پاؤڈر کوٹنگ ایپلی کیشن کا سامان کی ترتیب
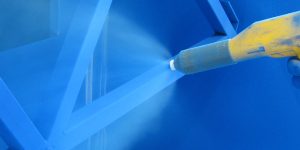
درخواست دینے کے بہت سے طریقے ہیں۔ پاؤڈر کوٹنگ مواد؛ اور سات ہیںral اختیار کے لئے پاؤڈر کوٹنگ کی درخواست کا سامان. تاہم، جس مواد کو لاگو کرنا ہے وہ مطابقت پذیر قسم کا ہونا چاہیے۔ مثال کے طور پر، اگر درخواست کا طریقہ فلوائزڈ بیڈ ہے۔ پھر پاؤڈر کوٹنگ کا مواد فلوائزڈ بیڈ گریڈ ہونا چاہیے، اس کے برعکس، اگر ایپلی کیشن کا طریقہ الیکٹرو اسٹیٹک سپرے ہے، تو پاؤڈر میٹریل الیکٹرو اسٹیٹک سپرے گریڈ ہونا چاہیے۔
ایک بار مواد کو صحیح طریقے سے منتخب کیا جاتا ہے، پھر درخواست کا طریقہ حصہ ڈیزائن اور پیداوار کے اہداف کے ذریعہ منتخب کیا جاتا ہے. درخواست کے طریقوں کی دو شکلیں ہیں۔ یہ ان کے مطابق ایپلی کیشنز کے طور پر وسیع پیمانے پر مختلف ہوتے ہیں.
یہ شکلیں ہیں:
- فلوائزڈ بستر کی درخواست
- سپرے کی درخواست۔
فلوائزڈ بیڈ
درخواست کا یہ طریقہ پہلا طریقہ تھا جو پاؤڈر کوٹنگ میٹریل لگانے کے لیے استعمال ہوتا تھا۔ یہ آج بھی بہت سی ایپلی کیشنز پر استعمال ہوتا ہے جہاں بعد میں ٹھیک ہونے والی فلم کی موٹائی 5.0 میل سے زیادہ ہے۔ عام اشیاء تار کی مصنوعات، الیکٹریکل بس بارز وغیرہ ہیں۔
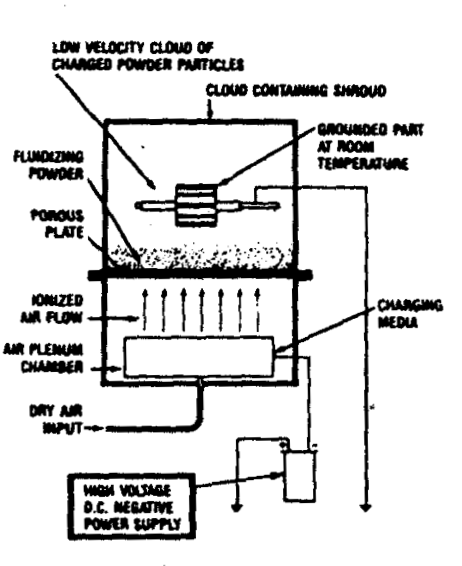
درخواست کے فلوائزڈ بستر کا طریقہ دو طریقوں سے انجام دیا جا سکتا ہے۔ ایک طریقہ یہ ہے۔ یہ ایک ایسا عمل ہے جس کے لیے اس حصے کو پہلے سے گرم کرنے کی ضرورت ہوتی ہے تاکہ پاؤڈر پگھل جائے اور اس پر قائم رہے۔ گرم حصہ کوٹنگ کے لیے پاؤڈر کے فلوائزڈ بیڈ میں رکھا جاتا ہے۔ پاؤڈر کی مقدار جو اس حصے پر لگائی جاتی ہے اس سے یہ معلوم ہوتا ہے کہ حصہ کتنا گرم ہے اور بستر میں کتنا عرصہ ہے۔ یہ واضح ہے کہ جب یہ طریقہ استعمال کیا جاتا ہے تو فلم کی موٹائی کا کنٹرول بنیادی تشویش کا نہیں ہوتا ہے۔
