കോട്ടിംഗ് രൂപീകരണ പ്രക്രിയ
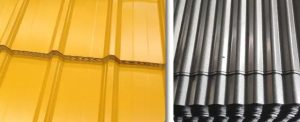
കോട്ടിംഗ് രൂപീകരണ പ്രക്രിയയെ മെൽറ്റ് കോലസെൻസായി വിഭജിച്ച് മൂന്ന് ഘട്ടങ്ങളായി ഒരു കോട്ടിംഗ് ഫിലിം രൂപപ്പെടുത്താം.
ഒരു നിശ്ചിത ഊഷ്മാവിൽ, റെസിൻ ദ്രവണാങ്കം, പൊടി കണങ്ങളുടെ ഉരുകിയ അവസ്ഥയുടെ വിസ്കോസിറ്റി, പൊടി കണങ്ങളുടെ വലിപ്പം എന്നിവയാണ് നിയന്ത്രണ ഉരുകിയ സംയോജന നിരക്ക് ഏറ്റവും പ്രധാനപ്പെട്ട ഘടകം. ലെവലിംഗ് ഫേസ് ഫ്ലോ ഇഫക്റ്റുകൾ പൂർത്തിയാക്കാൻ കൂടുതൽ സമയം ലഭിക്കുന്നതിന്, ഉരുകിയതിന്റെ മികച്ച സംയോജനം എത്രയും വേഗം ചെയ്യണം. ഒരു ക്യൂറിംഗ് ഏജന്റിന്റെ ഉപയോഗം ചുരുക്കി, ആവശ്യമായ സമയത്തിന്റെ ഒഴുക്കിനും ലെവലിംഗിനും ലഭ്യമാണ്, അങ്ങനെ വളരെ സജീവമായ പൊടിയിൽ നിന്ന് രൂപംകൊണ്ട കോട്ടിംഗ് ഫിലിം പലപ്പോഴും ഓറഞ്ച് തൊലി അവതരിപ്പിക്കുന്നു.
കോട്ടിംഗ് ഫ്ലോയെയും ലെവലിംഗിനെയും ബാധിക്കുന്ന പ്രധാന ഘടകങ്ങൾ റെസിൻ ഉരുകുന്ന വിസ്കോസിറ്റി, സിസ്റ്റത്തിന്റെ ഉപരിതല പിരിമുറുക്കം, ഫിലിം കനം എന്നിവയാണ്. അതാകട്ടെ, ഉരുകുന്ന വിസ്കോസിറ്റി, പ്രത്യേകിച്ച് ക്യൂറിംഗ് താപനില, ക്യൂറിംഗ് നിരക്ക്, ചൂടാക്കൽ നിരക്ക് എന്നിവയെ ആശ്രയിച്ചിരിക്കുന്നു.
മുകളിൽ സൂചിപ്പിച്ച വിവിധ ഘടകങ്ങൾ, കണികാ വലിപ്പം വിതരണവും ഫിലിം കനവും ഒരുമിച്ചു, സാധാരണയായി നിർണ്ണയിക്കുന്നത് വസ്തുക്കൾ പെയിന്റ് ചെയ്യേണ്ട ഫിലിം പ്രോപ്പർട്ടികൾ, പൊടി നിർമ്മാണ സാഹചര്യങ്ങൾ എന്നിവ നിർണ്ണയിക്കുന്നു. പൊടി കോട്ടിംഗ് സിസ്റ്റത്തിന്റെ ഉപരിതല പിരിമുറുക്കത്തിൽ നിന്നുള്ള വൈദ്യുതിയുടെ ഒഴുക്കും നിരപ്പും, ഈ മുൻഭാഗവും സൂചിപ്പിച്ചിട്ടുണ്ട്. നേരെമറിച്ച് കോട്ടിംഗ് ഫിലിമിലെ തന്മാത്രകൾ തമ്മിലുള്ള ആകർഷണത്തിന് പ്രയോഗിച്ച ശക്തി, ഉരുകിയ വിസ്കോസിറ്റി പോലുള്ള ഫലം കൂടുതലാണ്, ഒഴുക്കിനും നിരപ്പിനുമെതിരായ പ്രതിരോധം കൂടുതലാണ്. അങ്ങനെ, ഉപരിതല പിരിമുറുക്കവും ഗുരുത്വാകർഷണം തമ്മിലുള്ള വ്യത്യാസത്തിന്റെ തന്മാത്രാ വലുപ്പവും കോട്ടിംഗ് ഫിലിം ലെവലിംഗിന്റെ വ്യാപ്തി നിർണ്ണയിക്കുന്നു.
