భాగాల మరమ్మత్తు మరియు పొడి పూతలో హ్యాంగర్ స్ట్రిప్పింగ్
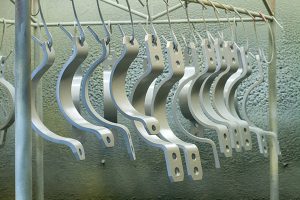
తర్వాత భాగం మరమ్మత్తు యొక్క పద్ధతులు పొడి పూత రెండు వర్గాలుగా ఉంచవచ్చు: టచ్-అప్ మరియు రీకోట్.
పూత పూసిన భాగం యొక్క చిన్న ప్రాంతం కవర్ చేయబడనప్పుడు మరియు ఫినిషింగ్ స్పెసిఫికేషన్లకు అనుగుణంగా లేనప్పుడు టచ్-అప్ రిపేర్ సరైనది. హ్యాంగర్ మార్కులు ఆమోదయోగ్యం కానప్పుడు, టచ్-అప్ అవసరం. అసెంబ్లీ సమయంలో హ్యాండ్లింగ్, మ్యాచింగ్ లేదా వెల్డింగ్ నుండి స్వల్ప నష్టాన్ని సరిచేయడానికి టచ్-అప్ కూడా ఉపయోగించవచ్చు.
పెద్ద ఉపరితల వైశాల్యం కారణంగా ఒక భాగం తిరస్కరించబడినప్పుడు లేదా టచ్-అప్ ఆమోదయోగ్యం కానప్పుడు రీకోట్ అవసరం. ఈ సమయంలో, జాగ్రత్తగా పరిగణించవలసిన అనేక ఎంపికలు ఉన్నాయి. సాధారణంగా తిరస్కరించబడిన భాగాన్ని రెండవ కోటుతో తిరిగి జత చేయవచ్చు. మరొక ఎంపిక భాగాన్ని తొలగించడం మరియు తిరిగి పెయింట్ చేయడం. స్ట్రిప్పింగ్ కూడా మంచి గ్రౌండ్ను అందించడానికి పార్ట్ హ్యాంగర్లను శుభ్రం చేయవచ్చు
ఎలెక్ట్రోస్టాటిక్ స్ప్రే కోసం.
మెరుగులు దిద్దు
లిక్విడ్ టచ్-అప్ పెయింట్ చిన్న బ్రష్, ఏరోసోల్ స్ప్రే లేదా ఎయిర్లెస్ గన్తో వర్తించబడుతుంది. పెయింట్ గాలిలో ఎండబెట్టి ఉంటుంది. ఎండబెట్టడం ప్రక్రియను తక్కువ-ఉష్ణోగ్రత రొట్టెలతో వేగవంతం చేయవచ్చు. కాల్చిన ఓవెన్లో పౌడర్ కోటింగ్ పూర్తిగా నయమైన తర్వాత టచ్-అప్ పెయింట్ ఉపయోగించబడుతుంది. హ్యాంగర్ మార్కులు, మూలలు మరియు అతుకులలో కాంతి మచ్చలు, వెల్డింగ్ లేదా అసెంబ్లీ నుండి నష్టం మరియు ఇతర చిన్న లోపాలు తాకవచ్చు. జన్యువుralలై, ఎ రంగు-సరిపోలిన యాక్రిలిక్ ఎనామెల్ లేదా లక్క ఉపయోగించబడుతుంది. టచ్-అప్ పెయింట్ ఆ భాగం యొక్క ఆశించిన జీవితంలో అవసరమైన పనితీరు నిర్దేశాలను అందుకోకపోతే ఉపయోగించబడదు.
ఫలితంగా ఉత్పత్తి తనిఖీ ప్రమాణాలకు అనుగుణంగా ఉంటే తప్ప, లోపభూయిష్ట ముగింపును రిపేర్ చేయడానికి టచ్-అప్ ఉపయోగించకూడదు.
