분체도장 장비 구성
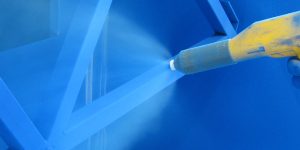
신청 방법은 다양합니다 분체 도료 재료, 그리고 seve가 있습니다ral 옵션용 분체 도장 장비. 단, 적용할 재료는 호환되는 유형이어야 합니다. 예를 들어, 적용 방법이 유동층인 경우. 분체 도료 재료는 유동층 등급이어야 하며 반대로 적용 방법이 정전 분무인 경우 분말 재료는 정전기 분무 등급이어야 합니다.
재료가 올바르게 선택되면 부품 설계 및 생산 목표에 따라 적용 방법이 선택됩니다. 적용 방법에는 두 가지 형태가 있습니다. 이들은 적합한 애플리케이션만큼 광범위합니다.
이러한 형식은 다음과 같습니다.
- 유동층 적용
- 스프레이 적용.
유동층
이 적용 방법은 분말 코팅 재료를 적용하는 데 사용된 첫 번째 방법입니다. 경화 후 필름 두께가 5.0mils를 초과하는 많은 응용 분야에서 오늘날에도 여전히 사용됩니다. 대표적인 품목은 전선 제품, 전기 버스 바 등입니다.
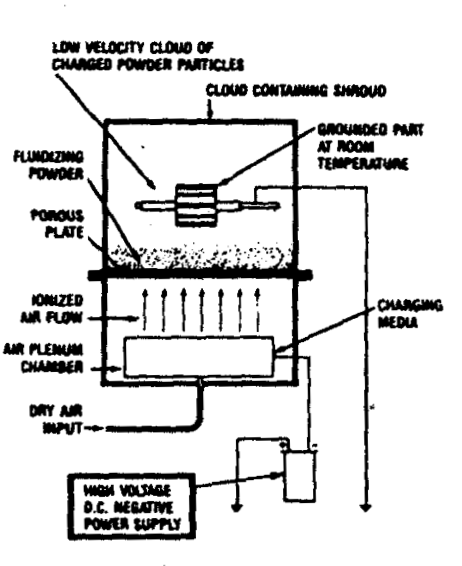
유동층 적용 방법은 두 가지 방법으로 수행할 수 있습니다. 한 가지 방법은 입니다. 이것은 분말이 녹고 접착되도록 부품을 예열해야 하는 공정입니다. 뜨거운 부분은 코팅을 위해 분말의 유동층에 놓입니다. 부품에 적용되는 분말의 양은 부품이 얼마나 뜨거운지, 얼마나 오랫동안 베드에 있는지에 따라 다릅니다. 이 방법을 사용할 때 필름 두께의 제어가 주요 관심사가 아님이 분명합니다.
유동층 시스템에서 부품의 필름 두께를 더 잘 제어하기 위해 정전기 원리가 도입되었습니다. 그림 1과 같이 부품이 유동층 위로 이송되고 분말이 유동층에 끌립니다. 이제 부품을 베드 위에 놓기 전에 예열할 필요가 없습니다. 분말은 분말 입자의 정전기에 의해 부품에 끌립니다. 이 정전기 전하는 유동층 위나 유동층의 정전기장에서 발생합니다.
부품의 필름 두께는 부품이 유동층에 있는 시간뿐만 아니라 분말 입자에 얼마나 많은 정전기 전하가 있는지에 의해 제어됩니다. 패러데이 케이지 문제를 일으킬 수 있는 부품 구성을 극복하기 위해 이 프로세스에서 열이 여전히 사용됩니다.
이 적용 방법은 전기 모터 전기자 코팅에 사용됩니다. 와이어가 적절하게 감기도록 하려면 필름 두께를 제어하는 높은 절연 강도 코팅이 필요합니다.
유동층 구조는 제조업체마다 다릅니다. 그러나 모든 디자인에 동일한 기본 구성 요소가 사용됩니다. 이러한 구성 요소는 호퍼 또는 탱크, 플레넘 또는 공기 챔버, 유동화 플레이트입니다. 설계, 제조업체 및 최종 용도에 따라 이러한 구성 요소 각각에 다른 재료가 사용됩니다. 예를 들어, 유동화 판은 다공성 폴리에틸렌, 공명판, 공예 종이, 또는 임의의 다공성 재료 또는 재료의 조합으로 만들어질 수 있습니다. 탱크는 분말의 무게를 지탱할 수 있는 모든 재료로 만들 수 있습니다.
