कोटिंग बनाने की प्रक्रिया
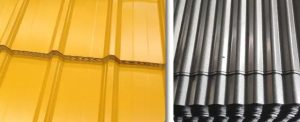
कोटिंग बनाने की प्रक्रिया को तीन चरणों को समतल करने वाली कोटिंग फिल्म बनाने के लिए पिघले हुए सहसंयोजन में विभाजित किया जा सकता है।
किसी दिए गए तापमान पर, नियंत्रण पिघला हुआ सहसंयोजन दर सबसे महत्वपूर्ण कारक राल का गलनांक, पाउडर कणों की पिघली हुई अवस्था की चिपचिपाहट और पाउडर कणों का आकार होता है। लेवलिंग फेज फ्लो इफेक्ट को पूरा करने के लिए अधिक समय देने के लिए जितनी जल्दी हो सके पिघला हुआ का सबसे अच्छा सहसंयोजन करने के लिए। आवश्यक समय के प्रवाह और समतलन के लिए उपलब्ध एक इलाज एजेंट का उपयोग, और इस प्रकार उन अत्यंत सक्रिय पाउडर से बनी कोटिंग फिल्म अक्सर संतरे के छिलके को प्रस्तुत करती है।
कोटिंग के प्रवाह और समतलन को प्रभावित करने वाले प्रमुख कारक राल की पिघली हुई चिपचिपाहट, सिस्टम की सतह का तनाव और फिल्म की मोटाई है। बदले में, पिघल चिपचिपापन, विशेष रूप से इलाज तापमान, इलाज दर और हीटिंग दर पर निर्भर करता है।
ऊपर वर्णित विभिन्न कारक, कण आकार वितरण और फिल्म मोटाई के साथ, आमतौर पर आवश्यक फिल्म गुणों द्वारा चित्रित वस्तुओं और पाउडर निर्माण की स्थिति तय की जाती है। पाउडर कोटिंग प्रणाली के सतही तनाव से शक्ति के प्रवाह और समतलन, इस मोर्चे का भी उल्लेख किया गया है। इसके विपरीत कोटिंग फिल्म में अणुओं के बीच आकर्षण के लिए लागू बल, परिणाम, जैसे पिघला हुआ चिपचिपापन अधिक होता है, प्रवाह और स्तर के खिलाफ प्रतिरोध जितना अधिक होता है। इस प्रकार, सतह तनाव, और गुरुत्वाकर्षण के बीच अंतर के आणविक आकार कोटिंग फिल्म लेवलिंग की सीमा निर्धारित करते हैं।
अच्छी प्रवाह क्षमता वाले कोटिंग के लिए, यह स्पष्ट है कि सिस्टम का सतह तनाव जितना संभव हो उतना अधिक होना चाहिए, और पिघला हुआ चिपचिपापन जितना संभव हो उतना कम होना चाहिए। सिस्टम के सतह तनाव में एडिटिव्स को जोड़कर इन्हें प्राप्त किया जा सकता है और कम आणविक भार के राल के कम गलनांक का उपयोग किया जा सकता है।
कोटिंग बनाने की प्रक्रिया
उत्कृष्ट प्रवाह गुणों वाली उपरोक्त स्थितियों के अनुसार कोटिंग्स तैयार की जा सकती हैं, लेकिन इसकी उच्च सतह तनाव के कारण संकोचन का कारण बनता है, कम पिघल चिपचिपाहट के कारण सैगिंग उत्पन्न होगा, और कोनों में खराब कोटेबिलिटी होगी। व्यावहारिक कार्य में, सिस्टम की सतह के तनाव और पिघल चिपचिपाहट को एक विशिष्ट सीमा के भीतर नियंत्रित किया जाता है, इसलिए योग्य कोटिंग सतह उपस्थिति प्राप्त की जा सकती है।
कोटिंग फिल्म के प्रवाह की सतह तनाव और पिघल चिपचिपाहट का प्रभाव चित्रा 2 में दिखाया गया है। जैसा कि आंकड़े में देखा जा सकता है, बहुत कम या बहुत अधिक पिघला हुआ चिपचिपापन का सतह तनाव कोटिंग प्रवाह को रोक देगा, जिसके परिणामस्वरूप एक कोटिंग फिल्म खराब प्रवाह क्षमता, और सतह तनाव बहुत अधिक है फिल्म बनाने की प्रक्रिया क्रेटर दिखाई देगी। पिघल चिपचिपाहट की भौतिक भंडारण स्थिरता बहुत कम है, जिससे पाउडर खराब हो जाएगा एक कोने के निर्माण की खराब कोटेबिलिटी, और मुखौटा में निर्माण।