RECOAT
రెండవ కోటు పొడిని వర్తింపజేయడం అనేది తిరస్కరించబడిన భాగాలను రిపేర్ చేయడానికి మరియు తిరిగి పొందేందుకు సాధారణ విధానం. అయితే, లోపాన్ని జాగ్రత్తగా విశ్లేషించి, తిరిగి పూయడానికి ముందు మూలాన్ని సరిదిద్దాలి. ఫ్యాబ్రికేషన్ లోపం, నాణ్యత లేని సబ్స్ట్రేట్, పేలవమైన క్లీనింగ్ లేదా ప్రీట్రీట్మెంట్ కారణంగా తిరస్కరణ సంభవించినట్లయితే లేదా రెండు పొరల మందం సహనానికి దూరంగా ఉన్నప్పుడు మళ్లీ కోట్ చేయవద్దు. అలాగే, అండర్క్యూర్ కారణంగా భాగం తిరస్కరించబడినట్లయితే, అది కేవలం అవసరమైన షెడ్యూల్లో తిరిగి బేక్ చేయబడాలి.
రెండవ కోటు కాంతి ప్రాంతాలు, ధూళి మరియు కాలుష్యం నుండి ఉపరితల లోపాలు, భారీ ఫిల్మ్ బిల్డ్ లేదా తుపాకీ ఉమ్మివేయడం నుండి కఠినమైన మచ్చలు మరియు తీవ్రమైన ఓవర్బేక్ నుండి రంగు మారడానికి ప్రభావవంతంగా ఉంటుంది. రఫ్ ఉపరితలాలు మరియు ప్రోట్రూషన్లను తిరిగి పూయడానికి ముందు మృదువైన ఇసుకతో వేయాలి.
ఆన్లైన్లో తనిఖీ చేయబడిన భాగాలను రెండవ కోటును స్వీకరించడానికి కన్వేయర్పై ఉంచవచ్చు. ఈ భాగాలు ముడి భాగాలతో ప్రీ-ట్రీట్మెంట్ దశల గుండా వెళతాయి. తిరిగి పూసిన భాగాలు నీటి మచ్చలు లేదా మరకలను చూపిస్తే, చివరి శుభ్రం చేయు దశలో సర్దుబాటు చేయవచ్చు.
రసాయన సరఫరాదారులు సిఫార్సులను అందించగలరు. రీకోట్ కోసం భాగాలు కలిసి వేలాడదీసినప్పుడు, శుభ్రపరచడం మరియు ముందస్తు చికిత్స అవసరం లేదు. అయినప్పటికీ, తిరస్కరించబడిన భాగాలు ఆచరణాత్మక సంఖ్యను కూడగట్టడానికి నిల్వ చేయబడితే, అవి ధూళి మరియు కాలుష్యం కోసం తనిఖీ చేయాలి.
కోట్ మొత్తం భాగం
రెండవ కోటు వేసేటప్పుడు, సాధారణ మిల్ మందం మొత్తం భాగానికి వర్తించాలి. లోపం ఉన్న ప్రాంతాన్ని మాత్రమే పూయడం సాధారణ తప్పు. ఇది ఒక కఠినమైన ఇసుకతో కూడిన ఉపరితలాన్ని వదిలివేస్తుంది, మిగిలిన భాగంలో చాలా సన్నని ఓవర్స్ప్రే పొర మాత్రమే ఉంటుంది. రెండవ కోటు కోసం అదే సిఫార్సు చేయబడిన నివారణ షెడ్యూల్ ఉపయోగించబడుతుంది.
క్రాస్ హాచ్ టెస్ట్ని ఉపయోగించడం ద్వారా ఎంచుకున్న శాంపిల్స్పై రీకోటింగ్ చేసిన తర్వాత ఇంటర్కోట్ సంశ్లేషణను తనిఖీ చేయవచ్చు లేదా మొదటి నుండి రెండవ కోటు సులభంగా పీల్ అవుతుందో లేదో చూడటానికి ఉపరితలంపై గోకడం చేయవచ్చు. రెండవ కోటుకు మంచి యాంకర్ను అందించడానికి కొన్ని పౌడర్ కోటింగ్లను తేలికగా ఇసుక వేయవలసి ఉంటుంది.
