Forschung zur Korrosionsbeständigkeit von feuerverzinkter Galvalume-Beschichtung
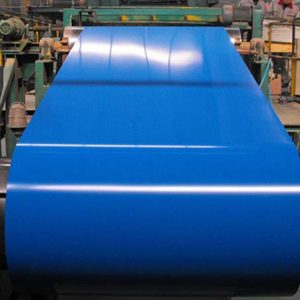
Feuerverzinkte Zn55Al1.6Si-Galvalume-Beschichtungen sind in vielen Bereichen wie der Automobilindustrie, dem Schiffbau, der Maschinenindustrie usw. weit verbreitet, nicht nur aufgrund ihrer besseren Korrosionsschutzleistung als die der Zinkbeschichtung, sondern auch aufgrund ihrer geringen Kosten (die Preis von Al ist derzeit niedriger als der von Zn). Seltene Erden wie La können das Wachstum von Ablagerungen verhindern und die Anhaftung von Ablagerungen erhöhen, daher wurden sie zum Schutz von Stählen und anderem verwendet metallisch Legierungen gegen Oxidation und Korrosion. Es sind jedoch nur wenige Literaturstellen zum Auftragen von La bei der feuerverzinkten Galvalumbeschichtung veröffentlicht, und in dieser Veröffentlichung wurden die Auswirkungen der La-Zugabe auf die Korrosionsbeständigkeit der feuerverzinkten Galvalumbeschichtung untersucht.
Experimentell
[1] HeißtauchenSchmelztauchüberzüge aus einer Zn-Al-Si-La-Legierung, die 0,0.02 Gew.%, 0.05 Gew.%, 0.1 Gew.% und 0.2 Gew.% La enthielten, wurden auf 1 mm Weichstahldraht aufgebracht. Der Prozess war wie folgt: Reinigen zum Entfernen von Rost und Fetten mit Ultraschallwelle (55 °C) → Reinigen mit Wasser → Flussmittel (85 ° C) → Trocknen (100 ~ 200 ° C) Heißtauchen (640 ~ 670 °C, 3~5 s).
[2]GewichtsverlusttestDer Gewichtsverlusttest wurde durch kupferbeschleunigten Essigsäure-Salzsprühtest (CASS) und Tauchkorrosionstests gemessen, die in einer Salzsprühkammer und 3.5%iger NaCl-Lösung durchgeführt wurden. Nach den Tests wurden die korrosiven Produkte mechanisch entfernt, mit fließendem Wasser gespült, dann mit Kaltluft getrocknet und der Gewichtsverlust mit einer elektronischen Waage gemessen. In beiden Fällen drei paralUm genauere Ergebnisse zu erhalten, wurden lel Proben genommen. Die Testzeit betrug 120 h für den CASS-Test und 840 h für den Immersionstest.
[3]Elektrochemischer TestDer elektrochemische Test wurde an der von Deutschland gelieferten elektrochemischen Arbeitsstation IM6e durchgeführt, wobei eine Platinplatte als Gegenelektrode, eine gesättigte Kalomelelektrode als Referenzelektrode und schmelztauchveredelte Zn-Al-Si-La-Beschichtungen aus Weichstahldraht als Arbeitselektrode verwendet wurden. Das korrodierende Medium war 3.5 % NaCl-Lösung. Die der Testlösung ausgesetzte Oberfläche betrug 1 cm². Messungen der elektrochemischen Impedanzspektroskopie (EIS) wurden im Frequenzbereich von 2 kHz bis 10 mHz durchgeführt, die Breite des sinusförmigen Spannungssignals betrug 10 mV (rms). Im Spannungsbereich von -10 mV . wurden schwache Polarisationskurven aufgezeichnet bis 70 mV betrug die Abtastrate 70 mV/s. In beiden Fällen begann das Experiment nicht, bis das Korrosionspotential stabil blieb (eine Variation von weniger als 1 mV in 5 min).
Oberflächenmorphologien der Proben wurden nach den Korrosionstests in der Salzsprühkammer und 550% NaCl-Lösung mit dem SSX-3.5 Rasterelektronenmikroskop (REM) untersucht. Die auf der Oberfläche der Proben im Salzsprühnebel und 3.5 % NaCl-Lösung gebildeten Korrosionsprodukte wurden mittels PW-3040160 Röntgenbeugung (XRD) getestet.
