پگھلنے والی چپکنے والی سطح کا تناؤ کوٹنگ کے بہاؤ کو روک دے گا، جس کے نتیجے میں ایک کوٹنگ فلم غریب flowability، اور سطح کشیدگی بہت زیادہ ہے فلم بنانے کے عمل craters نظر آئے گا. پگھلنے کی viscosity کی فزیکل سٹوریج کا استحکام بہت کم ہے پاؤڈر کو خراب کر دے گا کونے کی تعمیر کی ناقص کوٹ ایبلٹی، اور اگواڑے میں تعمیرات جھک جاتی ہیں۔
خلاصہ طور پر، یہ واضح ہے کہ حاصل شدہ پاؤڈر کوٹنگ فلم کی سطح کی آخری حالت، نقائص اور خامیاں (جیسے نارنجی کا چھلکا، ناقص بہاؤ، گڑھے، پن ہول وغیرہ) کا آپس میں گہرا تعلق ہے، اور جمع کرنے کے عمل میں بھی شامل ہیں۔ rheological قوت کنٹرول میں مرحلے کی تبدیلی. پاؤڈر پارٹیکل سائز کی تقسیم کوٹنگ فلم کی سطح کی ظاہری شکل کو بھی متاثر کرتی ہے۔ ذرات جتنے چھوٹے ہوتے ہیں، اس کی تھرمل صلاحیت کی وجہ سے کم کے بڑے ذرات ہوتے ہیں، اس لیے اس کا پگھلنے کا وقت بڑے ذرات کے مقابلے میں کم ہوتا ہے، کولیسنٹ بھی تیزی سے ہوتے ہیں، اور کوٹنگ فلم کی سطح کی بہتر شکل بنتی ہے۔ چھوٹے ذرات کی لمبائی کے مقابلے بڑے پاؤڈر کے ذرات پگھلنے کا وقت، پر بننے والی کوٹنگ فلم سے سنتری کے چھلکے کا اثر پیدا ہو سکتا ہے۔ الیکٹروسٹیٹک پاؤڈر کی تعمیر کے طریقے (کورونا ڈسچارج یا رگڑ ڈسچارج)، بلکہ سنتری کے چھلکے میں ایک عنصر کی تشکیل کا باعث بنتے ہیں۔
نارنجی کے چھلکے کے اثر کو کم کرنے یا اس سے بچنے کا طریقہ بہاؤ اور لیولنگ کو فروغ دینے کے لیے سنتری کے چھلکے کو کم یا بچایا جا سکتا ہے۔ یہ نظام کم پگھلنے والی واسکاسیٹی کا استعمال کرتا ہے، لیولنگ میں توسیع شدہ وقت اور کیورنگ کے عمل میں سطح کے زیادہ تناؤ سے بہاؤ اور لیولنگ کو بہتر بنایا جا سکتا ہے۔ سطح کے تناؤ کے میلان کو کنٹرول کرنے کے اہم پیرامیٹرز میں سنتری کے چھلکے کو کم کیا جاتا ہے، جبکہ کوٹنگ فلم کی سطح کی سطح کے تناؤ کو بھی کنٹرول کرنا یکساں ہوتا ہے، تاکہ سطح کا سب سے چھوٹا رقبہ حاصل کیا جا سکے۔
کوٹنگ کی ظاہری شکل کو بہتر بنانے کے اصل کام میں بہاؤ کو فروغ دینے والا ایجنٹ یا لیولنگ ایجنٹ اکثر استعمال کیا جاتا ہے، تاکہ سطح کے نقائص جیسے کہ سنتری کے چھلکے، گڑھے، پن ہولز کو ختم کیا جا سکے۔ بہاؤ کو فروغ دینے والے ایجنٹ کی اچھی کارکردگی پگھلنے کی چکنائی کو کم کر سکتی ہے، اس طرح پگھلنے کے اختلاط اور روغن کے پھیلاؤ میں حصہ ڈالتا ہے، سبسٹریٹ کی گیلی صلاحیت، بہاؤ اور کوٹنگ کی سطح کو بہتر بنانے کے ساتھ ساتھ سطح کے نقائص کو بھی ختم کرنے میں مدد کرتا ہے۔ ہوا کے اخراج کو آسان بنانے کے لیے۔
بہاؤ موڈیفائر کی خوراک اور اثر کے تعلق کی چھان بین کی جانی چاہیے۔ ناکافی مقدار سکڑنے اور سنتری کے چھلکے کا سبب بنے گی، ضرورت سے زیادہ استعمال سے چمک، کہرا، اور اوپری حصے میں چپکنے کے مسائل پیدا ہوں گے۔ عام طور پر، پری مکس میں فلو موڈیفائر شامل کیا جاتا ہے۔ یا رال ماسٹر بیچ سے بنا ہوا (رال اور 9/1 سے 8/2 کا اضافی تناسب)، یا پاؤڈر کی شکل میں غیر نامیاتی کیریئر پر جذب کیا جاتا ہے۔ پاؤڈر پینٹ میں اضافی اشیاء کی مقدار 0.5 سے 1.5٪ ہے (بائنڈر میں موثر پولیمر کا حساب لگایا جاتا ہے)، لیکن کم ارتکاز میں بھی اچھا ہوسکتا ہے۔
پولی کریلیٹ فلو موڈیفائر ریزنز سب سے زیادہ استعمال ہوتے ہیں، جیسے کہ پولی کریلک ایسڈ بوٹیل ایسٹر ("ایکرونل 4F")، ایکریلک ایسڈ ایتھائل - ایتھائل ہیکسیل ایکریلیٹ کوپولیمر اور بوٹیل ایکریلیٹ - ایکریلک ایسڈ-ہیکسائل ایکریلیٹ کوپولیمر، وغیرہ۔ وہ بہت زیادہ استعمال کیے جا سکتے ہیں۔ وسیع حراستی رینج. عام طور پر سطح کے تناؤ پر پولی کریلیٹ کا بہت کم اثر ہوتا ہے، وہ نسبتاً مستقل یکساں سطح کی تشکیل کوٹنگ میں حصہ ڈال سکتے ہیں۔ سطح کے تناؤ کو کم کرنے والے اضافی اجزاء (جیسے سلیکون یا اس طرح) کے مقابلے میں، وہ سطح کے تناؤ کو کم نہیں کرتے ہیں، اور اس لیے سطح کو تیز کرنے کے لیے استعمال کیا جا سکتا ہے۔ additives کی سطح کے تناؤ کو کم کرنے میں سطح کے فعال ایجنٹ، فلورینیٹڈ الکائل ایسٹرز، اور سلیکون شامل ہیں۔ ان میں شامل ہونے کی رقم بہت حساس ہے۔ Benzoin ایک degassing ایجنٹ ہے، سطح کی کشیدگی کو کم کرنے کا بھی اثر ہے، بڑے پیمانے پر پاؤڈر کوٹنگ کی کوٹنگ فلم کی سطح کی ظاہری شکل کو بہتر بنانے کے لئے استعمال کیا جاتا ہے.
کوٹنگ بنانے کا عمل
تبصرے بند ہیں۔