REBAKE
మొదటి కోటు సమయంలో ఒక భాగం అండర్క్యూర్ అయినప్పుడు, నిర్దేశిత సమయం మరియు ఉష్ణోగ్రత వద్ద సాధారణ నివారణ షెడ్యూల్ కోసం దానిని బేక్ ఓవెన్కు తిరిగి ఇవ్వడం ద్వారా దాన్ని సరిచేయవచ్చు. నిర్దిష్ట రసాయనికంగా నియంత్రించబడే తక్కువ-నిగనిగలాడే పూతలు వంటి కొన్ని మినహాయింపులతో, భాగాన్ని సరిగ్గా నయం చేసినప్పుడు లక్షణాలు తిరిగి పొందబడతాయి. పాక్షిక నివారణ అధిక గ్లోస్కు దారి తీస్తుంది, ఇది తుది నివారణ సమయంలో అదే స్థాయికి పడిపోదు, అది తగినంత ప్రారంభ నివారణతో పొందబడుతుంది.
స్ట్రిప్పింగ్
తిరస్కరణకు గురైన ఉత్పత్తిని తీసివేయడం వలన ఉత్పత్తి ధరకు విపరీతంగా తోడ్పడుతుంది మరియు ఉత్పత్తి లైన్ ప్రవాహానికి అంతరాయం కలిగిస్తుంది కాబట్టి సాధారణంగా పార్ట్ రిపేర్ కోసం స్ట్రిప్పింగ్ చివరి ప్రత్యామ్నాయం. పేలవమైన ముందస్తు చికిత్స కారణంగా తిరస్కరణకు గురైనప్పుడు లేదా టచ్-అప్ లేదా రెండు కోట్లు ఆమోదయోగ్యం కానప్పుడు, పూతతో కూడిన భాగాలను తీసివేయడం అవసరం అవుతుంది.
మరోవైపు, మంచి ఎలక్ట్రికల్ గ్రౌండ్ కోసం శుభ్రమైన హ్యాంగర్లను అందించడం ద్వారా పౌడర్ కోటింగ్ లైన్ యొక్క ప్రభావంలో స్ట్రిప్పింగ్ ముఖ్యమైన పాత్ర పోషిస్తుంది. హ్యాంగర్లు క్రమానుగతంగా తొలగించబడాలి. స్ట్రిప్పింగ్ పద్ధతులు క్రింది పేరాగ్రాఫ్లలో చర్చించబడ్డాయి. (గమనిక: కెమికల్ స్ట్రిప్పింగ్ ప్రాధాన్య పద్ధతి అని భిన్నాభిప్రాయాలు ఉన్నాయి.)
డిప్ ట్యాంక్లో వేడిగా (పెరిగిన ఉష్ణోగ్రత) లేదా చల్లగా (పరిసరం) ఉపయోగించడానికి రసాయన స్ట్రిప్పర్లు అందుబాటులో ఉన్నాయి. యాసిడ్, ఆల్కలీన్ మరియు కరిగిన ఉప్పు రకాలు ఉన్నాయి, భాగాలు మరియు హాంగర్లు మరియు పూత యొక్క రకాన్ని బట్టి ఎంపిక చేయబడుతుంది.
రసాయన స్ట్రిప్పర్స్ యొక్క ప్రధాన ప్రయోజనం పరికరాల కోసం తక్కువ ప్రారంభ మూలధన పెట్టుబడి. ప్రతికూలతలలో రసాయనాలను నిర్వహించడంలో భద్రతా ప్రమాదాలు, రసాయన భర్తీ మరియు పారవేయడం యొక్క అధిక ఖర్చులు మరియు పెయింట్తో నిండిన రసాయనాలు ఉన్నాయి. అల్యూమినియం మిశ్రమాల వంటి కొన్ని భాగాలు రసాయనాల తుప్పును తట్టుకోలేకపోవచ్చు.
