Методи та вимоги Qualicoat-Test
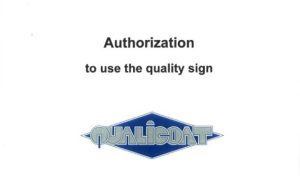
Методи та вимоги Qualicoat-Test
Методи Qualicoat-Test, описані нижче, використовуються для випробування готової продукції та/або систем покриття для затвердження (див. розділи 4 і 5).
Для механічних випробувань (розділи 2.6, 2.7 і 2.8) випробувальні панелі повинні бути виготовлені зі сплаву AA 5005-H24 або -H14 (AlMg 1 – напівтвердий) товщиною 0.8 або 1 мм, якщо інше не затверджено Технічним комітет.
Випробування з використанням хімічних речовин та випробування на корозію слід проводити на екструдованих секціях, виготовлених з AA 6060 або AA 6063.
1 Зовнішній вигляд
Зовнішній вигляд буде оцінено на значній поверхні.
Значна поверхня повинна бути визначена замовником і є частиною загальної поверхні, яка має важливе значення для зовнішнього вигляду та працездатності виробу. Краї, глибокі виїмки та вторинні поверхні не входять до значної поверхні. Покриття на значній поверхні не повинно мати жодних подряпин до основного металу. Коли покриття на значній поверхні розглядається під косим кутом приблизно 60° до верхньої поверхні, жоден з перерахованих нижче дефектів не повинен бути помітний з відстані 3 метри: надмірна шорсткість, розбіги, пухирі, включення, кратери, матові. плями, ямки, подряпини або будь-які інші неприпустимі недоліки.
Покриття має бути рівномірного кольору і блиску з хорошим покриттям. Під час перегляду на сайті ці критерії мають відповідати наступному:
- – для деталей, що використовуються зовні: дивитися на відстані 5 м
- – для деталей, що використовуються всередині: дивитися на відстані 3 м
2. Блиск
ISO 2813 – використання падаючого світла під кутом 60° до норми.
Примітка: якщо значуща поверхня занадто мала або непридатна для вимірювання блиску за допомогою глянцевого приладу, блиск слід візуально порівняти з еталонним зразком (під тим самим кутом огляду).
ВИМОГИ:
- Категорія 1 : 0 – 30 +/- 5 одиниць
- Категорія 2 : 31 – 70 +/- 7 одиниць
- Категорія 3 : 71 – 100 +/- 10 одиниць
(допустиме відхилення від номінального значення, зазначеного постачальником покриття)
3. Товщина покриття
EN ISO 2360
Товщину покриття на кожній деталі, що підлягає випробуванню, необхідно виміряти на значній поверхні не менше ніж на п'яти вимірювальних ділянках (приблизно 1 см2) з 3-5 окремими показаннями на кожній ділянці. Середнє значення окремих показань, знятих на одній вимірювальній ділянці, дає значення вимірювання, яке має бути записано в звітах про перевірку. Жодне з виміряних значень не може бути меншим за 80% зазначеного мінімального значення, інакше випробовування товщини в цілому буде вважатися незадовільним.
Методи та вимоги Qualicoat-Test
Порошки:
- Клас 11: 60 мкм
- Клас 2: 60 мкм
- Клас 3: 50 мкм
- Двошарова порошкова система (класи 1 і 2): 110 мкм
- Двошарове порошкове ПВДФ: 80 мкм
Рідке покриття
- Двошарова система PVDF: 35 мкм
- Тришарова металізована PVDF система: 45 мкм
- Силіконовий поліестер без Праймер для вій : 30 мкм (мінімум 20% кремнієвої смоли)
- Фарби, що розбавляються водою: 30 мкм
- Інші термореактивні фарби: 50 мкм
- Двокомпонентні фарби: 50 мкм
- Електрофоретичне покриття: 25 мкм
Інші системи покриття можуть вимагати різної товщини покриття, але наносити їх можна лише за погодженням з Виконавчим комітетом.
Методи та вимоги Qualicoat-Test
Результати необхідно оцінити, як показано на чотирьох типових прикладах (мінімальна товщина покриття для покриттів 60 мкм):
Приклад 1:
Виміряні значення в мкм: 82, 68, 75, 93, 86 середні: 81
Рейтинг: Цей зразок цілком задовільний.
Приклад 2:
Виміряні значення в мкм: 75, 68, 63, 66, 56 середні: 66
Оцінка: цей зразок хороший, оскільки середня товщина покриття становить понад 60 мкм і тому, що жодне виміряне значення не менше 48 мкм (80% від 60 мкм).
Приклад 3:
Виміряні значення в мкм: 57, 60, 59, 62, 53 середні: 58
Оцінка: ця вибірка є незадовільною та входить до заголовка «відхилені зразки» у таблиці 5.1.4.
Приклад 4:
Виміряні значення в мкм: 85, 67, 71, 64, 44 середні: 66
оцінка:
Цей зразок є незадовільним, хоча середня товщина покриття становить понад 60 мкм. Перевірку слід вважати невдалою, оскільки вимірюване значення 44 мкм нижче межі допуску 80% (48 мкм).
4. Адгезія
EN ISO 2409
Клейка стрічка повинна відповідати стандарту. Відстань між надрізами має становити 1 мм для товщини покриття до 60 мкм, 2 мм для товщини від 60 мкм до 120 мкм і 3 мм для більш товстого покриття.
ВИМОГИ: Результат повинен бути 0.
5. Відступ
EN ISO 2815
ВИМОГИ:
Мінімум 80 із зазначеною необхідною товщиною покриття.
6. Купінговий тест
Усі порошкові системи, крім порошків класів 2 і 3: EN ISO 2
Порошки 2 і 3 класу:
EN ISO 1520 з подальшим випробуванням на адгезію стрічкою, як зазначено нижче:
Після механічної деформації наклейте клейку стрічку (див. розділ 2.4) до покритої сторони контрольної панелі. Накрийте ділянку, щільно притиснувши до покриття, щоб усунути порожнечі або повітряні кишені. Через 1 хвилину різко відірвіть стрічку під прямим кутом до площини панелі.
ВИМОГИ:
- – Мінімум 5 мм для порошкові покриття (1, 2 і 3 класи)
- – Мінімум 5 мм для рідких покриттів, за винятком – двокомпонентні фарби та лаки: мінімум 3 мм – фарби та лаки, що розбавляються водою: мінімум 3 мм
- – Мінімум 5 мм для електрофоретичних покриттів
Щоб бути орієнтовним, випробування необхідно проводити на покритті товщиною, що наближається до мінімально необхідної.
При огляді неозброєним оком покриття не повинно мати жодних ознак розтріскування або відшарування, за винятком порошків 2 і 3 класів.
Порошки 2 і 3 класу:
При огляді неозброєним оком покриття не повинно мати жодних ознак відшарування після випробування на адгезію натягуванням стрічки.
Методи та вимоги Qualicoat-Test
Коментарі закриті