Qualicoat-Testmethoden und Anforderungen
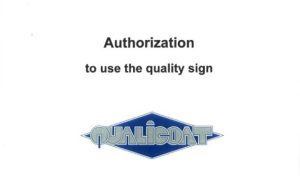
Qualicoat-Testmethoden und Anforderungen
Die nachfolgend beschriebenen Qualicoat-Testmethoden werden verwendet, um fertige Produkte und/oder Beschichtungssysteme für die Zulassung zu testen (siehe Kapitel 4 und 5).
Für die mechanischen Prüfungen (Abschnitte 2.6, 2.7 und 2.8) müssen die Prüfbleche aus der Legierung AA 5005-H24 oder -H14 (AlMg 1 – halbhart) mit einer Dicke von 0.8 oder 1 mm bestehen, sofern nicht anders vom Technischen Prüfer zugelassen Komitee.
An Strangpressprofilen aus AA 6060 oder AA 6063 sollten chemische Prüfungen und Korrosionsprüfungen durchgeführt werden.
1 Das Auftreten
Das Aussehen wird auf der signifikanten Oberfläche bewertet.
Die signifikante Oberfläche muss vom Kunden definiert werden und ist der Teil der Gesamtoberfläche, der für das Aussehen und die Gebrauchstauglichkeit des Artikels wesentlich ist. Kanten, tiefe Vertiefungen und Nebenflächen werden nicht in die signifikante Fläche eingerechnet. Die Beschichtung auf der signifikanten Fläche darf keine Kratzer bis zum Grundwerkstoff aufweisen. Bei Betrachtung der Beschichtung auf der signifikanten Oberfläche in einem schrägen Winkel von ca. 60° zur oberen Oberfläche darf keiner der nachfolgend aufgeführten Fehler aus einer Entfernung von 3 Metern sichtbar sein: übermäßige Rauhigkeit, Läufer, Blasen, Einschlüsse, Krater, Mattheit Flecken, Löcher, Vertiefungen, Kratzer oder andere inakzeptable Fehler.
Die Beschichtung muss von gleichmäßiger Farbe und Glanz mit guter Deckkraft sein. Bei der Besichtigung vor Ort müssen diese Kriterien wie folgt erfüllt sein:
- – für im Außenbereich eingesetzte Teile: Betrachtung aus 5 m Entfernung
- – für im Innenbereich verwendete Teile: Betrachtung aus 3 m Entfernung
2. Glanz
ISO 2813 – bei 60° zur Normalen einfallendem Licht.
Hinweis: Wenn die signifikante Fläche zu klein oder für die Messung des Glanzes mit dem Glanzmessgerät ungeeignet ist, sollte der Glanz visuell mit dem Referenzmuster (aus dem gleichen Betrachtungswinkel) verglichen werden.
ANFORDERUNGEN:
- Kategorie 1: 0 – 30 +/- 5 Einheiten
- Kategorie 2: 31 – 70 +/- 7 Einheiten
- Kategorie 3: 71 – 100 +/- 10 Einheiten
(zulässige Abweichung vom Nennwert des Lacklieferanten)
3. Schichtdicke
EN ISO 2360
Die Dicke der Beschichtung auf jedem zu prüfenden Teil muss auf der signifikanten Oberfläche an mindestens fünf Messbereichen (ca. 1 cm2) mit 3 bis 5 separaten Messungen an jedem Bereich gemessen werden. Der Mittelwert der Einzelmessungen an einer Messstelle ergibt einen in den Prüfberichten festzuhaltenden Messwert. Keiner der gemessenen Werte darf kleiner als 80 % des angegebenen Mindestwertes sein, sonst gilt die Dickenprüfung insgesamt als nicht zufriedenstellend.
