कोटिंग तयार करण्याची प्रक्रिया
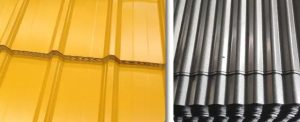
कोटिंग-फॉर्मिंग प्रक्रियेला वितळलेल्या कोलेसेन्समध्ये विभागले जाऊ शकते जेणेकरून कोटिंग फिल्म तीन टप्प्यात समतल होईल.
दिलेल्या तपमानावर, नियंत्रण वितळलेले एकत्रीकरण दर सर्वात महत्वाचा घटक म्हणजे राळचा वितळण्याचा बिंदू, पावडर कणांच्या वितळलेल्या स्थितीची चिकटपणा आणि पावडर कणांचा आकार. शक्य तितक्या लवकर वितळलेल्या सर्वोत्कृष्ट एकत्रीकरणासाठी, लेव्हलिंग फेज फ्लो इफेक्ट्स पूर्ण करण्यासाठी जास्त वेळ मिळावा यासाठी. क्युरिंग एजंटचा वापर आवश्यक वेळेनुसार प्रवाह आणि समतल करण्यासाठी उपलब्ध कमी केला जातो आणि अशा प्रकारे त्या अत्यंत सक्रिय पावडरपासून बनलेली कोटिंग फिल्म सहसा संत्र्याची साल सादर करते.
कोटिंग फ्लो आणि लेव्हलिंगवर परिणाम करणारे महत्त्वाचे घटक म्हणजे राळची वितळलेली चिकटपणा, प्रणालीचा पृष्ठभाग तणाव आणि फिल्मची जाडी. या बदल्यात, वितळण्याची चिकटपणा, विशेषत: क्यूरिंग तापमान, बरे होण्याचा दर आणि गरम होण्याच्या दरावर अवलंबून असते.
वर नमूद केलेले विविध घटक, एकत्र कण आकार वितरण आणि चित्रपट जाडी, सहसा चित्रित वस्तू आणि पावडर बांधकाम परिस्थिती निर्णय आवश्यक चित्रपट गुणधर्म द्वारे केले जाते. पावडर कोटिंग प्रणालीच्या पृष्ठभागाच्या तणावातून वीज प्रवाह आणि समतल करणे, या आघाडीचा देखील उल्लेख केला आहे. याउलट कोटिंग फिल्ममधील रेणूंमधील आकर्षणावर लागू केलेले बल, परिणाम, जसे की वितळलेली चिकटपणा जास्त, प्रवाह आणि समतलीकरण विरुद्ध जास्त प्रतिकार. अशाप्रकारे, पृष्ठभागावरील ताण आणि गुरुत्वाकर्षणातील फरकाचा आण्विक आकार कोटिंग फिल्म लेव्हलिंगची व्याप्ती निर्धारित करतो.
चांगल्या प्रवाहक्षमतेसह कोटिंगसाठी, हे स्पष्ट आहे की प्रणालीचा पृष्ठभाग तणाव शक्य तितका जास्त असावा आणि वितळण्याची चिकटपणा शक्य तितकी कमी असावी. हे ऍडिटीव्ह जोडून प्रणालीच्या पृष्ठभागावरील ताणतणाव सुधारले जाऊ शकते आणि कमी आण्विक वजनाच्या राळच्या कमी वितळण्याच्या बिंदूचा वापर केला जाऊ शकतो.
कोटिंग तयार करण्याची प्रक्रिया
उत्कृष्ट प्रवाह गुणधर्म असलेल्या वरील परिस्थितीनुसार कोटिंग्ज तयार केल्या जाऊ शकतात, परंतु त्याच्या उच्च पृष्ठभागाच्या तणावामुळे संकोचन होते, कमी वितळलेल्या स्निग्धतामुळे सॅगिंग निर्माण होते आणि कोपरे खराब coatability. व्यावहारिक कार्यामध्ये, पृष्ठभागावरील ताण आणि प्रणालीची वितळणारी चिकटपणा एका विशिष्ट श्रेणीमध्ये नियंत्रित केली जाते, त्यामुळे योग्य कोटिंग पृष्ठभागाचे स्वरूप प्राप्त केले जाऊ शकते.
कोटिंग फिल्मच्या प्रवाहाच्या पृष्ठभागावरील ताण आणि वितळलेल्या चिकटपणाचा प्रभाव आकृती 2 मध्ये दर्शविला आहे. आकृतीमध्ये पाहिल्याप्रमाणे, खूप कमी किंवा खूप जास्त वितळलेल्या स्निग्धतेचा पृष्ठभाग तणाव कोटिंगचा प्रवाह रोखेल, परिणामी एक कोटिंग फिल्म खराब प्रवाहक्षमता, आणि पृष्ठभागावरील ताण खूप जास्त आहे, फिल्म तयार करण्याच्या प्रक्रियेत खड्डे दिसतील. वितळलेल्या स्निग्धतेची भौतिक साठवण स्थिरता खूप कमी असल्याने पावडर बिघडते कोपऱ्यातील बांधकामाची खराब आवरणक्षमता आणि दर्शनी भागामध्ये बांधकाम खराब होते.