حصے پر فلم کی موٹائی پر زیادہ کنٹرول حاصل کرنے کے لیے، فلوائزڈ بیڈ سسٹم کے ساتھ، الیکٹرو سٹیٹکس کے اصول متعارف کرائے گئے ہیں۔ جیسا کہ تصویر 1 میں دکھایا گیا ہے، اس حصے کو فلوائزڈ بیڈ کے اوپر لے جایا جاتا ہے اور پاؤڈر اس کی طرف متوجہ ہوتا ہے۔ اس حصے کو اب بستر کے اوپر رکھنے سے پہلے پہلے سے گرم کرنے کی ضرورت نہیں ہے۔ پاؤڈر کو پاؤڈر پارٹیکل پر الیکٹرو اسٹاٹک چارج کے ذریعے اس حصے کی طرف راغب کیا جاتا ہے۔ یہ الیکٹرو اسٹاٹک چارج ایک الیکٹرو اسٹیٹک فیلڈ میں یا تو اوپر یا فلوائزڈ بیڈ میں تیار ہوتا ہے۔
اس حصے پر فلم کی موٹائی کو اب نہ صرف یہ کہ حصہ فلوائزڈ بیڈ میں کتنا وقت ہے، بلکہ پاؤڈر پارٹیکل پر کتنا الیکٹرو سٹیٹک چارج ہے۔ اس عمل میں اب بھی بعض اوقات حرارت کو جزوی ترتیب پر قابو پانے کے لیے استعمال کیا جاتا ہے جو فیراڈے کیج کے مسائل کا سبب بن سکتا ہے۔
درخواست کا یہ طریقہ الیکٹریکل موٹر آرمچر کو کوٹنگ کے لیے استعمال کیا جاتا ہے۔ ان کو فلم کی موٹائی کے کنٹرول کے ساتھ ایک اعلی ڈائی الیکٹرک طاقت کی کوٹنگ کی ضرورت ہوتی ہے تاکہ تار کو ٹھیک طرح سے زخم لگ سکے۔
فلوائزڈ بستر کی تعمیر ہر صنعت کار کے ساتھ مختلف ہوتی ہے۔ تاہم، تمام ڈیزائنوں میں ایک ہی بنیادی اجزاء استعمال کیے جاتے ہیں۔ یہ اجزاء ہاپر یا ٹینک، پلینم یا ایئر چیمبر، اور فلوائزنگ پلیٹ ہیں۔ ان اجزاء میں سے ہر ایک کے لیے مختلف مواد استعمال کیے جاتے ہیں جن کا انحصار ڈیزائن، کارخانہ دار اور اختتامی استعمال پر ہوتا ہے۔ مثال کے طور پر، فلوائزنگ پلیٹ غیر محفوظ پولی تھیلین، ساؤنڈ بورڈ، کرافٹ پیپر، یا کسی غیر محفوظ مواد یا مواد کے امتزاج سے بنی ہو سکتی ہے۔ ٹینک کسی بھی ایسے مواد سے بنایا جا سکتا ہے جو پاؤڈر کے وزن کو سہارا دے سکے۔
اسپرے کی درخواست