తగలెట్టు
బర్న్ ఆఫ్, లేదా పైరోలిసిస్, స్ట్రిప్పింగ్ కోసం ఓవెన్లు పూతను కాల్చడానికి అధిక ఉష్ణోగ్రతలను ఉపయోగిస్తాయి. అవి దాదాపు 800°F (427″C) వద్ద పనిచేసే బ్యాచ్ రకం లేదా ఆన్లైన్ ఓవెన్లు కావచ్చు, కాలుష్య నియంత్రణ ఎగ్జాస్ట్ సుమారు 1200-1300°F (649-704°C) ఉష్ణోగ్రతల వద్ద పనిచేస్తాయి. బర్న్-ఆఫ్ ఓవెన్లు కాలుష్యం మరియు పారవేయడం సమస్యలను తొలగిస్తాయి. అవి పనిచేయడానికి సాపేక్షంగా సమర్థవంతమైనవి, కానీ పెద్ద మూలధన పెట్టుబడి అవసరం మరియు అవశేష బూడిదను తొలగించడానికి కొన్ని రకాల పోస్ట్ క్లీనింగ్ అవసరం. భాగాలు 800°F (427°C) ఉష్ణోగ్రతలను తట్టుకోవాలి. కొన్ని పూత రసాయనాలు ఈ స్ట్రిప్పింగ్ టెక్నిక్కు తగినవి కావు. పరికరాల తయారీదారుని మరియు స్థానిక నియంత్రణ ఏజెన్సీలను సంప్రదించండి. టూలింగ్ని పదేపదే తొలగించడం వల్ల విచ్ఛిన్నం లేదా వైకల్యం చెందకుండా నిరోధించడానికి కొన్ని రకాల మిశ్రమం అవసరమవుతుందని కూడా గమనించాలి.
షాట్ బ్లాస్టింగ్
షాట్ బ్లాస్టింగ్, లేదా అబ్రాడింగ్, ఇతర పద్ధతులు మినహాయించబడినప్పుడు భాగాలు లేదా హ్యాంగర్లను తీసివేయడానికి ఉపయోగించవచ్చు. క్యూర్డ్ పౌడర్ కోటింగ్ యొక్క దృఢత్వం కారణంగా ఈ ప్రక్రియ చాలా నెమ్మదిగా జరుగుతుంది. ఈ ప్రక్రియ యొక్క ప్రతికూలత ఏమిటంటే, ఇది సాధనాన్ని క్షీణింపజేస్తుంది (సన్నని) మరియు ఎక్కువ ఉపరితల వైశాల్యాన్ని బహిర్గతం చేస్తుంది, ఇది తిరిగి పూయబడినప్పుడు తీసివేయడం కష్టం అవుతుంది.
క్రయోజెనిక్
క్రయోజెనిక్ స్ట్రిప్పింగ్ లిక్విడ్ నైట్రోజన్తో ఫిల్మ్ను పెళుసు చేస్తుంది, ఆపై పూతను సులభంగా తొలగించడానికి నాన్బ్రేసివ్ షాట్ బ్లాస్ట్ను ఉపయోగిస్తుంది. ఇది వేగవంతమైన, కాలుష్యరహిత పద్ధతి, కానీ దీనికి ప్రత్యేక పరికరాలు అవసరం. భాగాలు తప్పనిసరిగా -100°F (-37°C)ని టూలింగ్ కోసం పరిగణించాలి.
జీన్RAL
వివరించిన పద్ధతుల్లో దేనినైనా భాగాలు తట్టుకోగలవా లేదా అనే విషయాన్ని పరిగణనలోకి తీసుకోవాలి. రసాయన మరియు పరికరాల సరఫరాదారులు ఉష్ణోగ్రతలు చేయగలరు మరియు కొన్ని రకాల మిశ్రమం ఆ నిర్ణయంలో సహాయం చేయాల్సి ఉంటుంది. సాధనం విషయానికి వస్తే, సరైన డిజైన్ అవసరమైన శుభ్రపరిచే మొత్తాన్ని తగ్గిస్తుంది. చవకైన భాగం హుక్ తరచుగా భర్తీ చేయబడితే అది చాలా ఖరీదైనదిగా మారుతుంది.
అభాప్రాయాలు ముగిసినవి