Konfiguration der Ausrüstung zum Auftragen von Pulverbeschichtungen
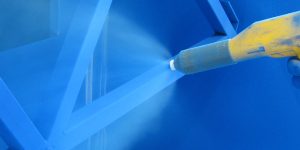
Es gibt viele Möglichkeiten sich zu bewerben Pulverbeschichtung Materialien; und es gibt siebenral Pulverbeschichtungsausrüstung für Option. Allerdings muss das aufzubringende Material verträglicher Art sein. Zum Beispiel, wenn das Auftragungsverfahren Wirbelbett ist. dann muss das Pulverbeschichtungsmaterial eine Fließbettsorte sein. Umgekehrt, wenn das Auftragungsverfahren elektrostatisches Sprühen ist, dann muss das Pulvermaterial eine elektrostatische Sprühsorte sein.
Sobald das Material richtig ausgewählt ist, wird die Auftragungsmethode durch die Teilekonstruktion und die Produktionsziele ausgewählt. Es gibt zwei Formen von Bewerbungsverfahren. Diese variieren so stark wie die Anwendungen, für die sie geeignet sind.
Diese Formulare sind:
- Wirbelschichtanwendung
- Sprühanwendung.
FLÜSSIGKEITSBETT
Diese Auftragsmethode war die erste, mit der Pulverbeschichtungsmaterial aufgetragen wurde. Es wird auch heute noch bei vielen Anwendungen verwendet, bei denen die Dicke des nachgehärteten Films über 5.0 mil liegt. Typische Artikel sind Drahtprodukte, elektrische Stromschienen usw.
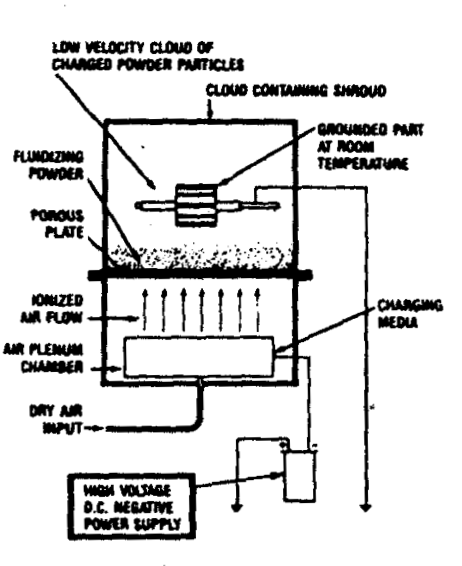
Das Wirbelschicht-Auftragsverfahren kann auf zwei Arten durchgeführt werden. Eine Möglichkeit ist die . Dies ist ein Prozess, bei dem das Teil vorgewärmt werden muss, damit das Pulver schmilzt und daran haftet. Das heiße Teil wird zur Beschichtung in ein Wirbelbett aus Pulver eingebracht. Die Pulvermenge, die auf das Teil aufgetragen wird, hängt davon ab, wie heiß das Teil ist und wie lange es im Bett liegt. Es ist offensichtlich, dass die Kontrolle der Filmdicke nicht von primärer Bedeutung ist, wenn dieses Verfahren verwendet wird.
Um eine bessere Kontrolle der Filmdicke auf dem Teil zu erhalten, werden bei einem Wirbelschichtsystem die Prinzipien der Elektrostatik eingeführt. Wie in Abb. 1 gezeigt, wird das Teil über die Wirbelschicht transportiert und das Pulver wird davon angezogen. Das Teil muss jetzt nicht vorgewärmt werden, bevor es über dem Bett platziert wird. Durch eine elektrostatische Aufladung des Pulverpartikels wird das Pulver vom Bauteil angezogen. Diese elektrostatische Ladung wird in einem elektrostatischen Feld entweder über oder in der Wirbelschicht entwickelt.
Die Filmdicke auf dem Teil wird nun nicht nur durch die Zeitdauer des Teils in der Wirbelschicht gesteuert, sondern auch durch die elektrostatische Aufladung des Pulverpartikels. Bei diesem Prozess wird manchmal immer noch Wärme verwendet, um die Teilekonfiguration zu überwinden, die zu Problemen mit dem Faradayschen Käfig führen kann.
Dieses Auftragsverfahren wird zum Beschichten von Ankern von Elektromotoren verwendet. Diese erfordern eine Beschichtung mit hoher Durchschlagsfestigkeit mit Schichtdickensteuerung, damit der Draht richtig gewickelt werden kann.
Wirbelschichtkonstruktion variiert je nach Hersteller; jedoch werden in allen Ausführungen die gleichen Grundkomponenten verwendet. Diese Komponenten sind der Trichter oder Tank, die Plenum- oder Luftkammer und die Fluidisierungsplatte. Für jede dieser Komponenten werden je nach Design, Hersteller und Endanwendung unterschiedliche Materialien verwendet. Beispielsweise kann die Wirbelplatte aus porösem Polyethylen, Resonanzboden, Kraftpapier oder einem beliebigen porösen Material oder einer Kombination von Materialien bestehen. Der Tank kann aus jedem Material bestehen, das das Gewicht des Pulvers tragen kann.
