A por felhordásának módjai – ELEKTROMOS SZÓRÁS
Írta: doPowder | 29. január 2022-én
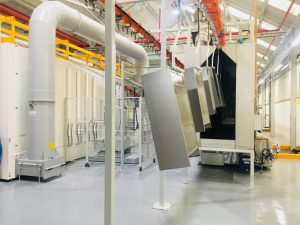
Az elektrosztatikus permetezés a legszélesebb körben alkalmazott felhordási módszer por bevonat anyagokat. Növekedése lenyűgöző ütemben növekszik. A 60-as évek közepén kifejlesztett eljárás a leghatékonyabb módja a bevonatok és felületkezelések rövid időn belüli felhordásának. Azonban a porbevonat elfogadása a génbenral kezdetben nagyon lassú volt az Egyesült Államokban. Európában az elektrosztatikus porpermetezési koncepciót könnyebben elfogadták, és a technológia sokkal gyorsabban fejlődött ott, mint a világ más részein. Azonban számos előrelépés történt mind a por anyagok, mind a gyártók rendelkezésére álló felhordó berendezések terén. Ezek a fejlesztések génralAz elektrosztatikus porszórt bevonattal kapcsolatos problémák, valamint a rendszerelemek funkcionális működésének javítása. Ennek eredményeként manapság az elektrosztatikus porszórt bevonatrendszerek széles választéka áll rendelkezésre.
A porbevonat anyagok elektrosztatikus porszóró eljárással történő felhordásához öt alapvető berendezés szükséges:
- Por adagoló egység;
- Elektrosztatikus porszóró pisztoly vagy ezzel egyenértékű elosztó berendezés;
- Elektrosztatikus feszültségforrás;
- Porvisszanyerő egység;
- Spray fülke
Vannak más eszközök is, amelyek javítják ezen alapvető alkatrészek működését. Az elektrosztatikus porszóró rendszer működése során a port az adagolóegységből egy porbevezető tömlőn keresztül a szórópisztoly(ok)ba szippantják, vagy szivattyúzzák. A szórópisztolyok szórt felhő formájában irányítják a port a rész felé. A hajtóerőt egyrészt a levegő biztosítja, amely a port szállítja az adagolóegységből a szórópisztolyba, másrészt a pisztolynál lévő por elektrosztatikus töltése. Az elektrosztatikus feszültséget a szórópisztolyra egy olyan forrás szolgáltatja, amely nagyfeszültségű, alacsony áramerősségű elektromos energiát továbbít a szórópisztolyhoz csatlakoztatott elektródákhoz. Ahogy a szétszórt, elektrosztatikusan feltöltött porfelhő közeledik a földelt részhez, elektromos vonzási mező jön létre, amely a porszemcséket az alkatrészhez vonzza és porréteget hoz létre. Az alkatrészhez nem tapadt túlpermet vagy port össze kell gyűjteni újrafelhasználás vagy ártalmatlanítás céljából. A kollektor egységben a port elválasztják a szállító légáramtól. Az összegyűjtött port ezután automatikusan vagy manuálisan újrahasznosítják az adagolóegységbe, hogy újrapermetezzenek. A levegő egy szűrőközeg-eszközön keresztül a tiszta levegő kamrába kerül, majd egy végső vagy abszolút szűrőn keresztül tiszta levegőként visszakerül a növényi környezetbe. A bevont alkatrészt ezután kihordják az alkalmazási területről, és hőhatásnak teszik ki, ami a poranyag kifolyását és megkeményedését eredményezi.
Gazdasági előny
Az elektrosztatikus porpermettel a porfelszórás akár 99%-a visszanyerhető és újra felhordható. A porral tapasztalható anyagveszteség minimális a folyékony bevonórendszerekhez képest.
Ezenkívül a legtöbb esetben a púder egyrétegű fedést biztosít, anélkül, hogy a kész alkatrészen lefutna és megereszkedne. Alkalmazása a primer A befejező bevonat előtt nincs szükség bevonatba, ami csökkenti a többrétegű folyékony rendszerek idő- és munkaigényét.
A szárítópor alacsonyabb üzemanyagköltsége gyakran a kisebb sütők használatából, a rövidebb sütési időkből és bizonyos esetekben az alacsonyabb sütőhőmérsékletből adódik. Nincs szükség a sminklevegő melegítésére vagy temperálására, mivel a levegő tiszta levegőként kerül vissza a növényi környezetbe.
A porral egyéb költségmegtakarítások is elérhetők, beleértve az alacsonyabb tisztítási költségeket is. Porral történő bevonáskor nincs szükség az oldószerek keverésére, visszanyerésére és ártalmatlanítására. Általában nem használnak oldószert vagy vegyszert sem a porfelhordó berendezés, sem a szórófülkék tisztításához. Mivel a levegő és a porszívók génralA porral, munkaerővel és tisztítószerekkel végzett tisztításhoz csak annyi kell, hogy csökkenjen, és megszűnjön a veszélyes festékiszap elhelyezése.
A folyékony bevonatok nagy százaléka olykor mérgező és gyúlékony oldószert tartalmaz, amelyek elvesznek az alkalmazási folyamat során. A szállítmány tárolása és az oldószerek kezelési költségei általában nagyon drágák. A porral gyakorlatilag megszűnnek a szennyezéscsökkentő berendezéssel, a lehűtési idővel és az oldószeres hulladékok ártalmatlanításával kapcsolatos költségek.
Az oldószerek használatának megszüntetése csökkentheti a tűzbiztosítási követelményeket, valamint a tűzbiztosítási védelem fenntartásáért fizetett díjakat is. Végül a fólia négyzetméterenkénti milliméterenkénti költsége a legtöbb esetben megegyezik a folyékony bevonat költségeivel, vagy alacsonyabb annál.
Könnyű alkalmazás
Az egyenletes felületi jellemzők és a porszórt alkalmazásoknál megvalósított elektrosztatikus „körvonal” segít csökkenteni a magasan képzett kezelők iránti igényt. Ezen túlmenően, porral történő bevonáskor nem kell fenntartani a viszkozitási egyensúlyt. A poranyagok „permetezésre készen” érkeznek a gyártótól. Por esetén nincs szükség lehűlési időre. A bevont rész közvetlenül a permetező területről a kemencébe szállítható kikeményedés céljából. Csökkenthető a selejtezési arány, csakúgy, mint az elutasított alkatrészek újrafeldolgozásának költségei. A futást és a megereszkedést általában kiküszöböljük a porfestési eljárással.
A nem megfelelő vagy nem megfelelő bevonat lefújható az alkatrészről (hőkezelés előtt), és újra bevonható. Ez kiküszöbölheti a lehúzással, újrakezeléssel, újbóli bevonattal és az elutasított alkatrészek újrafelhasználásával járó munkaerőt és költségeket. A felhasználók azt tapasztalták, hogy a porszórt bevonatolási folyamat könnyen automatizálható. Használhat automatikus pisztolymozgatókat, kontúrmechanizmusokat, robotokat és álló szórópisztoly-pozícionálást. Porszórt bevonattal a teljes gyártási idő gyakran csökkenthető vagy a gyártási mennyiség növelhető. A folyékony bevonatolási folyamat során szükséges különféle lépések kiiktatása hatékonyabb befejező vonalat eredményezhet.