Qualicoat-Testmethoden und Anforderungen
Pulver:
- Klasse 11: 60 μm
- Klasse 2: 60 μm
- Klasse 3: 50 μm
- Zweischicht-Pulversystem (Klassen 1 und 2): 110 μm
- Zweischichtiges PVDF-Pulversystem: 80 μm
Flüssige Beschichtung
- Zweischichtiges PVDF-System: 35 μm
- Dreischichtiges metallisiertes PVDF-System: 45 μm
- Silikonpolyester ohne Grundierung : 30 μm (mindestens 20 % Silikonharz)
- Wasserverdünnbare Lacke : 30 μm
- Andere wärmehärtbare Farben: 50 μm
- Zweikomponentenlacke : 50 μm
- Elektrophoresebeschichtung: 25 μm
Andere Beschichtungssysteme können andere Beschichtungsstärken erfordern, dürfen aber nur mit Zustimmung des Exekutivkomitees aufgebracht werden.
Qualicoat-Testmethoden und Anforderungen
Die Ergebnisse sind anhand von vier typischen Beispielen zu beurteilen (Mindestschichtdicke für Beschichtungen von 60 μm):
Beispiel 1:
Messwerte in μm: 82, 68, 75, 93, 86 Durchschnitt: 81
Bewertung: Dieses Muster ist vollkommen zufriedenstellend.
Beispiel 2:
Messwerte in μm: 75, 68, 63, 66, 56 Durchschnitt: 66
Bewertung: Diese Probe ist gut, weil die durchschnittliche Schichtdicke mehr als 60 µm beträgt und weil kein gemessener Wert kleiner als 48 µm ist (80 % von 60 µm).
Beispiel 3:
Messwerte in μm: 57, 60, 59, 62, 53 Durchschnitt: 58
Bewertung: Dieses Muster ist unbefriedigend und fällt in Tabelle 5.1.4 unter die Überschrift „abgelehnte Muster“.
Beispiel 4:
Messwerte in μm: 85, 67, 71, 64, 44 Durchschnitt: 66
Rating:
Diese Probe ist unbefriedigend, obwohl die durchschnittliche Schichtdicke mehr als 60 µm beträgt. Die Prüfung ist als nicht bestanden anzusehen, da der gemessene Wert von 44 μm unterhalb der Toleranzgrenze von 80 % (48 μm) liegt.
4. Adhäsion
EN ISO 2409
Das Klebeband muss der Norm entsprechen. Der Schnittabstand muss bei Schichtdicken bis 1 μm 60 mm, bei Schichtdicken zwischen 2 μm und 60 μm 120 mm und bei dickeren Schichten 3 mm betragen.
ANFORDERUNGEN: Das Ergebnis muss 0 sein.
5. Einrückung
EN ISO 2815
ANFORDERUNGEN:
Mindestens 80 mit der angegebenen erforderlichen Schichtdicke.
6. Schröpftest
Alle Pulversysteme außer Pulver der Klassen 2 und 3: EN ISO 2
Pulver der Klassen 2 und 3:
EN ISO 1520, gefolgt von einem Tape-Pull-Adhäsionstest wie unten angegeben:
Bringen Sie nach der mechanischen Verformung ein Klebeband (siehe Abschnitt 2.4) auf der beschichteten Seite des Prüfblechs an. Decken Sie den Bereich ab, indem Sie fest gegen die Beschichtung drücken, um Hohlräume oder Lufteinschlüsse zu beseitigen. Nach 1 Minute das Klebeband rechtwinklig zur Plattenebene scharf abziehen.
ANFORDERUNGEN:
- – Mindestens 5 mm für Pulverbeschichtungen (Klassen 1, 2 und 3)
- – Mindestens 5 mm für flüssige Beschichtungen außer – Zweikomponentenfarben und -lacke: mindestens 3 mm – wasserverdünnbare Farben und Lacke: mindestens 3 mm
- – Mindestens 5 mm für Elektrotauchlacke
Als Anhaltspunkt muss der Test an einer Beschichtung durchgeführt werden, deren Dicke in etwa der erforderlichen Mindestdicke entspricht.
Mit bloßem Auge betrachtet darf die Beschichtung keine Risse oder Ablösungen aufweisen, außer bei Pulvern der Klassen 2 und 3.
Pulver der Klassen 2 und 3:
Mit bloßem Auge betrachtet darf die Beschichtung nach dem Tape-Pull-Adhäsionstest keine Ablösung zeigen
Qualicoat-Testmethoden und Anforderungen
Kommentarfunktion ist geschlossen