Réparation de pièces et décapage de cintres en revêtement poudre
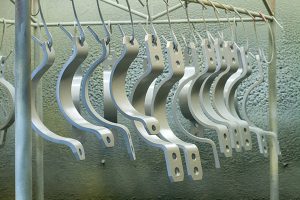
Les méthodes de réparation des pièces après revêtement en poudre peuvent être classés en deux catégories : retouche et recouvrement.
La réparation de retouche est appropriée lorsqu'une petite zone de la pièce revêtue n'est pas couverte et ne peut pas répondre aux spécifications de finition. Lorsque les marques de suspension ne sont pas acceptables, une retouche est nécessaire. La retouche peut également être utilisée pour réparer de légers dommages causés par la manipulation, l'usinage ou le soudage lors de l'assemblage.
Une nouvelle couche est nécessaire lorsqu'une pièce est rejetée en raison d'un défaut de grande surface ou lorsqu'une retouche n'est pas acceptable. À ce stade, il existe une variété d'options qui doivent être examinées attentivement. Habituellement, la partie rejetée peut être re-jumelée avec une deuxième couche. Une autre option consiste à décaper et repeindre la pièce. Le décapage peut également nettoyer les suspentes de pièces pour fournir un bon sol
pour pulvérisation électrostatique.
RETOUCHE
La peinture de retouche liquide est appliquée avec un petit pinceau, un aérosol ou un pistolet sans air. La peinture est séchée à l'air. Le processus de séchage peut être accéléré avec une cuisson à basse température. La peinture de retouche est utilisée après que le revêtement en poudre a été complètement durci dans un four de cuisson. Les marques de suspension, les taches légères dans les coins et les coutures, les dommages causés par le soudage ou l'assemblage et d'autres petits défauts peuvent être retouchés. Gèneraljustement, un Couleur-un émail ou une laque acrylique assortie est utilisé. La peinture de retouche ne peut pas être utilisée si elle ne répond pas aux spécifications de performance requises pendant la durée de vie prévue de cette pièce.
La retouche ne doit pas être utilisée pour réparer une finition défectueuse à moins que le produit résultant ne réponde aux normes d'inspection.
RECOUVRIR
L'application d'une deuxième couche de poudre est l'approche courante pour réparer et récupérer les pièces rejetées. Cependant, le défaut doit être soigneusement analysé et la source corrigée avant de recouvrir. Ne pas recouvrir si le rebut est causé par un défaut de fabrication, un substrat de mauvaise qualité, un nettoyage ou un prétraitement insuffisant, ou lorsque l'épaisseur de deux couches ensemble sera hors tolérance. De plus, si la pièce est rejetée en raison d'un sous-durcissement, il suffit de la recuire selon le calendrier requis.
Une deuxième couche est efficace pour couvrir les zones claires, les défauts de surface dus à la saleté et à la contamination, les points rugueux dus à la formation d'un film épais ou au crachat de pistolet, et le changement de couleur dû à une surcuisson sévère. Les surfaces rugueuses et les saillies doivent être poncées avant de recouvrir.
Les pièces inspectées en ligne peuvent être laissées sur le convoyeur pour recevoir une deuxième couche. Ces pièces peuvent passer par les étapes de prétraitement avec des pièces brutes. Si les pièces recouvertes présentent des taches d'eau ou des taches, un ajustement peut être effectué lors de l'étape de rinçage final.
Les fournisseurs de produits chimiques peuvent offrir des recommandations. Lorsque les pièces à recouvrir sont accrochées ensemble, le nettoyage et le prétraitement ne sont pas nécessaires. Cependant, si les pièces rejetées ont été stockées pour accumuler un nombre pratique, elles doivent être vérifiées pour la saleté et la contamination.
Enduire toute la partie
Lors de l'application de la deuxième couche, une épaisseur de mil normale doit être appliquée sur toute la pièce. Une erreur courante consiste à ne recouvrir que la zone défectueuse. Cela laisse une surface rugueuse et granuleuse où il n'y a qu'une très fine couche de surpulvérisation sur le reste de la pièce. Le même programme de cure recommandé est utilisé pour la deuxième couche.
L'adhérence intercouche peut être vérifiée après avoir recouvert des échantillons sélectionnés en utilisant le test de quadrillage ou en grattant simplement la surface pour voir si la deuxième couche se détache facilement de la première. Certains revêtements en poudre peuvent avoir besoin d'être légèrement poncés pour fournir un bon ancrage pour la deuxième couche.