നല്ല ഫ്ലോബിലിറ്റി ഉള്ള ഒരു കോട്ടിംഗിനായി, സിസ്റ്റത്തിന്റെ ഉപരിതല പിരിമുറുക്കം കഴിയുന്നത്ര ഉയർന്നതായിരിക്കണമെന്ന് വ്യക്തമാണ്, കൂടാതെ ഉരുകിയ വിസ്കോസിറ്റി കഴിയുന്നത്ര കുറവാണ്. സിസ്റ്റത്തിന്റെ ഉപരിതല പിരിമുറുക്കത്തിലേക്ക് അഡിറ്റീവുകൾ ചേർത്ത് മെച്ചപ്പെടുത്താനും കുറഞ്ഞ തന്മാത്രാ ഭാരമുള്ള റെസിൻ കുറഞ്ഞ ദ്രവണാങ്കം ഉപയോഗിക്കുന്നതിലൂടെയും ഇവ നേടാനാകും.
കോട്ടിംഗ് രൂപീകരണ പ്രക്രിയ
മേൽപ്പറഞ്ഞ വ്യവസ്ഥകൾക്കനുസൃതമായി മികച്ച ഫ്ലോ പ്രോപ്പർട്ടികൾ ഉള്ള കോട്ടിംഗുകൾ തയ്യാറാക്കാം, പക്ഷേ അതിന്റെ ഉയർന്ന ഉപരിതല പിരിമുറുക്കം കാരണം ചുരുങ്ങലിന് കാരണമാകുന്നു, താഴ്ന്ന ഉരുകിയ വിസ്കോസിറ്റി കാരണം തൂങ്ങിക്കിടക്കും, കോണുകൾ മോശമായ കോട്ടബിലിറ്റിയും സൃഷ്ടിക്കും. പ്രായോഗിക പ്രവർത്തനത്തിൽ, സിസ്റ്റത്തിന്റെ ഉപരിതല പിരിമുറുക്കവും ഉരുകൽ വിസ്കോസിറ്റിയും ഒരു പ്രത്യേക പരിധിക്കുള്ളിൽ നിയന്ത്രിക്കപ്പെടുന്നു, അതിനാൽ യോഗ്യതയുള്ള കോട്ടിംഗ് ഉപരിതല രൂപം ലഭിക്കും.
കോട്ടിംഗ് ഫിലിമിന്റെ ഒഴുക്കിന്റെ ഉപരിതല പിരിമുറുക്കത്തിന്റെയും ഉരുകൽ വിസ്കോസിറ്റിയുടെയും ആഘാതം ചിത്രം 2-ൽ കാണിച്ചിരിക്കുന്നു. ചിത്രത്തിൽ കാണുന്നത് പോലെ, വളരെ താഴ്ന്നതോ വളരെ ഉയർന്നതോ ആയ മെൽറ്റ് വിസ്കോസിറ്റിയുടെ ഉപരിതല പിരിമുറുക്കം കോട്ടിംഗ് ഫ്ലോയെ തടയും, ഫലമായി ഒരു കോട്ടിംഗ് ഫിലിം മോശം ഫ്ലോബിലിറ്റി, കൂടാതെ ഉപരിതല പിരിമുറുക്കം വളരെ കൂടുതലാണ്, ഫിലിം രൂപീകരണ പ്രക്രിയ ഗർത്തങ്ങൾ പ്രത്യക്ഷപ്പെടും. ഉരുകിയ വിസ്കോസിറ്റിയുടെ ഫിസിക്കൽ സ്റ്റോറേജ് സ്ഥിരത വളരെ കുറവാണ്, പൊടി വഷളാകാൻ ഇടയാക്കും, ഒരു മൂലയുടെ നിർമ്മാണത്തിന്റെ മോശം കോട്ടബിലിറ്റി, കൂടാതെ മുൻഭാഗം തൂങ്ങിക്കിടക്കുന്ന നിർമ്മാണം.