الیکٹرو اسٹاٹک سپرے آلات کے ساتھ پاؤڈر کوٹنگ لگانے کا طریقہ دو اقسام میں تقسیم کیا گیا ہے۔ دونوں صورتوں میں الیکٹرو سٹیٹکس کا استعمال پاؤڈر کو اس حصے کی طرف راغب کرنے کے لیے کیا جانا چاہیے۔ اس حصے کا پاؤڈر جیسا کہ مائع سپرے سسٹم میں دیکھا جاتا ہے۔ اس لیے، سبسٹریٹ کی طرف متوجہ ہونے کے لیے پاؤڈر کو چارج کیا جانا چاہیے، یا حصے کو گرم کیا جانا چاہیے (تھرمل کشش)۔ اس کی وضاحت کرنے کے لیے بہترین تشبیہ یہ ہے کہ اگر آپ اپنے بالوں پر غبارے کو رگڑتے ہیں، تو یہ الیکٹرو سٹیٹک چارج کی وجہ سے دیوار سے چپک جائے گا۔ ایک ہی غبارہ الیکٹرو سٹیٹک چارج کے بغیر دیوار سے نہیں چپکے گا۔ یہ تجربہ خشک (مرطوب نہیں) دن پر کیا جانا چاہئے۔ دو قسم کے الیکٹروسٹیٹک سپرے پاؤڈر کوٹنگ ایپلی کیشن کا سامان ہیں:
- کورونا چارجڈ سپرے گن۔
- Tribo چارج سپرے گن

ایمپریج کی حد، موجودہ سائیکلنگ یا وقفے وقفے سے موجودہ ایپلیکیشن مطلوبہ کوٹنگ کے وقت کو لمبا کرتی ہے، کیونکہ یہ لاگو ایمپیئر سیکنڈز (کولمب) ہے جو الیکٹرو ڈیپازٹ پیدا کرتا ہے۔
موجودہ کھپت تقریباً 15 کولمب فی گرام تیار شدہ کوٹ سے لے کر 150 کول/گرام تک ہے۔ ابتدائی امپریج میں اضافے کے بعد، تازہ جمع شدہ فلم کی اعلیٰ برقی مزاحمت موجودہ بہاؤ کو کم کر دیتی ہے، جس کے نتیجے میں اوو بنتا ہے۔rall ایک سے تین منٹ کے لیے دو سے چار ایم پی فی مربع فٹ کی ضرورت ہے، یا فی 100 مربع فٹ ایک سے تین کلو واٹ گھنٹے کے درمیان۔ کوٹنگ کا وقت عام طور پر ایک سے تین منٹ تک ہوتا ہے۔ کسی خاص کام کے لیے، جیسے تار۔ اسٹیل بینڈز وغیرہ، کوٹنگ کے اوقات چھ سیکنڈ سے کم بتائے جاتے ہیں۔
وولٹیج کی ضرورت بڑی حد تک غسل میں منتشر رال کی نوعیت سے طے ہوتی ہے۔ تنصیبات عام طور پر 200 اور 400 وولٹ کے درمیان چلائی جاتی ہیں، حالانکہ کچھ مبینہ طور پر 50 وولٹ تک کم اور دیگر 1000 وولٹ تک چلتی ہیں۔
کلی کرنا:
تازہ لیپت شدہ ٹکڑے، جب نہانے سے اٹھائے جائیں، نہانے کی بوندیں اور یہاں تک کہ پینٹ کے گڑھے بھی ساتھ رکھیں۔ کام کے ٹکڑے کے آس پاس پینٹ کے ٹھوس مواد کی زیادہ مقدار موجود ہے جس کو لیپت کیا جا رہا ہے۔ یہ اندازہ لگایا گیا ہے کہ ایک آٹوموٹو باڈی تقریباً 1 گیلن غسل لے کر (گھسیٹ کر) لے سکتی ہے۔ 10wt٪ غیر اتار چڑھاؤ پر یہ تقریبا 1 lb. ٹھوس ہے۔ ان سطحوں کی طرف ٹھوس اشیاء کی منتقلی کو مدنظر رکھتے ہوئے جن کی کوٹنگ کی جا رہی ہے، ان کے آس پاس میں 35% تک ٹھوس مواد کی ارتکاز متوقع ہے۔ اس طرح، یہ واضح ہے کہ اٹھائے گئے پینٹ غسل کی بحالی ضروری ہے، اور ایک منافع بخش طریقہ "الٹرا فلٹریٹ کلی" کی شکل میں پایا گیا ہے۔
الٹرا فلٹریشن جھلیوں کا استعمال کرتی ہے جو پانی کے گزرنے کی اجازت دیتی ہے اور صحیح معنوں میں تحلیل شدہ مادوں، جیسے سالوینٹس، حل کرنے والے، نمکیات (تعفن!) وغیرہ۔ منتشر پینٹ ریزن، روغن وغیرہ کو جھلی کے ذریعے برقرار رکھا جاتا ہے۔ ایک سو یا اس سے زیادہ گیلن غسل دباؤ میں جھلی کے ایک طرف سے گزرتا ہے، جبکہ ایک گیلن صاف پانی جھلی سے گزرتا ہے۔ پرمیٹ یا الٹرا فلٹریٹ کہلانے والے سیال کو جمع کیا جاتا ہے اور اسے کللا سیال کے طور پر استعمال کیا جاتا ہے (تصویر 7)۔ تین مراحل پر مشتمل کللا نظام تقریباً 85% پینٹ سالڈز کو بازیافت کرتا ہے جو غسل سے اٹھائے گئے تھے۔
الٹرا فلٹریٹ کی مقدار کو بعض اوقات ضائع کر دیا جاتا ہے، جس کی وجہ سے ڈمپ سائٹس پر ٹرک چلانے کی ضرورت پڑ سکتی ہے۔ ان کچرے کے حجم کو ریورس اوسموسس کے ذریعے کم کیا جا سکتا ہے۔
پکانا یا علاج:
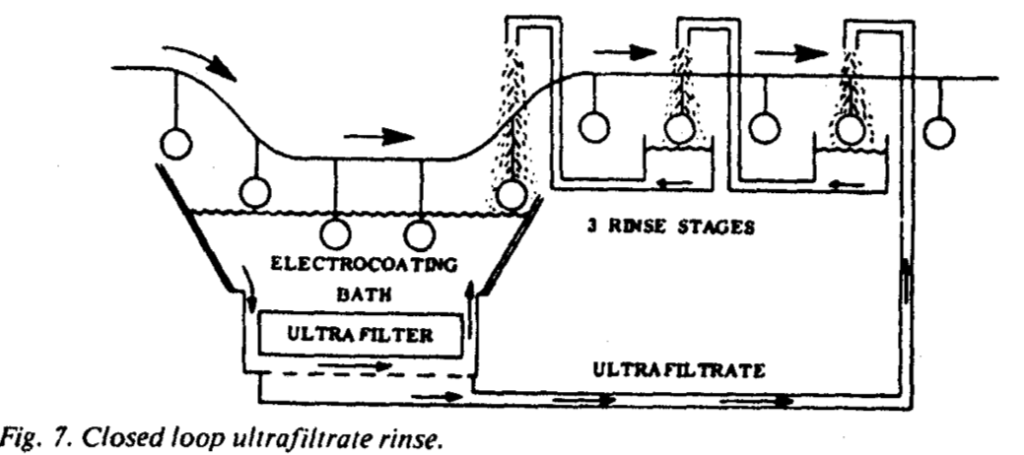
علاج کے لیے وقت/درجہ حرارت کے تقاضے رال سسٹم کے ذریعے طے کیے جاتے ہیں اور روایتی ڈپ یا سپرے پینٹ کے لیے درکار ہوتے ہیں - عام طور پر 5'F سے 25°F ہوا کے درجہ حرارت پر 250-400 منٹ۔ ایئر ڈرائینگ الیکٹرو کوٹس مارکیٹ میں موجود ہیں۔
EQUIPMENT
کوٹنگ ٹینک.