सारांशात, हे स्पष्ट आहे की, प्राप्त पावडर कोटिंग फिल्मच्या पृष्ठभागाची अंतिम स्थिती, दोष आणि कमतरता (जसे की संत्र्याची साल, खराब प्रवाहक्षमता, खड्डे, पिनहोल्स इ.) यांचा एकमेकांशी जवळचा संबंध आहे आणि ते जमा करण्याच्या प्रक्रियेत देखील समाविष्ट आहे. rheological शक्ती नियंत्रण मध्ये फेज बदल. पावडर कण आकार वितरण देखील कोटिंग फिल्म पृष्ठभाग देखावा प्रभावित करते. कण जितके लहान, तितके मोठे कण त्याच्या थर्मल क्षमतेमुळे कमी असतात, म्हणून त्याचा वितळण्याचा वेळ मोठ्या कणांपेक्षा कमी असतो, कोलेसेंट देखील जलद होते आणि कोटिंग फिल्मचे पृष्ठभाग चांगले तयार होते. लहान कणांच्या लांबीपेक्षा मोठे पावडर कण वितळण्याची वेळ, त्यावर तयार केलेल्या कोटिंग फिल्ममुळे संत्र्याच्या सालीचा प्रभाव निर्माण होऊ शकतो. इलेक्ट्रोस्टॅटिक पावडर बांधकाम पद्धती (कोरोना डिस्चार्ज किंवा घर्षण डिस्चार्ज), परंतु संत्र्याच्या सालीमध्ये एक घटक देखील तयार होतो.
प्रवाह आणि समतलीकरणाला चालना देण्यासाठी संत्र्याच्या सालीचा प्रभाव कसा कमी करायचा किंवा टाळायचा हे संत्र्याची साल कमी किंवा टाळू शकते. प्रणाली कमी वितळणारी स्निग्धता वापरते, समतलीकरणाचा विस्तारित वेळ आणि क्युरींग प्रक्रियेत पृष्ठभागावरील ताण जास्त असल्यास प्रवाह आणि समतलीकरण सुधारले जाऊ शकते. पृष्ठभागावरील ताण ग्रेडियंट नियंत्रित करण्यासाठी महत्वाचे पॅरामीटर्स म्हणजे संत्र्याची साल कमी केली जाते, तसेच कोटिंग फिल्मच्या पृष्ठभागाच्या पृष्ठभागावरील ताण एकसमान नियंत्रित करण्यासाठी, सर्वात लहान पृष्ठभागाचे क्षेत्रफळ प्राप्त करण्यासाठी.
संत्र्याची साल, खड्डे, पिनहोल्स यांसारख्या पृष्ठभागावरील दोष दूर करण्यासाठी, कोटिंगचे स्वरूप सुधारण्यासाठी फ्लो-प्रोमोटिंग एजंट किंवा लेव्हलिंग एजंटचा वापर वास्तविक कामात केला जातो. फ्लो-प्रोमोटिंग एजंटच्या चांगल्या कामगिरीमुळे वितळण्याची स्निग्धता कमी होऊ शकते, त्यामुळे वितळणे आणि रंगद्रव्य पसरण्यास हातभार लागतो, ज्यामुळे सब्सट्रेटची आर्द्रता, कोटिंगचा प्रवाह आणि समतलता सुधारते, तसेच पृष्ठभागावरील दोष दूर करण्यास मदत होते. हवा सोडणे सुलभ करण्यासाठी.
प्रवाह सुधारक डोस आणि परिणाम संबंध तपासले पाहिजे. अपुर्या प्रमाणात केशरी फळाची साल आकुंचन आणि जास्त प्रमाणात खाल्ल्याने चकचकीतपणा, धुके नष्ट होतात आणि वरच्या बाजूस रिकोट चिकटून समस्या निर्माण होतात. सामान्यतः, प्रीमिक्समध्ये प्रवाह सुधारक जोडला जातो. किंवा राळ मास्टर बॅच (राळ आणि 9/1 ते 8/2 चे ऍडिटीव्ह गुणोत्तर) बनलेले आहे किंवा पावडर स्वरूपात अजैविक वाहक वर शोषले जाते. पावडर पेंटमध्ये अॅडिटीव्हचे प्रमाण 0.5 ते 1.5% आहे (बाइंडर्समध्ये प्रभावी पॉलिमरची गणना केली जाते), परंतु कमी सांद्रता देखील चांगली असू शकते.
पॉलीअॅक्रिलेट फ्लो मॉडिफायर रेजिन मोठ्या प्रमाणावर वापरले जातात, जसे की पॉलीअॅक्रिलिक अॅसिड ब्युटाइल एस्टर (“एक्रोनल 4एफ”), अॅक्रेलिक अॅसिड इथाइल – इथाइल हेक्साइल अॅक्रिलेट कॉपॉलिमर आणि ब्यूटाइल अॅक्रिलेट – अॅक्रेलिक अॅसिड-हेक्साइल अॅक्रिलेट कॉपॉलिमर इ. विस्तृत एकाग्रता श्रेणी. सहसा polyacrylate पृष्ठभाग तणाव वर थोडे प्रभाव, ते एक तुलनेने स्थिर एकसमान पृष्ठभाग लागत लेप योगदान करू शकता. पृष्ठभागावरील ताण कमी करणार्या ऍडिटीव्ह (जसे की सिलिकॉन किंवा यासारख्या) च्या तुलनेत, ते पृष्ठभागावरील ताण कमी करत नाहीत आणि त्यामुळे समतलीकरणाला गती देण्यासाठी त्यांचा वापर केला जाऊ शकतो. ऍडिटीव्हच्या पृष्ठभागावरील ताण कमी करा ज्यामध्ये पृष्ठभाग सक्रिय घटक, फ्लोरिनेटेड अल्काइल एस्टर आणि सिलिकॉन समाविष्ट आहेत. ते सामील होणारी रक्कम अतिशय संवेदनशील आहे. बेंझोइन एक डिगॅसिंग एजंट आहे, त्याचा पृष्ठभागावरील ताण कमी करण्याचा प्रभाव देखील आहे, पावडर कोटिंगच्या कोटिंग फिल्मच्या पृष्ठभागाचे स्वरूप सुधारण्यासाठी मोठ्या प्रमाणावर वापरले जाते.
कोटिंग तयार करण्याची प्रक्रिया
टिप्पण्या बंद आहेत