ചുരുക്കത്തിൽ, ലഭിച്ച പൊടി കോട്ടിംഗ് ഫിലിമിന്റെ അവസാന ഉപരിതല അവസ്ഥ, വൈകല്യങ്ങളും കുറവുകളും (ഓറഞ്ച് തൊലി, മോശം ഒഴുക്ക്, ഗർത്തങ്ങൾ, പിൻഹോളുകൾ മുതലായവ) പരസ്പരം ബന്ധപ്പെട്ടിരിക്കുന്നു, കൂടാതെ നിക്ഷേപ പ്രക്രിയയിൽ ഉൾപ്പെട്ടിരിക്കുന്നതും വ്യക്തമാണ്. റിയോളജിക്കൽ ഫോഴ്സ് നിയന്ത്രണത്തിൽ ഘട്ടം മാറ്റം. പൊടി കണിക വലിപ്പം വിതരണം കോട്ടിംഗ് ഫിലിമിന്റെ ഉപരിതല രൂപത്തെയും ബാധിക്കുന്നു. ചെറിയ കണികകൾ, അതിന്റെ താപ ശേഷി കാരണം താഴ്ന്ന വലിയ കണങ്ങൾ, അതിനാൽ അതിന്റെ ദ്രവണാങ്കം സമയം വലിയ കണങ്ങളെ അപേക്ഷിച്ച് ചെറുതാണ്, coalescents പുറമേ വേഗത്തിലാണ്, പൂശുന്നു ഫിലിമിന്റെ മെച്ചപ്പെട്ട ഉപരിതല രൂപം രൂപം. ചെറിയ കണങ്ങളുടെ ദൈർഘ്യത്തേക്കാൾ വലിയ പൊടി കണികകൾ ഉരുകുന്ന സമയം, ഓറഞ്ചിന്റെ തൊലി പ്രഭാവം ഉണ്ടാക്കിയേക്കാം. ഇലക്ട്രോസ്റ്റാറ്റിക് പൊടി നിർമ്മാണ രീതികൾ (കൊറോണ ഡിസ്ചാർജ് അല്ലെങ്കിൽ ഘർഷണം ഡിസ്ചാർജ്), മാത്രമല്ല ഓറഞ്ച് പീൽ ഒരു ഘടകം രൂപീകരണം നയിക്കുന്നു.
ഒഴുക്ക് പ്രോത്സാഹിപ്പിക്കുന്നതിന് ഓറഞ്ച് തൊലി പ്രഭാവം എങ്ങനെ കുറയ്ക്കാം അല്ലെങ്കിൽ ഒഴിവാക്കാം, ഓറഞ്ച് തൊലി കുറയ്ക്കുകയോ ഒഴിവാക്കുകയോ ചെയ്യാം. സിസ്റ്റം കുറഞ്ഞ മെൽറ്റ് വിസ്കോസിറ്റി ഉപയോഗിക്കുന്നു, വിപുലീകൃത സമയം ലെവലിംഗ് ചെയ്യുന്നു, കൂടാതെ ക്യൂറിംഗ് പ്രക്രിയയിലെ ഉയർന്ന ഉപരിതല പിരിമുറുക്കം, ഒഴുക്കും ലെവലിംഗും മെച്ചപ്പെടുത്താൻ കഴിയും. ഉപരിതല ടെൻഷൻ ഗ്രേഡിയന്റ് നിയന്ത്രിക്കുന്നതിനുള്ള പ്രധാന പാരാമീറ്ററുകൾ ഓറഞ്ച് പീൽ കുറയ്ക്കുന്നു, അതേസമയം കോട്ടിംഗ് ഫിലിം ഉപരിതലത്തിന്റെ ഉപരിതല പിരിമുറുക്കം നിയന്ത്രിക്കുന്നത് ഏറ്റവും ചെറിയ ഉപരിതല വിസ്തീർണ്ണം ലഭിക്കുന്നതിന് ഏകതാനമാണ്.
ഓറഞ്ചിന്റെ തൊലി, ഗർത്തങ്ങൾ, പിൻഹോളുകൾ തുടങ്ങിയ ഉപരിതല വൈകല്യങ്ങൾ ഇല്ലാതാക്കാൻ, കോട്ടിംഗിന്റെ രൂപം മെച്ചപ്പെടുത്തുന്നതിന്, ഫ്ലോ-പ്രൊമോട്ടിംഗ് ഏജന്റ് അല്ലെങ്കിൽ ലെവലിംഗ് ഏജന്റ് പലപ്പോഴും യഥാർത്ഥ ജോലിയിൽ ഉപയോഗിക്കുന്നു. ഒരു ഫ്ലോ-പ്രൊമോട്ടിംഗ് ഏജന്റിന്റെ നല്ല പ്രകടനം ഉരുകിയ വിസ്കോസിറ്റി കുറയ്ക്കും, അങ്ങനെ ഉരുകൽ മിശ്രിതത്തിനും പിഗ്മെന്റ് ചിതറിക്കിടക്കുന്നതിനും കാരണമാകുന്നു, അടിവസ്ത്രത്തിന്റെ ഈർപ്പം മെച്ചപ്പെടുത്താനും കോട്ടിംഗിന്റെ ഒഴുക്കും നിരപ്പും മെച്ചപ്പെടുത്താനും, ഉപരിതല വൈകല്യങ്ങൾ ഇല്ലാതാക്കാനും സഹായിക്കുന്നു. വായു പ്രകാശനം സുഗമമാക്കുന്നതിന്.
