કોટિંગ બનાવવાની પ્રક્રિયા
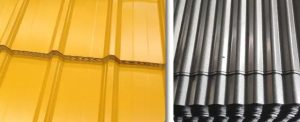
કોટિંગ-રચના પ્રક્રિયાને ત્રણ તબક્કામાં લેવલિંગ કરતી કોટિંગ ફિલ્મ બનાવવા માટે મેલ્ટ કોલેસેન્સમાં વિભાજિત કરી શકાય છે.
આપેલ તાપમાને, નિયંત્રણ પીગળેલા સંકલન દર સૌથી મહત્વપૂર્ણ પરિબળ એ રેઝિનનું ગલનબિંદુ, પાવડર કણોની પીગળેલી સ્થિતિની સ્નિગ્ધતા અને પાવડર કણોનું કદ છે. શક્ય તેટલી વહેલી તકે પીગળેલા શ્રેષ્ઠ સંકલન માટે, લેવલિંગ તબક્કાના પ્રવાહની અસરોને પૂર્ણ કરવા માટે લાંબો સમય મળે તે માટે. ક્યોરિંગ એજન્ટનો ઉપયોગ જરૂરી સમયના પ્રવાહ અને સ્તરીકરણ માટે ઉપલબ્ધ ટૂંકો, અને આમ તે અત્યંત સક્રિય પાવડરમાંથી બનેલી કોટિંગ ફિલ્મ ઘણીવાર નારંગીની છાલ રજૂ કરે છે.
કોટિંગના પ્રવાહ અને સ્તરીકરણને અસર કરતા મુખ્ય પરિબળો એ રેઝિનની પીગળેલી સ્નિગ્ધતા, સિસ્ટમની સપાટીનું તણાવ અને ફિલ્મની જાડાઈ છે. બદલામાં, મેલ્ટ સ્નિગ્ધતા, ખાસ કરીને ક્યોરિંગ તાપમાન, ક્યોરિંગ રેટ અને હીટિંગ રેટ પર આધાર રાખે છે.
ઉપરોક્ત વિવિધ પરિબળો, કણોના કદના વિતરણ અને ફિલ્મની જાડાઈ સાથે, સામાન્ય રીતે પેઇન્ટેડ વસ્તુઓ અને પાવડર બાંધકામની સ્થિતિ નક્કી કરવા માટે જરૂરી ફિલ્મ ગુણધર્મો દ્વારા નક્કી કરવામાં આવે છે. પાવડર ની પરત સિસ્ટમના સરફેસ ટેન્શનમાંથી પાવરનો પ્રવાહ અને સ્તરીકરણ, આ ફ્રન્ટનો પણ ઉલ્લેખ કરવામાં આવ્યો છે. તેનાથી વિપરીત, કોટિંગ ફિલ્મમાં પરમાણુઓ વચ્ચેના આકર્ષણ પર લાગુ બળ સાથે, પરિણામ, જેમ કે મેલ્ટ સ્નિગ્ધતા વધારે છે, પ્રવાહ અને સ્તરીકરણ સામે પ્રતિકાર વધારે છે. આમ, સપાટીનું તાણ અને ગુરુત્વાકર્ષણ વચ્ચેના તફાવતનું પરમાણુ કદ કોટિંગ ફિલ્મના સ્તરીકરણની હદ નક્કી કરે છે.
સારી ફ્લોબિલિટી સાથે કોટિંગ માટે, તે સ્પષ્ટ છે કે સિસ્ટમની સપાટીનું તણાવ શક્ય તેટલું ઊંચું હોવું જોઈએ, અને મેલ્ટ સ્નિગ્ધતા શક્ય તેટલી ઓછી હોવી જોઈએ. આ સિસ્ટમની સપાટીના તણાવમાં ઉમેરણો ઉમેરીને પ્રાપ્ત કરી શકાય છે અને નીચા પરમાણુ વજનના રેઝિનનો નીચા ગલનબિંદુનો ઉપયોગ કરીને સુધારી શકાય છે.
