Korrosionsschutz-Epoxid-Pulverbeschichtung spielt eine Schutzfunktion
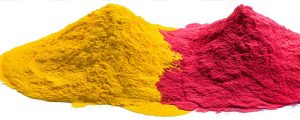
Durch das gemeinsame Aufbringen von kathodischem Schutz und Korrosionsschutzschicht können unterirdische oder unter Wasser befindliche Metallstrukturen den wirtschaftlichsten und effektivsten Schutz erhalten. In der Regel vor dem Gebrauch mit einer Schutzschicht beschichtet, um die elektrische Isolierung der Metall- und Dielektrikumumgebung zu isolieren, kann eine gute Beschichtung mehr als 99% der Strukturen der Außenfläche vor Korrosion schützen. Die Rohrbeschichtung in der Produktion, beim Transport und im Bau kann nicht absolut gegen Schäden garantieren (Mundbeschichtung füllen, Beschichtungsdichte, Beschichtungsloch usw.), es ist nicht möglich, die Korrosionsumgebung der Pipeline vollständig zu isolieren. Aber auch für Anti-Korrosions-Dämmschicht aus verschiedenen Materialien, in unterschiedlichem Maße, saugfähig und atmungsaktiv, und wird nach und nach saugfähig begraben. Um einen wirksamen Korrosionsschutz aufrechtzuerhalten, ist es notwendig, den kathodischen Schutz, dh den Gelenkschutz, zu ergreifen. Dicke Beschichtungen (Dicke> 1 mm), Rohrleitungsverbindungsschutz sollte ein Schutzpotential von -1.10 bis -1.15 V (CSE) gewählt werden, die dünne Beschichtung (Dicke ≤ 1 mm) nimmt das Schutzpotential von -1.05 bis -1.10 V (CSE) auf. Unter Berücksichtigung von Bodenbeschaffenheit, Feuchtigkeit, Temperatur, Beschichtungsarten, Beschichtungsqualität sowie Mikroorganismen geeignete Anpassungen des Schutzpotentials, sowohl um die Rohrleitung zu schützen, ohne die Korrosionsschutzbeschichtung zu zerstören. Die Korrosion der Polarisationsstromauswertungsumgebung ist effektiver. „Schutz“ ist hier ein wichtiges Konzept, das Korrosionsschutz-Epoxid Pulverbeschichtung statt „Schutz“?
Die beschichtete Kathode Ablösung der Beschichtung, zerstörerische Auswirkungen, die eigentliche erdverlegte Stahlrohrleitung zum Ausführen des besten Schutzpotentials ausgewählte kathodische Schutzbeschichtung (3PE-Beschichtung, das darunter liegende schmelzgebundene Epoxidpulver) aus den Gründen, die es wert sind, untersucht zu werden. Über das beste Schutzpotential. Strom-Potenzial-Kurve in der ausländischen Gelehrten Studie Korrosion und kathodischen Schutz Situationen, intensive Wasserstoffdesorption Reaktionspotential von-1.15 V. Laut der Untersuchung von Malaysia, Lloyd's Register, Shell bietet ein maximales Schutzpotential von -1.1 V, Limit Take-1.15 V; Die deutsche Norm DIN30676-19853.1 lautet wie folgt: Bei der dünnen Beschichtung (<1mm) Dicke wurde für den Korrosionsschutz das Gehäuse verwendet, aufgrund der Polarisierung werden sich gegenteilige Auswirkungen wie Blasen bilden, um die Auswirkungen zu minimieren, sollten die Umfang des Schutzpotentials in Abhängigkeit von der Beschichtung, z. B. maximales Schutzpotential von -1.00 ~~-1.20 V (relative CSE) . Im Ausland wird speziell die potenzielle Ursache für das Versagen der Beschichtung durch eine Reihe von Faktoren erwähnt, darunter Bodenzusammensetzung, Feuchtigkeit, Temperatur, Beschichtungsarten, Beschichtungsqualität und mikrobielles Gen der Industrieral-1.05 ~ – 1.10 V (CSE) (Hinweis: die weit verbreitete Verwendung von schmelzgebundenen Epoxid-Pulverbeschichtungen). Kathodische Bleibeschichtung (3PE-Beschichtung der Unterseite des Mechanismus). schmelzgebundene Epoxid-Pulverbeschichtung).
Beschichtungsart, Feuchtigkeit, Temperatur bestimmt die Beschichtung von Wasseraufnahme, Beständigkeit gegen Eindringvermögen in Abhängigkeit von Beschichtungsdicke und Beschichtung unter den gleichen Bedingungen. Untersuchungen haben gezeigt, dass vernetztes Epoxidharz eine gewisse Menge an Poren und Porenkanälen für die Wassermoleküle im Epoxidharz bildet. Lösung erreichen die Beschichtung / Metall-Grenzfläche, vom Tunnel in den Korrosionsproduktfilm, der an der Grenzfläche mit der Metallreaktion erzeugt wird, diese Schicht des Korrosionsproduktfilms, um die Reaktion des Metalls und der Lösung zu verhindern, nimmt der Beschichtungswiderstand allmählich ab. Wenn immer mehr korrosive Ionen die Grenzfläche erreichen, wird diese Schicht des Korrosionsproduktfilms allmählich zerstört, die Korrosion verstärkt und führt schließlich dazu, dass die Epoxidbeschichtung von der Trommel abgezogen wird. Schmelzgebundene Epoxid-Pulverbeschichtungen ausgehärtet sind noch reich an Ether- und Hydroxylgruppen, diese aktiven Gruppen und die Rohroberfläche sind durch chemische Bindungen fest miteinander verbunden, um eine Korrosionsschutzbeschichtung zu bilden. Füllen Sie die Mündung der Beschichtung, dicht, aus nadelstichartigen Gründen, die Beschichtung ist unterschiedlich stark von Wasseraufnahme und Durchlässigkeit, wenn der kathodische Schutz zu groß ist, was zur kathodischen Wasserstoffentwicklung führt, mit den aktiven Wasserstoffatomen der angesammelten, bis zu einem gewissen Grad , Wasserstoff reagiert mit Ether und Hydroxyl, wodurch die Haftfestigkeit der Beschichtung und des Stahlrohrs untergraben wird, was zum Verschwinden der Haftfestigkeit führt. Das Ergebnis ist, dass sich die Beschichtung vom Stahlrohr ablöst.
Kommentarfunktion ist geschlossen