Ergebnisse und Diskussion
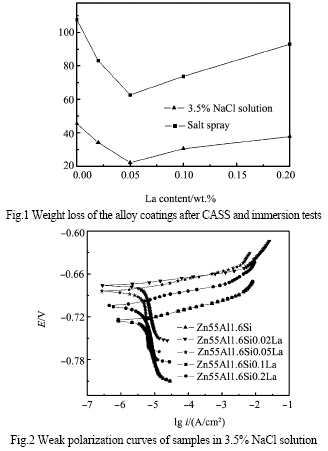
[1.1] Gewichtsverlust
Abb. 1 zeigt die Ergebnisse der Gewichtsverlusttests im Salzsprühschrank und 3.5 % NaCl-Lösung. Die Korrosionsrate der Proben nahm in beiden Fällen zunächst mit steigendem La-Gehalt bis auf 0.05 Gew.-% ab und stieg dann mit weiter steigendem La-Gehalt an. Daher wurde die beste Korrosionsbeständigkeit bei den Beschichtungen erfahren, die 0.05 Gew.-% La enthielten. Es wurde festgestellt, dass während des Eintauchtests Rotrost am frühesten auf der 0 Gew.-% La-Beschichtungsoberfläche in 3.5 % NaCl-Lösung gefunden wurde, jedoch bis zum Ende des Eintauchtests kein Rotrost auf der 0.05 Gew.-% La-Beschichtungsoberfläche vorhanden war .
2.1.2 Elektrochemischer Test
Abb. 2 zeigt schwache Polarisationskurven für Zn-Al-Si-La-Legierungsbeschichtungen in 3.5% NaCl-Lösung. Es ist ersichtlich, dass die Form schwacher Polarisationskurven nur wenige Unterschiede aufwies und der Korrosionsprozess aller Arten von Legierungsbeschichtungen durch kathodische Reaktion kontrolliert wurde. Die Tafel-Anpassungsergebnisse basierend auf den schwachen Polarisationskurven in Abb. 2 sind in Tabelle 1 dargestellt. Ähnlich wie beim Gewichtsverlusttest wurde auch festgestellt, dass die Korrosionsbeständigkeit der Galvalume-Beschichtung durch eine geringe Zugabe von La und das Minimum verbessert werden konnte Die Korrosionsrate wurde mit 0.05 Gew.-% La erhalten.
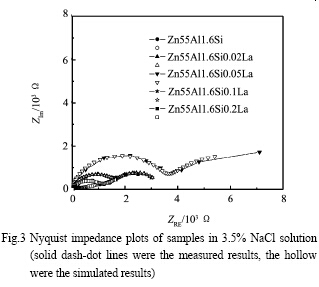
Fig. 3 stellt die Nyquist-Diagramme dar, die für Beschichtungen mit unterschiedlichen Mengen an La-Zugabe aufgezeichnet wurden, die 3.5 h lang einer 0.5%igen NaCl-Lösung ausgesetzt waren. In allen Fällen gab es zwei Bögen, was zwei Zeitkonstanten bedeutete. Diejenige, die bei hoher Frequenz auftrat, repräsentierte die dielektrische Eigenschaft der Legierungsbeschichtung, während die bei niedriger Frequenz der des Weichstahlsubstrats in den Poren entsprach (dh Beschichtungsfehler). Mit zunehmender La-Zugabe nahm der Durchmesser des Hochfrequenzlichtbogens zu, dieser Effekt war im Fall einer Zn55Al1.6Si0.05La-Legierungsbeschichtung ausgeprägter. Bei weiterer Erhöhung des La-Gehalts nahm jedoch der Durchmesser des Hochfrequenzbogens umgekehrt ab. Währenddessen neigte sich das Zentrum aller Bögen zum vierten Quadranten, was darauf hindeutet, dass der Dispersionseffekt auf der Elektrodenoberfläche aufgetreten ist. Unter dieser Bedingung können bessere Ergebnisse erzielt werden, indem CPE (Konstantphasenelement) anstelle der reinen Kapazität verwendet wird, was durch . gezeigt wurde anderen Forschungsgruppen.
Kommentarfunktion ist geschlossen