SPRÜHAUFTRAG
Das Verfahren zum Auftragen von Pulverbeschichtung mit elektrostatischen Spritzgeräten wird in zwei Arten unterteilt. In beiden Fällen muss Elektrostatik verwendet werden, um das Pulver an das Teil zu binden. Es gibt keine mechanische Anziehung oder Haftung zum Halten. Das Pulver zum Teil wie in Flüssigkeitssprühsystemen gesehen. Daher muss das Pulver geladen oder das Teil erhitzt werden (thermische Anziehung), um vom Substrat angezogen zu werden. Die beste Analogie, um dies zu erklären, ist, dass, wenn Sie einen Ballon an Ihrem Haar reiben, dieser aufgrund der elektrostatischen Aufladung an der Wand kleben bleibt. Derselbe Ballon wird ohne elektrostatische Aufladung nicht an der Wand kleben. Dieses Experiment sollte an einem trockenen (nicht feuchten) Tag durchgeführt werden. Die zwei Arten von elektrostatischen Spritzpulverbeschichtungsanlagen sind:
- Corona-geladene Spritzpistolen.
- Tribo-geladene Spritzpistolen

Strombegrenzung, Stromwechsel oder intermittierende Strombeaufschlagung verlängern die erforderliche Beschichtungszeit, da die aufgebrachten Amperesekunden (Coulomb) die galvanische Abscheidung erzeugen.
Der Stromverbrauch reicht von etwa 15 Coulomb pro Gramm fertiger Beschichtung bis zu 150 Coul/g. Nach einem anfänglichen Stromstoß verringert der hohe elektrische Widerstand des frisch abgeschiedenen Films den Stromfluss, was zu einem Überstrom führtrall Bedarf von zwei bis vier Ampere pro Quadratfuß für ein bis drei Minuten oder zwischen einer und drei Kilowattstunden pro 100 Quadratfuß. Die Beschichtungszeit liegt normalerweise im Bereich von einer bis drei Minuten. Für einige spezielle Arbeiten, wie z. B. Drähte. Stahlbänder usw. werden Beschichtungszeiten von nur sechs Sekunden angegeben.
Der Spannungsbedarf wird weitgehend durch die Natur des im Bad dispergierten Harzes bestimmt. Installationen werden normalerweise zwischen 200 und 400 Volt betrieben, obwohl einige Berichten zufolge mit nur 50 Volt und andere mit 1000 Volt betrieben werden.
Spülen:
Frisch beschichtete Teile tragen, wenn sie aus der Badewanne gehoben werden, Badetropfen und sogar Farbpfützen. In der Nähe eines zu beschichtenden Werkstücks liegt eine hohe Konzentration an Lackfeststoffen vor. Es wird geschätzt, dass eine Automobilkarosserie ungefähr 1 Gallone Bad mit sich führen (herausziehen) kann. Bei 10 Gew.-% nichtflüchtigen Stoffen sind dies ungefähr 1 Pfund Feststoffe. Unter Berücksichtigung der Migration von Feststoffen zu zu beschichtenden Oberflächen sind Feststoffkonzentrationen von bis zu 35% in deren Umgebung zu erwarten. Somit ist klar, dass die Rückgewinnung des angehobenen Lackbades notwendig ist und ein lukrativer Weg in Form der „Ultrafiltratspülung“ gefunden wurde.
Die Ultrafiltration verwendet Membranen, die Wasser und wirklich gelöste Stoffe wie Lösungsmittel, Lösungsvermittler, Salze (Verunreinigungen!) usw. passieren lassen. Dispergierte Lackharze, Pigmente usw. werden von der Membran zurückgehalten. Einhundert oder mehr Gallonen Bad passieren unter Druck auf einer Seite der Membran, während eine Gallone klare wässrige Flüssigkeit durch die Membran strömt. Die als Permeat oder Ultrafiltrat bezeichnete Flüssigkeit wird gesammelt und als Spülflüssigkeit verwendet (Abb. 7). Ein dreistufiges Spülsystem gewinnt ca. 85 % der Lackfeststoffe, die aus dem Bad gehoben wurden, zurück.
Manchmal werden Ultrafiltratmengen verworfen, was einen Transport zu Deponien erforderlich machen kann. Das Volumen dieser Abfälle kann durch Umkehrosmose reduziert werden.
