Bereiding van Carboxyl-getermineerd voor Fusion-bonded-epoxy Powder Coating
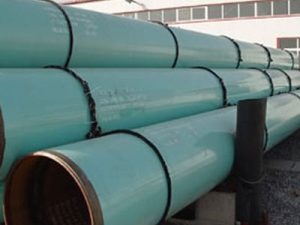
Bereiding en karakterisering van carboxy-getermineerde poly (butadieen-co-acrylonitril)-epoxyhars prepolymeren voor Fusion-bonded-epoxy Poeder Coating
1 Inleiding
Fusiegebonden epoxy (FBE) poedercoatings die voor het eerst werden ontwikkeld door 3M Co., worden veel gebruikt wanneer langdurige bescherming tegen corrosie van cruciaal belang is, zoals in de olie-, metaal-, gas- en waterleidingindustrie. De prestatie-eisen voor FBE-poedercoatings zijn echter uitdagend vanwege hun hoge verknopingsdichtheid. De inherente brosheid van uitgeharde coatings is een van de belangrijkste obstakels die een bredere toepassing van epoxy's in industrieën in de weg staan. Daarom is het misschien mogelijk om de prestaties van FBE-coatings te verbeteren door de taaiheid van de coating te vergroten. Er zijn veel hardingsmethoden gebruikt voor het harden van epoxysystemen, vaak in composiettoepassingen, waaronder rubber, elastomeer, thermoplastisch, copolymeer, met nanodeeltjes gemodificeerde epoxy's en combinaties van het bovenstaande.
Hoewel er veel onderzoek is gedaan naar het harden van epoxysystemen, is het merendeel van de
studies betroffen de chemische modificatie van epoxyhars met reactief vloeibaar rubber, met name carboxyl-getermineerd butadieen-co-acrylonitril (CTBN). McGarry et al. gebruikten CTBN met een molecuulgewicht van 3000 en verschillende DGEBA-epoxies die met piperidine waren uitgehard. Kinloch et al. onthulden een dynamische afhankelijkheid in het DGEBA/CTBN/piperidine-systeem door de breuktaaiheid bij verschillende slagsnelheden te berekenen en een bijna tweevoudige toename in taaiheid te verkrijgen. CTBN zou kunnen worden geïntroduceerd in de epoxysystemen zoals diglycidylether van bisfenol-A (DGEBA) epoxyharsen. Wanneer dergelijke epoxyharsen samen met het vloeibare rubber worden uitgehard, kan de taaiheid van de domeinen worden verbeterd door de slagenergie te absorberen. Het is algemeen bekend dat de uitgeharde harsen tweefasensystemen [26] omvatten waarin het vloeibare rubber is gedispergeerd in een matrix van epoxy met een bolvormige domeinstructuur of een continue structuur.
Tot dusver was het harden van epoxyharsen voornamelijk gericht op de vloeibare epoxyharsen, en weinig onderzoek was gericht op het harden van vaste epoxyharsen. In dit artikel hebben we CTBN-EP-prepolymeren bereid zonder gebruik te maken van organische oplosmiddelen. Vervolgens werden FBE poedercoatings composieten gevuld met CTBN-EP prepolymeren geproduceerd. Op basis van de mechanische eigenschappen en morfologische analyse werden pogingen ondernomen om taaiheidsmechanismen te analyseren die heersen in de fasegescheiden matrix. Analyse van de structuureigenschapsrelatie van het CTBN-EP-systeem is naar ons beste weten een nieuwe onderneming. Deze nieuwe hardingstechnologie kan dus de toepassingsgebieden van FBE-poedercoatings in de industrie uitbreiden.
2. experimenteel
2.1-materialen
De gebruikte epoxyhars was vaste diglycidylether van bisfenol A (DGEBA) (DOW, DER663) met een epoxide-equivalentgewicht van 750-900. Vloeibaar, carboxyl-getermineerd poly(butadieen-co-acrylonitril) (CTBN) (Emerald, Hypro 1 300x1323) met een acrylonitrilgehalte van 26% werd gebruikt. Trifenylfosfine werd in dit systeem als katalysator gebruikt. De verharder (HTP-305) was een fenol. Fenol epoxyhars (GT7255) werd gekocht bij HUNTSMAN Co., Pigment (L6900), dat werd geleverd door BASF Co., ontgassingsmiddel en egaliseermiddel werden gekocht bij Aisitelun.