스프레이 적용
정전기 스프레이 장비로 분체도장을 하는 방법은 두 가지로 나뉜다. 두 경우 모두 정전기를 사용하여 분말을 부품으로 끌어 당겨야 합니다. 기계적 인력이나 접착력이 없습니다. 액체 스프레이 시스템에서 볼 수 있는 부품에 대한 분말. 따라서 분말 또는 가열된 부분(열적 인력)이 기판에 흡착되어야 합니다. 이것을 설명하는 가장 좋은 비유는 풍선을 머리카락에 문지르면 정전기로 인해 풍선이 벽에 달라붙게 된다는 것입니다. 동일한 풍선은 정전기가 없으면 벽에 붙지 않습니다. 이 실험은 건조한(습하지 않은) 날에 수행해야 합니다. 두 가지 유형의 정전기 스프레이 분말 코팅 적용 장비는 다음과 같습니다.
- 코로나 대전 스프레이 건.
- 트라이보 차지 스프레이 건

암페어 제한, 전류 순환 또는 간헐적 전류 적용은 필요한 코팅 시간을 연장합니다. 이는 전착을 생성하는 적용된 암페어-초(쿨롱)이기 때문입니다.
전류 소비 범위는 완성된 코트 15g당 약 150쿨롱에서 최대 XNUMX쿨롱/g입니다. 초기 암페어 서지 후, 새로 증착된 필름의 높은 전기 저항은 전류 흐름을 감소시켜 과도하게rall 100~XNUMX분 동안 제곱피트당 XNUMX~XNUMX암페어 또는 XNUMX제곱피트당 XNUMX~XNUMX킬로와트시 필요. 코팅 시간은 일반적으로 XNUMX분에서 XNUMX분입니다. 전선과 같은 일부 특수 작업의 경우. 강철 밴드 등의 코팅 시간은 XNUMX초 정도로 짧은 것으로 보고됩니다.
전압 요구 사항은 주로 수조에 분산된 수지의 특성에 따라 달라집니다. 설비는 일반적으로 200볼트에서 400볼트 사이에서 작동되지만 일부는 50볼트만큼 낮게 작동되고 다른 것은 1000볼트만큼 높게 작동되는 것으로 보고됩니다.
헹굼:
갓 코팅된 조각을 욕조에서 들어올리면 욕조 물방울과 페인트 웅덩이가 떠오릅니다. 코팅되는 작업물 주변에는 고농도의 페인트 고형물이 존재합니다. 자동차 차체는 약 1갤런의 배스를 운반(인출)할 수 있는 것으로 추정됩니다. 10wt% 비휘발성 물질에서 이것은 약 1lb. 고체입니다. 코팅되는 표면을 향한 고체의 이동을 고려하면 그 부근에서 최대 35%의 고체 농도가 예상됩니다. 따라서, 들어 올려진 페인트 수조의 회수가 필요하고 수익성 있는 방법이 "한외여과액 린스"의 형태로 발견되었다는 것이 분명합니다.
한외여과는 용매, 가용화제, 염(불순물!) 등과 같이 물과 완전히 용해된 물질의 통과를 허용하는 막을 사용합니다. 분산된 페인트 수지, 안료 등은 막에 의해 유지됩니다. 7갤런 이상의 수조는 압력 하에서 멤브레인의 한 면을 통과하는 반면 85갤런의 투명한 수성 유체는 멤브레인을 통과합니다. 투과액 또는 한외여과액이라고 하는 액체가 수집되어 헹굼액으로 사용됩니다(그림 XNUMX). XNUMX단계 헹굼 시스템은 수조에서 제거된 페인트 고형물의 약 XNUMX%를 회수합니다.
일정량의 한외여과물이 버려지는 경우가 있는데, 이로 인해 덤프 현장으로 트럭 운송이 필요할 수 있습니다. 이러한 폐기물의 양은 역삼투압에 의해 감소될 수 있습니다.