કોટિંગ-રચના પ્રક્રિયા
ઉત્કૃષ્ટ પ્રવાહના ગુણો ધરાવતી ઉપરોક્ત પરિસ્થિતિઓ અનુસાર કોટિંગ તૈયાર કરી શકાય છે, પરંતુ તેની ઉચ્ચ સપાટીના તાણને કારણે સંકોચન થાય છે, નીચા પીગળવાના કારણે સ્નિગ્ધતા ઝૂલશે, અને ખૂણાઓ નબળી કોટબિલિટી પેદા કરશે. વ્યવહારુ કાર્યમાં, સિસ્ટમની સપાટીની તાણ અને ઓગળવાની સ્નિગ્ધતા ચોક્કસ શ્રેણીમાં નિયંત્રિત થાય છે, તેથી યોગ્ય કોટિંગ સપાટીનો દેખાવ મેળવી શકાય છે.
કોટિંગ ફિલ્મના પ્રવાહની સપાટીના તણાવ અને ઓગળેલા સ્નિગ્ધતાની અસર આકૃતિ 2 માં બતાવવામાં આવી છે. આકૃતિમાં જોઈ શકાય છે તેમ, ખૂબ ઓછી અથવા ખૂબ ઊંચી પીગળેલી સ્નિગ્ધતાનું સપાટી તણાવ કોટિંગના પ્રવાહને અટકાવશે, પરિણામે એક કોટિંગ ફિલ્મ નબળી પ્રવાહક્ષમતા, અને સપાટી તણાવ ખૂબ વધારે છે ફિલ્મ રચના પ્રક્રિયા ક્રેટર્સ દેખાશે. મેલ્ટ સ્નિગ્ધતાની ભૌતિક સંગ્રહ સ્થિરતા ખૂબ ઓછી છે તે પાવડરને બગડે છે ખૂણાના બાંધકામની નબળી કોટેબિલિટી, અને રવેશમાં બાંધકામ ઝૂલશે.
સારાંશમાં, તે સ્પષ્ટ છે કે, પ્રાપ્ત પાવડર કોટિંગ ફિલ્મની સપાટીની અંતિમ સ્થિતિ, ખામીઓ અને ખામીઓ (જેમ કે નારંગીની છાલ, નબળી પ્રવાહક્ષમતા, ક્રેટર, પિનહોલ્સ, વગેરે) એકબીજા સાથે ગાઢ રીતે સંકળાયેલા છે, અને ડિપોઝિશન પ્રક્રિયામાં પણ સામેલ છે. rheological બળ નિયંત્રણ તબક્કામાં ફેરફાર. પાવડર કણોના કદનું વિતરણ પણ કોટિંગ ફિલ્મની સપાટીના દેખાવને અસર કરે છે. કણો જેટલા નાના હોય છે, તેની થર્મલ ક્ષમતાને કારણે મોટા કણો ઓછા હોય છે, તેથી તેનો ગલન સમય મોટા કણો કરતા ઓછો હોય છે, કોલેસેન્ટ પણ ઝડપથી થાય છે, અને કોટિંગ ફિલ્મની સપાટીનો દેખાવ વધુ સારો બને છે. નાના કણોની લંબાઈ કરતાં મોટા પાઉડર કણોના ગલનનો સમય, તેના પર બનેલી કોટિંગ ફિલ્મ નારંગીની છાલની અસર પેદા કરી શકે છે. ઇલેક્ટ્રોસ્ટેટિક પાવડર બાંધકામ પદ્ધતિઓ (કોરોના ડિસ્ચાર્જ અથવા ઘર્ષણ સ્રાવ), પણ નારંગીની છાલમાં પરિબળની રચના તરફ દોરી જાય છે.
પ્રવાહ અને સ્તરીકરણને પ્રોત્સાહન આપવા માટે નારંગીની છાલની અસરને કેવી રીતે ઘટાડવી અથવા ટાળવી તે નારંગીની છાલને ઘટાડી અથવા ટાળી શકે છે. સિસ્ટમ ઓછી મેલ્ટ સ્નિગ્ધતાનો ઉપયોગ કરે છે, સ્તરીકરણ વિસ્તૃત સમય અને ક્યોરિંગ પ્રક્રિયામાં ઉચ્ચ સપાટીના તણાવથી પ્રવાહ અને સ્તરીકરણ સુધારી શકાય છે. સપાટીના તાણના ઢાળને નિયંત્રિત કરવા માટેના મહત્વના પરિમાણો નારંગીની છાલ ઘટાડવામાં આવે છે, જ્યારે કોટિંગ ફિલ્મની સપાટીના સપાટીના તાણને નિયંત્રિત કરવાનું પણ એકસરખું હોય છે, જેથી સપાટીનો સૌથી નાનો વિસ્તાર મેળવવામાં આવે.
