Proceso de formación de revestimiento
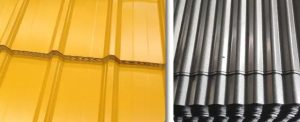
El proceso de formación de recubrimiento se puede dividir en coalescencia por fusión para formar una película de recubrimiento que nivela tres etapas.
A una temperatura dada, el control de la tasa de coalescencia fundida, el factor más importante es el punto de fusión de la resina, la viscosidad del estado fundido de las partículas de polvo y el tamaño de las partículas de polvo. Con el fin de lograr la mejor coalescencia del fundido, lo antes posible, a fin de tener más tiempo para completar los efectos del flujo de la fase de nivelación. El uso de un agente de curado acortado disponible para fluir y nivelar el tiempo requerido, y por lo tanto la película de recubrimiento formada por esos polvos extremadamente activos a menudo presenta piel de naranja.
Los factores clave que afectan el flujo y la nivelación del recubrimiento son la viscosidad de fusión de la resina, la tensión superficial del sistema y el espesor de la película. A su vez, la viscosidad del fundido depende particularmente de la temperatura de curado, la velocidad de curado y la velocidad de calentamiento.
Los diversos factores mencionados anteriormente, junto con la distribución del tamaño de partícula y el espesor de la película, generalmente están determinados por las propiedades requeridas de la película para pintar los objetos y las condiciones de construcción del polvo. El recubrimiento en polvo flujo y nivelación de la potencia a partir de la tensión superficial del sistema, también se ha mencionado este frente. La fuerza aplicada a la atracción entre las moléculas en la película de recubrimiento, por el contrario, el resultado, como que la viscosidad del fundido es mayor, mayor es la resistencia contra el flujo y la nivelación. Por lo tanto, la tensión superficial y el tamaño molecular de la diferencia entre la gravedad determinan el grado de nivelación de la película de recubrimiento.
Para un recubrimiento con buena fluidez, está claro que la tensión superficial del sistema debe ser lo más alta posible y la viscosidad del fundido lo más baja posible. Estos se pueden lograr agregando los aditivos a la tensión superficial del sistema y se puede mejorar el uso de un punto de fusión bajo de la resina de bajo peso molecular.
Proceso de formación de revestimiento
Los recubrimientos se pueden preparar de acuerdo con las condiciones anteriores que tienen excelentes propiedades de flujo, pero debido a su alta tensión superficial provoca la contracción, debido a la menor viscosidad del fundido generará flacidez y las esquinas mala capacidad de recubrimiento. En el trabajo práctico, la tensión superficial y la viscosidad del fundido del sistema se controlan dentro de un rango específico, por lo que se puede obtener una apariencia de superficie de recubrimiento calificada.
El impacto de la tensión superficial y la viscosidad del fundido del flujo de la película de recubrimiento se muestra en la Figura 2. Como se puede ver en la figura, la tensión superficial de una viscosidad del fundido demasiado baja o demasiado alta impedirá el flujo del recubrimiento, lo que resultará en una película de recubrimiento con poca fluidez y la tensión superficial es demasiado alta, el proceso de formación de la película aparecerá como cráteres. La estabilidad de almacenamiento físico de la viscosidad de la masa fundida es demasiado baja hará que el polvo se deteriore La capacidad de recubrimiento deficiente de una construcción de esquina y la construcción en la fachada se combe.
En resumen, está claro que el estado final de la superficie de la película de recubrimiento en polvo obtenida, los defectos y las deficiencias (como piel de naranja, mala fluidez, cráteres, picaduras, etc.) están estrechamente relacionados entre sí, y también en el proceso de deposición involucrado en la cambio de fase en el control de la fuerza reológica. La distribución del tamaño de las partículas de polvo también afecta la apariencia de la superficie de la película de recubrimiento. Cuanto más pequeñas son las partículas, más grandes son las partículas bajas debido a su capacidad térmica, por lo que su tiempo de fusión es más corto que el de las partículas grandes, los coalescentes también son más rápidos y se forma una mejor apariencia superficial de la película de recubrimiento. El tiempo de fusión de las partículas de polvo grandes es mayor que la longitud de las partículas pequeñas, la película de recubrimiento formada puede generar el efecto de piel de naranja. Métodos de construcción de polvo electrostático (descarga corona o descarga por fricción), pero también conduce a la formación de un factor en la piel de naranja.
Cómo reducir o evitar el efecto piel de naranja para promover la fluidez y nivelación puede reducir o evitar la piel de naranja. El sistema utiliza una viscosidad de fusión baja, el tiempo prolongado de nivelación y una tensión superficial más alta en el proceso de curado pueden mejorar el flujo y la nivelación. Los parámetros importantes para controlar el gradiente de tensión superficial son la piel de naranja reducida, mientras que el control de la tensión superficial de la superficie de la película de recubrimiento es uniforme, para obtener el área superficial más pequeña.
En el trabajo real, a menudo se usa un agente que promueve el flujo o un agente de nivelación para mejorar la apariencia del recubrimiento, con el fin de eliminar los defectos de la superficie, como la piel de naranja, los cráteres y los agujeros de alfiler. El buen desempeño de un agente promotor del flujo puede reducir la viscosidad del fundido, contribuyendo así a la mezcla del fundido y la dispersión del pigmento, para mejorar la humectabilidad del sustrato, el flujo y la nivelación del recubrimiento, y también ayuda a eliminar los defectos de la superficie. como para facilitar la salida del aire.
Se debe investigar la dosis del modificador de flujo y la relación del efecto. Una cantidad insuficiente causará encogimiento y piel de naranja, el consumo excesivo conducirá a la pérdida de brillo, turbidez y producirá problemas de adhesión de la capa superior. Por lo general, se agrega el modificador de flujo en la premezcla. O está hecho de un lote maestro de resina (resina y la proporción de aditivos de 9/1 a 8/2), o está adsorbido en el soporte inorgánico en forma de polvo. La cantidad de aditivos en la pintura en polvo es de 0.5 a 1.5% (en aglutinantes de polímero efectivo calculado), pero a bajas concentraciones también puede ser bueno.
Las resinas modificadoras de fluidez de poliacrilato más utilizadas, como el éster butílico del ácido poliacrílico (“Acronal 4F”), el copolímero de ácido acrílico etil-hexilacrilato de etilo y el copolímero de butilacrilato-ácido acrílico-hexilacrilato, etc. amplio rango de concentración. Por lo general, los poliacrilatos tienen poco efecto sobre la tensión superficial, pueden contribuir a que el recubrimiento forme una superficie uniforme relativamente constante. Comparados con los de los aditivos reductores de la tensión superficial (tales como silicona o similares), no reducen la tensión superficial y, por lo tanto, pueden usarse para acelerar la nivelación. Reducir la tensión superficial de los aditivos incluyen agentes tensioactivos, ésteres de alquilo fluorados y silicona. Se unen a la cantidad es muy sensible. El benjuí es un agente desgasificador, también tiene el efecto de reducir la tensión superficial, se usa ampliamente para mejorar la apariencia de la superficie de la película de recubrimiento del recubrimiento en polvo.
Proceso de formación de revestimiento
Los comentarios están cerrados