2.2 Synthese en karakterisering van CTBNEP-prepolymeren
Stoichiometrische hoeveelheden epoxyharsen, CTBN en katalysator werden in een kolf gedaan die gedurende 150 uur werd verwarmd en mechanisch geroerd bij 3.0 . De reactie werd gestopt toen de zuurwaarde daalde tot 0. De prepolymeren werden gemarkeerd als CO, C0, C5, C10 en C15 (subscripts zijn de inhoud van de CTBN). De mogelijke reactie wordt getoond in Fig.20.
FTIR-spectroscopie werd gebruikt om de structuren te karakteriseren. FTIR-spectra werden geregistreerd door een FTLA2000-104 spectrofotometer in het golflengtebereik van 4 500-500 cm−1 (ABB Bomem of Canada). De molecuulgewichten en molecuulgewichtsverdeling van CTBN-EP-prepolymeren werden bepaald met GPC. Tetrahydrofuran (THF) werd gebruikt als loopmiddel met een stroomsnelheid van 1.0 ml/min. Het kolomsysteem werd gekalibreerd met gebruikmaking van monogedispergeerde standaardpolystyrenen.
2.3 Bereiding en karakterisering van uithardingsfilms
Er werden vijf uithardingsfilms bereid die 0 gew.%-20 gew.% CTBN bevatten. De berekende hoeveelheden DGEBA (volgens de formulering gegeven in Tabel 1) en HTP-305 werden gedurende 120 minuten bij 10 geroerd om een homogeen mengsel te verkrijgen. Het mengsel werd in een voorverwarmde ijzeren mal gegoten die gedurende 180 minuten in een heteluchtoven bij 10 was uitgehard en vervolgens gedurende 30 minuten bij 200 werd uitgehard.
De trekproeven werden uitgevoerd op een KD111-5 machine (KaiQiang Co., Ltd., China) met een kruiskopsnelheid van 1 mm/min. De waarden zijn genomen uit gemiddeld drie monsters volgens GB/2568-81. De rek bij het breekpunt van het monster werd geëvalueerd. De slagvastheid van het monster werd bepaald op een MZ-2056-machine met behulp van rechthoekige monsters van 40 mm × 10 mm × 2 mm. De tests werden uitgevoerd bij kamertemperatuur en waarden werden genomen uit gemiddeld drie monsters volgens GB/T2571-1995.
De glasovergangstemperaturen van de uithardingsfilms werden bepaald met behulp van een dynamische mechanische analysator (DMA). De metingen werden uitgevoerd met een verwarmingssnelheid van 2 /min van -90 ℃ tot 180 ℃ bij een vast frequentieniveau van 1 Hz. De opslagmodulus, verliesmodulus en verliesfactor werden verkregen met behulp van dubbele cantilever-modus met een monster van 30 mm × 10 mm × 2 mm.
Scanning elektronenmicroscopie (SEM) werd uitgevoerd (Quanta-2000 model SEM, FEI of Dutch) met een elektronenvoltage van 10 kV. De monsters werden gebroken onder vloeibare stikstof en eerst behandeld met tolueen om de rubberfase te extraheren voordat ze onder vacuüm werden gedroogd. De grootte en verdeling van gedispergeerde deeltjes werden bepaald door middel van het maken van een halfautomatische opname.
Het percentage gewichtsverlies en thermische degradatiekenmerken van bereide monsters werden geëvalueerd door een thermogravimetrische analysator (TGA) geregistreerd op Instrument (METTER Toledo uit Zwitserland). De hoeveelheid genomen monster was ongeveer 5-10 mg in een platinamonsterpan. De verwarmingssnelheid in elke run werd op 10 /min gehouden en het temperatuurbereik was omgevingstemperatuur tot 800 .
Reacties zijn gesloten