RECUIRE
Lorsqu'une pièce n'est pas suffisamment polymérisée lors de la première couche, elle peut être réparée en la renvoyant simplement au four de cuisson pour un programme de polymérisation normal à l'heure et à la température spécifiées. Les propriétés seront récupérées lorsque la pièce sera correctement durcie, à quelques exceptions près, comme certains revêtements à faible brillance contrôlés chimiquement. Un durcissement partiel se traduira par une brillance plus élevée, qui ne tombera pas au même niveau pendant le durcissement final que celui qui aurait été obtenu avec un durcissement initial adéquat.
DÉCAPAGE
Le décapage est généralement la dernière alternative pour la réparation des pièces, car le décapage du produit rejeté peut augmenter considérablement les coûts de production et perturber le flux de la chaîne de production. Le décapage des pièces revêtues devient toutefois nécessaire lorsque le rebut est causé par un mauvais prétraitement ou lorsqu'une retouche ou deux couches ne sont pas acceptables.
D'autre part, le décapage joue un rôle important dans l'efficacité de la ligne de poudrage en fournissant des cintres propres pour une bonne mise à la terre électrique. Les cintres doivent être dépouillés périodiquement. Les méthodes de décapage sont discutées dans les paragraphes suivants. (Remarque : Il existe une divergence d'opinions selon laquelle le décapage chimique est la méthode préférée.)
Les décapants chimiques sont disponibles pour être utilisés à chaud (température élevée) ou à froid (ambiante) dans une cuve de trempage. Il existe des types de sels acides, alcalins et fondus, avec une sélection en fonction du type de pièces et de suspensions et du revêtement à enlever.
Le principal avantage des décapants chimiques est le faible investissement initial en capital pour l'équipement. Les inconvénients comprennent les risques pour la sécurité liés à la manipulation des produits chimiques, les coûts élevés de remplacement et d'élimination des produits chimiques et les produits chimiques chargés de peinture. Certaines pièces, telles que les alliages d'aluminium, peuvent ne pas résister à la corrosion des produits chimiques.
Brûler
Les fours à combustion ou à pyrolyse pour le décapage utilisent des températures élevées pour incinérer le revêtement. Il peut s'agir de fours de type batch ou en ligne qui fonctionnent à environ 800 ° F (427″ C), avec l'échappement antipollution fonctionnant à des températures d'environ 1200-1300 ° F (649-704 ° C). Les fours à combustion éliminent les problèmes de pollution et d'élimination. Leur fonctionnement est relativement efficace, mais ils nécessitent un investissement en capital important et nécessitent un certain type de post-nettoyage pour éliminer les cendres résiduelles. Les pièces doivent résister à des températures de 800°F (427°C). Certaines chimies de revêtement ne conviennent pas à cette technique de décapage. Consultez le fabricant de l'équipement et les organismes de réglementation locaux. Il convient également de noter que le décapage répété de l'outillage peut nécessiter un certain type d'alliage pour éviter la rupture ou la déformation.
Grenaillage
Le grenaillage ou l'abrasion peut être utilisé pour décaper des pièces ou des cintres lorsque d'autres méthodes ont été exclues. Ce processus est très lent en raison de la ténacité du revêtement en poudre durci. L'inconvénient de ce processus est qu'il érode (amincit) l'outillage et expose plus de surface, qui devient plus difficile à décaper lorsqu'il est recouvert.
Cryogénique
Le décapage cryogénique fragilise le film avec de l'azote liquide, puis utilise un grenaillage non abrasif pour enlever facilement le revêtement. C'est une méthode rapide et non polluante, mais elle nécessite un équipement spécialisé. Les pièces doivent supporter -100 °F (-37 °C) pour être prises en compte pour l'outillage.
GÉNÉRAL
Il convient de déterminer si les pièces peuvent ou non résister à l'une des méthodes décrites. Les fournisseurs de produits chimiques et d'équipements peuvent mesurer les températures, et certains types d'alliages peuvent devoir aider à cette détermination. En ce qui concerne l'outillage, une conception appropriée peut réduire la quantité de nettoyage nécessaire. Un crochet de pièce bon marché peut devenir très coûteux s'il doit être remplacé fréquemment.
Les commentaires sont fermés