Backen oder Aushärten:
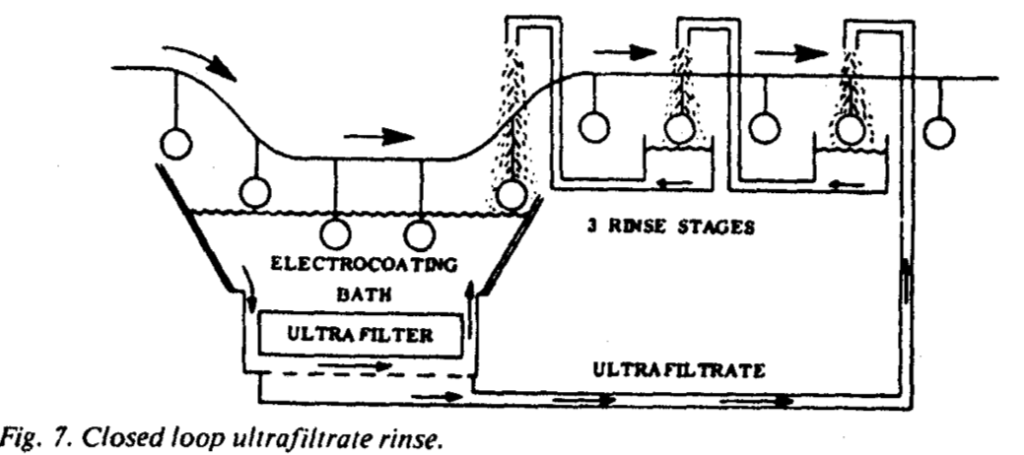
Die Zeit-/Temperaturanforderungen für die Aushärtung werden durch das Harzsystem bestimmt und sind ähnlich denen für herkömmliche Tauch- oder Sprühlacke – normalerweise 5-25 Minuten bei einer Lufttemperatur von 250 °F bis 400 °F. Lufttrocknende Elektrotauchlacke sind auf dem Markt.
AUSRÜSTUNG
Beschichtung von Tanks.
Es werden zwei Arten von Tanks verwendet:
- Als Gegenelektrode dient die Tankwand.
- Die Wannenwand wird mit einer elektrisch isolierenden Schicht ausgekleidet, während die Gegenelektroden in die Wanne eingelegt und dann je nach Werkstückgröße oder -form positioniert werden. Die Elektroden sind bei manchen Installationen von Kompartimenten umgeben, von denen eine Seite von einer Membran gebildet wird. Die Gegenionen „X“ oder „Y“ (Tabelle 1) reichern sich durch einen als Elektrodialyse bezeichneten Prozess in den Elektrodenkammern an und werden verworfen oder wiederverwendet.
Hektik:
Um ein Absetzen der Farbe im Tank zu verhindern, werden Pumpen, Saugrohre, Leitungswellen und Ejektor-Düsen-Systeme eingesetzt, die das gesamte Badvolumen in 6 bis 30 Minuten bewegen oder umdrehen können.
Filterung:
In der Regel werden Filter mit einer Porengröße von 5 bis 75 µm verwendet, um das gesamte Farbvolumen in 30 bis 120 Minuten durch den Filter zu leiten. Die sauren Einsatzstoffe werden mit Farbfeststoffkonzentrationen von 40 % bis 99+ % hergestellt und versandt. In einigen Anlagen wird das Futter in Form von zwei oder mehr Komponenten in den Tank dosiert, wobei eine Komponente das Harz ist, die andere Komponente eine Pigmentaufschlämmung usw.
Methode zur Entfernung des Lösungsvermittlers:
Um ein Bad im Betriebszustand zu halten, wird die Entfernung von übrig gebliebenen Lösungsvermittlern durch Elektrodialyse, Ionenaustausch oder Dialyseverfahren erreicht.
Kühlausrüstung:
Praktisch die gesamte zugeführte elektrische Energie wird in Wärme umgewandelt. Die Kühlausrüstung muss ausreichen, um die gewünschte Badtemperatur aufrechtzuerhalten, normalerweise zwischen 70 °F und 90 °F, wie von den Lacklieferanten angegeben.
Backen oder Aushärten:
Es wird der herkömmliche Ofentyp verwendet. Die Luftgeschwindigkeit durch den Ofen ist aufgrund der sehr geringen Mengen an organischen flüchtigen Bestandteilen in der Lackschicht vergleichsweise gering.
Stromversorgung:
In der Regel werden Gleichrichter spezifiziert, die einen Gleichstrom von weniger als 10 % Welligkeit liefern. Es werden verschiedene Ausgangsspannungssteuerungen verwendet, wie z. B. Stufenschalter, Induktionsregler, sättigbare Kerndrosseln usw. Normalerweise werden Spannungen im Bereich von 50 bis 500 V bereitgestellt. Der Strombedarf errechnet sich aus dem in der zur Verfügung stehenden Zeit aufzutragenden Beschichtungsgewicht.
Kommentarfunktion ist geschlossen