부식 방지 에폭시 분말 코팅은 보호 기능을 합니다.
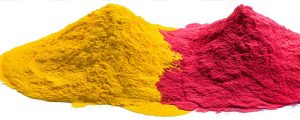
음극 보호 및 부식 방지 층의 공동 적용으로 지하 또는 수중 금속 구조가 가장 경제적이고 효과적인 보호를 얻을 수 있습니다. 일반적으로 사용하기 전에 보호 코팅으로 코팅되어 금속 및 유전체 환경의 전기 절연 절연에 좋은 코팅은 외부 표면 구조의 99% 이상을 부식으로부터 보호할 수 있습니다. 생산, 운송 및 건설에서 파이프 코팅은 손상 (입 코팅, 코팅 밀도, 코팅 핀홀 등)에 대해 절대적으로 보장 할 수 없으며 파이프 라인 부식 환경이 완전히 격리 될 수 없습니다. 그러나 다양한 재료의 부식 방지 절연 층에도 다양한 정도, 흡수성 및 통기성이 있으며 점차적으로 흡수제가 묻힐 것입니다. 효과적인 부식 방지를 유지하려면 음극 보호, 즉 조인트 보호를 취하는 것이 필요합니다. 두꺼운 코팅(두께> 1mm), 파이프라인 조인트 보호는 -1.10 ~-1.15V(CSE)의 보호 전위를 선택해야 하며, 얇은 코팅(두께 ≤ 1mm)은 -1.05 ~-1.10V(CSE)의 보호 전위를 취해야 합니다. 토양 조성, 습도, 온도, 코팅 유형, 코팅 품질 및 미생물을 고려하여 부식 방지 코팅을 파괴하지 않고 파이프라인을 보호하기 위해 보호 잠재력에 대한 적절한 조정. 분극 전류 평가 환경의 부식이 더 효과적입니다. "보호"는 여기서 중요한 개념이며 부식 방지 에폭시 분체 도료 제자리에, "보호"?
코팅의 코팅된 음극 스트리핑, 파괴적인 영향, 실제 매장된 강철 파이프라인을 실행하여 최고의 보호 잠재력을 가진 음극 보호 코팅(3PE 코팅, 기본 융착 에폭시 분말)을 탐색할 가치가 있는 이유를 선택했습니다. 최고의 보호 가능성에 대해. 외국 학자의 전류 전위 곡선은 부식 및 음극 보호 상황, -1.15V의 강렬한 수소 탈착 반응 전위를 연구합니다. 말레이시아 조사에 따르면, Lloyd's Register, Shell은 -1.1V 제한 테이크 -1.15V의 최대 보호 잠재력을 제공합니다. 독일 표준 DIN30676-19853.1은 다음과 같이 읽습니다. 얇은 코팅(<1mm)에서 케이스는 부식 방지를 위해 사용되었으며, 극성으로 인해 물집이 형성되는 것과 같은 반대 영향을 미치므로 영향을 최소화하기 위해 제한해야 합니다. -1.00 ~-1.20V(상대 CSE)의 최대 보호 전위와 같은 코팅의 기능으로 보호 전위의 범위. 해외에서는 토양 조성, 습도, 온도, 코팅 유형, 코팅 품질 및 미생물, 산업 유전자를 포함한 여러 요인에 의해 코팅 실패의 잠재적인 원인을 구체적으로 언급ral-1.05 ~ – 1.10V(CSE) 손실 가능성이 있는 정전을 방지하기 위해 고려되었습니다(참고: 융합 에폭시 분말 코팅의 광범위한 사용). 음극 보호 납 코팅 (3PE 코팅 바닥 오프 메커니즘 융합 접착 에폭시 분말 코팅).
도막의 종류, 습도, 온도에 따라 도막의 흡수성, 내침투성이 도막두께의 함수로 결정되며 동일한 조건하에서 도막이 됩니다. 연구에 따르면 가교된 에폭시 수지는 물 분자가 에폭시 수지로 들어가는 일정한 양의 기공 및 기공 채널을 형성합니다. 용액은 금속 반응과의 계면에서 생성된 부식 생성물 필름으로 터널에서 코팅/금속 계면에 도달하고, 이 부식 생성물 필름 층은 금속과 용액의 반응을 방지하기 위해 코팅 저항이 점차 감소합니다. 점점 더 많은 부식성 이온이 계면에 도달하면 부식 생성물 필름의 이 층이 점차적으로 파괴되고 부식이 강화되어 궁극적으로 드럼에서 벗겨진 에폭시 코팅이 됩니다. 경화된 융합 결합형 에폭시 분말 코팅은 여전히 에테르 및 히드록실기가 풍부하며, 이러한 활성 그룹과 파이프 표면은 부식 방지 코팅을 형성하기 위해 화학적 결합에 의해 함께 단단히 결합됩니다. 코팅의 입을 채우십시오, 조밀하고, 핀홀 이유, 코팅은 물 흡수 및 투과성의 정도가 다릅니다. 음극 보호가 과도하면 축적된 활성 수소 원자와 함께 음극 수소 발생이 어느 정도 발생합니다. , 수소는 에테르와 수산기 반응을 일으켜 코팅과 강관의 결합 강도를 약화시켜 결합 강도가 사라집니다. 그 결과 강관에서 코팅이 벗겨집니다.
댓글이 닫혔습니다