संक्षेप में, यह स्पष्ट है, प्राप्त पाउडर कोटिंग फिल्म की अंतिम सतह की स्थिति, दोष और कमियां (जैसे संतरे के छिलके, खराब प्रवाह क्षमता, क्रेटर, पिनहोल, आदि) बारीकी से परस्पर संबंधित हैं, और इसमें शामिल बयान प्रक्रिया में भी शामिल है रियोलॉजिकल फोर्स कंट्रोल में चरण परिवर्तन। पाउडर कण आकार वितरण भी कोटिंग फिल्म की सतह उपस्थिति को प्रभावित करता है। छोटे कण, इसकी तापीय क्षमता के कारण कम के बड़े कण, इसलिए इसके पिघलने का समय बड़े कणों की तुलना में कम होता है, सहसंयोजक भी तेज होते हैं, और कोटिंग फिल्म की बेहतर सतह उपस्थिति बनती है। छोटे कणों की लंबाई की तुलना में बड़े पाउडर कणों के पिघलने का समय, नारंगी छील प्रभाव उत्पन्न हो सकता है। इलेक्ट्रोस्टैटिक पाउडर निर्माण विधियों (कोरोना डिस्चार्ज या घर्षण निर्वहन), लेकिन नारंगी छील में एक कारक के गठन की ओर जाता है।
संतरे के छिलके के प्रभाव को कम करने या उससे बचने के लिए कैसे प्रवाह और समतलन को बढ़ावा देने के लिए संतरे के छिलके को कम किया जा सकता है या उससे बचा जा सकता है। सिस्टम कम पिघल चिपचिपाहट का उपयोग करता है, विस्तारित समय को समतल करता है और इलाज की प्रक्रिया में उच्च सतह तनाव को प्रवाह और समतलन में सुधार किया जा सकता है। सतह तनाव ढाल को नियंत्रित करने के लिए महत्वपूर्ण पैरामीटर नारंगी छील को कम करते हैं, जबकि कोटिंग फिल्म सतह की सतह तनाव को नियंत्रित करने के लिए सबसे छोटा सतह क्षेत्र प्राप्त करने के लिए समान है।
नारंगी छील, क्रेटर, पिनहोल जैसे सतह दोषों को खत्म करने के लिए, कोटिंग की उपस्थिति में सुधार के लिए फ्लो-प्रमोशन एजेंट या लेवलिंग एजेंट अक्सर वास्तविक कार्य में उपयोग किया जाता है। प्रवाह को बढ़ावा देने वाले एजेंट का अच्छा प्रदर्शन पिघल चिपचिपाहट को कम कर सकता है, इस प्रकार पिघल मिश्रण और वर्णक फैलाव में योगदान देता है, सब्सट्रेट की अस्थिरता में सुधार करने के लिए, कोटिंग का प्रवाह और स्तर, सतह दोषों को भी खत्म करने में मदद करता है हवा की रिहाई की सुविधा के लिए के रूप में।
प्रवाह संशोधक खुराक और प्रभाव संबंध की जांच की जानी चाहिए। अपर्याप्त मात्रा में सिकुड़न और संतरे के छिलके का कारण होगा, अत्यधिक खपत से चमक, धुंध का नुकसान होगा, और ऊपरी हिस्से पर फिर से परत लगाने की समस्या पैदा होगी। आम तौर पर, प्रीमिक्स में प्रवाह संशोधक जोड़ा जाता है। या एक राल मास्टर बैच (राल और 9/1 से 8/2 के योगात्मक अनुपात) से बना है, या पाउडर के रूप में अकार्बनिक वाहक पर adsorbed है। पाउडर पेंट में एडिटिव्स की मात्रा 0.5 से 1.5% (बाइंडर्स में गणना की गई प्रभावी पॉलिमर) है, लेकिन कम सांद्रता पर भी अच्छा हो सकता है।
Polyacrylate प्रवाह संशोधक रेजिन सबसे व्यापक रूप से उपयोग किया जाता है, जैसे कि पॉलीएक्रिलिक एसिड ब्यूटाइल एस्टर ("एक्रोनल 4F"), ऐक्रेलिक एसिड एथिल - एथिल हेक्साइल एक्रिलेट कोपोलिमर और ब्यूटाइल एक्रिलेट - ऐक्रेलिक एसिड-हेक्सिल एक्रिलेट कोपोलिमर, आदि। उनका उपयोग बहुत ही में किया जा सकता है। विस्तृत एकाग्रता रेंज। आमतौर पर पॉलीएक्रिलेट सतह के तनाव पर बहुत कम प्रभाव डालते हैं, वे अपेक्षाकृत स्थिर समान सतह बनाने वाले कोटिंग में योगदान कर सकते हैं। सतह के तनाव को कम करने वाले एडिटिव्स (जैसे सिलिकॉन या इसी तरह) की तुलना में, वे सतह के तनाव को कम नहीं करते हैं, और इसलिए लेवलिंग में तेजी लाने के लिए इस्तेमाल किया जा सकता है। एडिटिव्स की सतह के तनाव को कम करने के लिए सतह सक्रिय एजेंट, फ्लोरिनेटेड एल्काइल एस्टर और सिलिकॉन शामिल हैं। वे राशि में शामिल होते हैं बहुत संवेदनशील है। बेंज़ोइन एक degassing एजेंट है, सतह के तनाव को कम करने का भी प्रभाव पड़ता है, पाउडर कोटिंग की कोटिंग फिल्म की सतह की उपस्थिति में सुधार करने के लिए व्यापक रूप से उपयोग किया जाता है।
कोटिंग बनाने की प्रक्रिया
टिप्पणियाँ बंद हैं