굽거나 치료:
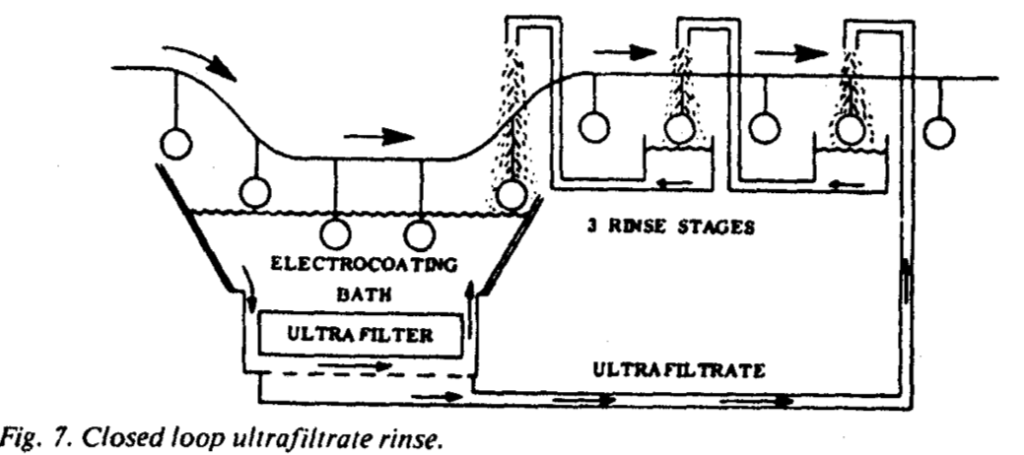
경화를 위한 시간/온도 요구 사항은 수지 시스템에 의해 결정되며 기존의 딥 또는 스프레이 페인트에 요구되는 것과 유사합니다. 일반적으로 5'F ~ 25°F 대기 온도에서 250-400분입니다. 공기 건조 전기 코팅이 시장에 나와 있습니다.
장비
코팅 탱크.
두 가지 유형의 탱크가 사용됩니다.
- 탱크 벽은 상대 전극으로 사용됩니다.
- 탱크 벽은 전기 절연 코팅으로 라이닝되어 있고 상대 전극은 탱크에 삽입된 다음 작업물의 크기 또는 모양에 따라 배치됩니다. 일부 설비에서는 전극이 구획으로 둘러싸여 있으며, 그 중 한 면은 멤브레인으로 구성되어 있습니다. 반대 이온 "X" 또는 "Y"(표 1)는 전기투석이라고 하는 과정에 의해 전극 구획에 축적되고 폐기되거나 재사용됩니다.
동요:
6~30분 안에 전체 수조 부피를 이동하거나 뒤집을 수 있는 펌프, 드래프트 튜브, 라인 샤프트 및 이젝터-노즐 시스템은 페인트가 탱크에 침전되는 것을 방지하는 데 사용됩니다.
여과:
일반적으로 5~75미크론 공극 크기의 필터를 사용하여 30~120분 안에 필터를 통해 전체 페인트 볼륨을 통과시킵니다. 산성 공급 재료는 40% ~ 99+% 범위의 페인트 고형분 농도로 제조 및 배송됩니다. 일부 설비에서 공급물은 두 가지 이상의 구성 요소 형태로 탱크에 계량됩니다. 한 구성 요소는 수지이고 다른 구성 요소는 안료 슬러리입니다.
가용화제 제거 방법:
항온조를 작동 상태로 유지하기 위해 남은 가용화제를 전기투석, 이온 교환 또는 투석 방법을 통해 제거합니다.
냉각 장비:
실제로 적용된 모든 전기 에너지는 열로 변환됩니다. 냉각 장비는 페인트 공급업체가 지정한 대로 원하는 수조 온도(일반적으로 70°F ~ 90F)를 유지하기에 적절해야 합니다.
굽거나 치료하십시오:
기존의 오븐 유형이 사용됩니다. 오븐을 통한 공기 속도는 페인트 코트에 매우 적은 양의 유기 휘발성 물질로 인해 비교적 낮습니다.
전원:
리플 계수가 10% 미만인 직류를 공급하는 정류기가 일반적으로 지정됩니다. 탭 스위치, 유도 조정기, 포화 코어 리액터 등과 같은 다양한 출력 전압 제어가 사용됩니다. 일반적으로 50~500V 범위의 전압이 제공됩니다. 현재 요구 사항은 사용 가능한 시간에 적용할 코팅의 무게에서 계산됩니다.
댓글이 닫혔습니다