નારંગીની છાલ, ક્રેટર્સ, પિનહોલ્સ જેવી સપાટીની ખામીઓને દૂર કરવા માટે, કોટિંગના દેખાવને સુધારવા માટે, ફ્લો-પ્રમોટીંગ એજન્ટ અથવા લેવલિંગ એજન્ટનો ઉપયોગ ઘણીવાર વાસ્તવિક કાર્યમાં થાય છે. પ્રવાહને પ્રોત્સાહન આપતા એજન્ટનું સારું પ્રદર્શન મેલ્ટ સ્નિગ્ધતાને ઘટાડી શકે છે, આમ મેલ્ટ મિશ્રણ અને રંગદ્રવ્ય વિખેરવામાં ફાળો આપે છે, સબસ્ટ્રેટની ભીનાશતા, પ્રવાહ અને કોટિંગનું સ્તરીકરણ, સપાટીની ખામીઓને દૂર કરવામાં પણ મદદ કરે છે. હવાના પ્રકાશનને સરળ બનાવવા માટે.
ફ્લો મોડિફાયર ડોઝ અને અસર સંબંધની તપાસ થવી જોઈએ. અપૂરતી માત્રા સંકોચન અને નારંગીની છાલનું કારણ બનશે, વધુ પડતા વપરાશથી ચળકાટ, ધુમ્મસની ખોટ થશે અને ઉપરના ભાગમાં રિકોટ સંલગ્નતાની સમસ્યા ઊભી થશે. સામાન્ય રીતે, પ્રિમિક્સમાં ફ્લો મોડિફાયર ઉમેરવામાં આવે છે. અથવા રેઝિન માસ્ટર બેચ (રેઝિન અને 9/1 થી 8/2 નો એડિટિવ રેશિયો) થી બનેલો છે અથવા પાવડર સ્વરૂપમાં અકાર્બનિક વાહક પર શોષાય છે. પાવડર પેઇન્ટમાં ઉમેરણોની માત્રા 0.5 થી 1.5% છે (બાઈન્ડરમાં અસરકારક પોલિમરની ગણતરી કરવામાં આવે છે), પરંતુ ઓછી સાંદ્રતામાં પણ સારી હોઈ શકે છે.
પોલિએક્રીલેટ ફ્લો મોડિફાયર રેઝિનનો સૌથી વધુ ઉપયોગ થાય છે, જેમ કે પોલિએક્રીલિક એસિડ બ્યુટાઇલ એસ્ટર (“એક્રોનલ 4F”), એક્રેલિક એસિડ ઇથિલ – ઇથિલ હેક્સિલ એક્રેલેટ કોપોલિમર અને બ્યુટાઇલ એક્રેલેટ – એક્રેલિક એસિડ-હેક્સિલ એક્રેલેટ કોપોલિમર, વગેરે. તેઓ ખૂબ જ ઉપયોગમાં લઈ શકાય છે. વિશાળ સાંદ્રતા શ્રેણી. સામાન્ય રીતે પોલિએક્રીલેટ સપાટીના તણાવ પર થોડી અસર કરે છે, તેઓ પ્રમાણમાં સતત સમાન સપાટીની રચનામાં કોટિંગમાં ફાળો આપી શકે છે. સરફેસ ટેન્શન રિડ્યુસિંગ એડિટિવ્સ (જેમ કે સિલિકોન અથવા તેના જેવા) ની તુલનામાં, તેઓ સપાટીના તણાવને ઘટાડતા નથી, અને તેથી તેનો ઉપયોગ સ્તરીકરણને વેગ આપવા માટે થઈ શકે છે. સરફેસ એક્ટિવ એજન્ટ્સ, ફ્લોરિનેટેડ એલ્કાઈલ એસ્ટર્સ અને સિલિકોનનો સમાવેશ થાય છે. તેઓ જોડાયા રકમ ખૂબ જ સંવેદનશીલ છે. બેન્ઝોઇન એ ડિગાસિંગ એજન્ટ છે, તેની સપાટીના તણાવને ઘટાડવાની અસર પણ છે, પાવડર કોટિંગની કોટિંગ ફિલ્મની સપાટીના દેખાવને સુધારવા માટે વ્યાપકપણે ઉપયોગમાં લેવાય છે.
કોટિંગ બનાવવાની પ્રક્રિયા
ટિપ્પણીઓ બંધ છે