ഫ്ലോ മോഡിഫയർ ഡോസേജും ഇഫക്റ്റ് ബന്ധവും അന്വേഷിക്കണം. അപര്യാപ്തമായ അളവ് ഓറഞ്ചിന്റെ തൊലി ചുരുങ്ങുന്നതിനും, അമിതമായ ഉപഭോഗം തിളക്കം, മൂടൽമഞ്ഞ് എന്നിവ നഷ്ടപ്പെടുന്നതിനും മുകളിലെ ഭാഗത്ത് റീകോട്ട് അഡീഷൻ പ്രശ്നങ്ങൾ ഉണ്ടാക്കുന്നതിനും ഇടയാക്കും. സാധാരണഗതിയിൽ, പ്രീമിക്സിലെ ഫ്ലോ മോഡിഫയർ ചേർത്തു. അല്ലെങ്കിൽ ഒരു റെസിൻ മാസ്റ്റർ ബാച്ച് (റെസിൻ, അഡിറ്റീവ് അനുപാതം 9/1 മുതൽ 8/2 വരെ), അല്ലെങ്കിൽ പൊടി രൂപത്തിൽ അജൈവ കാരിയറിൽ ആഗിരണം ചെയ്യപ്പെടുന്നു. പൊടി പെയിന്റിലെ അഡിറ്റീവുകളുടെ അളവ് 0.5 മുതൽ 1.5% വരെയാണ് (ബൈൻഡറുകളിൽ ഫലപ്രദമായ പോളിമർ കണക്കാക്കുന്നത്), എന്നാൽ കുറഞ്ഞ സാന്ദ്രതയിലും നല്ലതായിരിക്കാം.
പോളിഅക്രിലേറ്റ് ഫ്ലോ മോഡിഫയർ റെസിനുകൾ ഏറ്റവും വ്യാപകമായി ഉപയോഗിക്കപ്പെടുന്നു, ഉദാഹരണത്തിന്, പോളിഅക്രിലിക് ആസിഡ് ബ്യൂട്ടൈൽ ഈസ്റ്റർ ("അക്രോണൽ 4F"), അക്രിലിക് ആസിഡ് എഥൈൽ - എഥൈൽ ഹെക്സിൽ അക്രിലേറ്റ് കോപോളിമർ, ബ്യൂട്ടൈൽ അക്രിലേറ്റ് - അക്രിലിക് ആസിഡ്-ഹെക്സിൽ അക്രിലേറ്റ് കോപോളിമർ മുതലായവ. വിശാലമായ ഏകാഗ്രത പരിധി. സാധാരണയായി പോളിഅക്രിലേറ്റ് ഉപരിതല പിരിമുറുക്കത്തിൽ ചെറിയ സ്വാധീനം ചെലുത്തുന്നു, അവ താരതമ്യേന സ്ഥിരമായ ഏകീകൃത ഉപരിതലം രൂപപ്പെടുത്തുന്നതിന് കോട്ടിംഗിന് കാരണമാകും. ഉപരിതല പിരിമുറുക്കം കുറയ്ക്കുന്ന അഡിറ്റീവുകളുമായി താരതമ്യപ്പെടുത്തുമ്പോൾ (സിലിക്കൺ അല്ലെങ്കിൽ മറ്റുള്ളവ), അവ ഉപരിതല പിരിമുറുക്കം കുറയ്ക്കുന്നില്ല, അതിനാൽ ലെവലിംഗ് ത്വരിതപ്പെടുത്തുന്നതിന് ഇത് ഉപയോഗിക്കാം. അഡിറ്റീവുകളുടെ ഉപരിതല പിരിമുറുക്കം കുറയ്ക്കുക, ഉപരിതല സജീവമായ ഏജന്റുകൾ, ഫ്ലൂറിനേറ്റഡ് ആൽക്കൈൽ എസ്റ്ററുകൾ, സിലിക്കൺ എന്നിവ ഉൾപ്പെടുന്നു. അവർ തുക ചേരുന്നത് വളരെ സെൻസിറ്റീവ് ആണ്. ബെൻസോയിൻ ഒരു ഡീഗ്യാസിംഗ് ഏജന്റാണ്, കൂടാതെ ഉപരിതല പിരിമുറുക്കം കുറയ്ക്കുന്നതിനുള്ള ഫലവുമുണ്ട്, പൊടി കോട്ടിംഗിന്റെ കോട്ടിംഗ് ഫിലിമിന്റെ ഉപരിതല രൂപം മെച്ചപ്പെടുത്താൻ വ്യാപകമായി ഉപയോഗിക്കുന്നു.
കോട്ടിംഗ് രൂപീകരണ പ്രക്രിയ
അഭിപ്രായ സമയം കഴിഞ്ഞു