دو قسم کے ٹینک استعمال کیے جاتے ہیں:
- ٹینک کی دیوار کاؤنٹر الیکٹروڈ کے طور پر استعمال ہوتی ہے۔
- ٹینک کی دیوار کو برقی طور پر موصل کوٹ کے ساتھ لائن کیا جاتا ہے، جبکہ کاؤنٹر الیکٹروڈز کو ٹینک میں داخل کیا جاتا ہے اور پھر کام کے ٹکڑے کے سائز یا شکل کے مطابق رکھا جاتا ہے۔ الیکٹروڈ کچھ تنصیبات میں ہوتے ہیں جن کے چاروں طرف کمپارٹمنٹ ہوتے ہیں، جن کا ایک رخ ایک جھلی سے بنتا ہے۔ کاؤنٹر آئن "X" یا "Y" (ٹیبل 1) الیکٹروڈ کمپارٹمنٹس میں ایک عمل کے ذریعے جمع ہوتے ہیں جسے الیکٹرو ڈائلیسس کہتے ہیں، اور انہیں ضائع یا دوبارہ استعمال کیا جاتا ہے۔
جارحیت:
پینٹ کو ٹینک میں جمنے سے روکنے کے لیے پمپ، ڈرافٹ ٹیوب، لائن شافٹ اور ایجیکٹر نوزل سسٹمز استعمال کیے جاتے ہیں جو غسل کے پورے حجم کو 6 سے 30 منٹ میں منتقل کرنے یا تبدیل کرنے کی صلاحیت رکھتے ہیں۔
فلٹریشن:
ایک اصول کے طور پر، 5 سے 75 مائکرون پور سائز فلٹرز کا استعمال 30 سے 120 منٹ میں فلٹر کے ذریعے پورے پینٹ والیوم کو منتقل کرنے کے لیے کیا جاتا ہے۔ تیزابی فیڈ مواد 40% سے لے کر 99+% تک پینٹ ٹھوس مقدار میں تیار اور بھیجے جاتے ہیں۔ کچھ تنصیبات میں، فیڈ کو دو یا دو سے زیادہ اجزاء کی شکل میں ٹینک میں میٹر کیا جاتا ہے، ایک جزو رال، دوسرا جزو روغن سلری، وغیرہ۔
حل کرنے والے کو ہٹانے کا طریقہ:
غسل کو آپریٹنگ حالت میں رکھنے کے لیے، بچ جانے والے محلول کو ہٹانے کا عمل الیکٹرو ڈائلیسس، آئن ایکسچینج، یا ڈائیلاسز کے طریقوں سے کیا جاتا ہے۔
کولنگ کا سامان:
عملی طور پر تمام لاگو برقی توانائی حرارت میں بدل جاتی ہے۔ ٹھنڈک کا سامان مطلوبہ غسل کے درجہ حرارت کو برقرار رکھنے کے لیے کافی ہونا چاہیے، عام طور پر 70°F اور 90F کے درمیان، جیسا کہ پینٹ سپلائرز کے ذریعہ بیان کیا گیا ہے۔
پکانا یا علاج:
روایتی قسم کا تندور استعمال کیا جاتا ہے۔ پینٹ کوٹ میں بہت کم مقدار میں نامیاتی اتار چڑھاؤ کی وجہ سے تندور کے ذریعے ہوا کی رفتار نسبتاً کم ہے۔
طاقت کا منبع:
ریکٹیفائر جو 10% سے کم ریپل فیکٹر کا براہ راست کرنٹ فراہم کرتے ہیں عام طور پر بیان کیے جاتے ہیں۔ مختلف آؤٹ پٹ وولٹیج کنٹرولز استعمال میں ہیں، جیسے کہ نل کے سوئچ، انڈکشن ریگولیٹرز، سیچو ایبل کور ری ایکٹر وغیرہ۔ 50 سے 500V رینج میں وولٹیج عام طور پر فراہم کیے جاتے ہیں۔ موجودہ ضرورت کا حساب دستیاب وقت میں لاگو ہونے والی کوٹنگ کے وزن سے لگایا جاتا ہے۔
تبصرے بند ہیں۔