Investigación sobre a resistencia á corrosión do revestimento de Galvalume por inmersión en quente
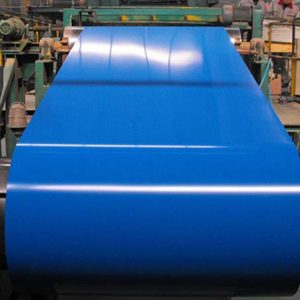
Os revestimentos de galvalume Zn55Al1.6Si por inmersión en quente utilizáronse amplamente en moitos campos como a industria do automóbil, a construción naval, a industria de maquinaria, etc., debido non só ao seu mellor rendemento anticorrosivo que o do revestimento de zinc, senón tamén ao seu baixo custo (o prezo do Al é máis baixo que o do Zn na actualidade). As terras raras como La poden dificultar o crecemento das escamas e aumentar a adhesión das escamas, polo que foron empregadas para protexer aceiros e outros. metálico aliaxes contra a oxidación e a corrosión. Non obstante, só hai poucas literaturas publicadas sobre a aplicación de La no revestimento de galvalume por inmersión en quente, e neste traballo investigáronse os efectos da adición de La sobre a resistencia á corrosión do revestimento de galvalume por inmersión en quente.
Experimental
[1] Inmersión en quenteOs revestimentos de aliaxe Zn-Al-Si-La por inmersión en quente que conteñen 0,0.02% en peso, 0.05% en peso, 0.1% en peso e 0.2% en peso La aplicáronse sobre fío de aceiro suave de 1 mm de diámetro. O proceso foi o seguinte: limpeza para eliminar a ferruxe e engraxamento por onda supersónica (55 °C) → limpeza con auga → fundente (85 °C) → secado (100~200 °C) mergullo en quente (640~670 °C, 3~5 s).
[2]Proba de perda de pesoA proba de perda de peso mediuse mediante probas de pulverización salina de ácido acético acelerado con cobre (CASS) e probas de corrosión por inmersión realizadas nunha cámara de pulverización salina e solución de NaCl ao 3.5%. Despois das probas, os produtos corrosivos foron eliminados por medios mecánicos, enxágües con auga corrente, despois secándose con aire frío e medindo a perda de peso mediante báscula electrónica. En ambos os casos, tres paralfixéronse mostras lel para obter resultados máis precisos. O tempo de proba foi de 120 h para a proba CASS e de 840 h para a proba de inmersión.
[3]Proba electroquímicaA proba electroquímica levouse a cabo pola estación de traballo electroquímica IM6e subministrada por Alemaña, tomando como contraelectrodo unha placa de platino, un electrodo de calomel saturado como electrodo de referencia e un fío de aceiro suave con revestimento de Zn-Al-Si-La en quente como electrodo de traballo. O medio de corrosión foi unha solución de NaCl ao 3.5%. A superficie exposta á solución de proba foi de 1 cm2. As medicións de espectroscopia de impedancia electroquímica (EIS) realizáronse cun intervalo de frecuencias de 10 kHz a 10 mHz, o ancho do sinal de tensión sinusoidal foi de 10 mV (rms). Rexistráronse curvas de polarización débiles no intervalo de tensión de -70 mV. a 70 mV, a taxa de exploración foi de 1 mV/s. En ambos os casos, o experimento non comezou ata que o potencial de corrosión permaneceu estable (unha variación de menos de 5 mV en 5 min).
As morfoloxías superficiais das mostras foron examinadas mediante un microscopio electrónico de varrido (SEM) SSX-550 despois das probas de corrosión na cámara de pulverización salina e na solución de NaCl ao 3.5%. Probáronse os produtos de corrosión que se forman na superficie das mostras no spray salino e na solución de NaCl ao 3.5% mediante a difracción de raios X (XRD) PW-3040160.
Resultados e discusión
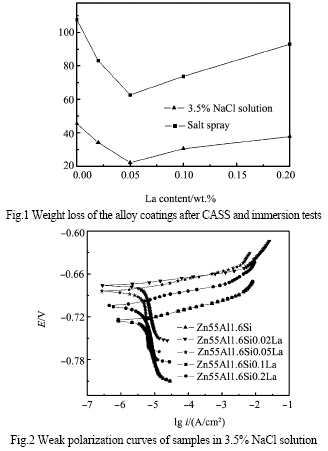
[1.1] Perda de peso
A Fig.1 ilustra os resultados das probas de perda de peso no armario de pulverización salina e na solución de NaCl ao 3.5%. A taxa de corrosión das mostras en ambos os casos diminuíu en primeiro lugar co aumento do contido de La ata o 0.05% en peso e despois aumentou ao aumentar aínda máis o contido de La. Polo tanto, a mellor resistencia á corrosión experimentouse nos revestimentos que conteñen 0.05% en peso de La. Descubriuse que durante a proba de inmersión, o óxido vermello atopouse máis cedo na superficie de revestimento de 0% en peso de La en solución de NaCl ao 3.5%, sen embargo, ata que rematou a proba de inmersión, non houbo ferruxe vermello na superficie de revestimento de 0.05% en peso de La. .
2.1.2 Ensaio electroquímico
A figura 2 mostra curvas de polarización débil para revestimentos de aliaxe Zn-Al-Si-La en solución de NaCl ao 3.5%. Pódese ver que a forma das curvas de polarización débiles mostrou poucas diferenzas e o proceso de corrosión de todo tipo de revestimentos de aliaxe controlouse por reacción catódica. Os resultados do axuste de Tafel baseados nas curvas de polarización débiles da Fig.2 preséntanse na Táboa 1. Do mesmo xeito que na proba de perda de peso, tamén se comprobou que a resistencia á corrosión do revestimento de galvalume podería mellorarse mediante unha pequena adición de La e o mínimo. a taxa de corrosión obtívose cun 0.05% La.
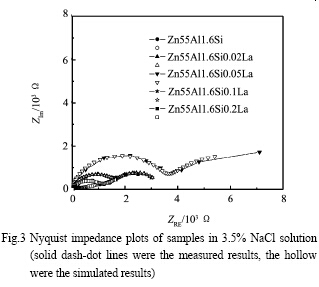
A Fig.3 representa os diagramas de Nyquist rexistrados para revestimentos con diferentes cantidades de adición de La expostos a solución de NaCl ao 3.5% durante 0.5 h. En todos os casos, había dous arcos que significaban dúas constantes de tempo. A que aparece a alta frecuencia representaba a característica dieléctrica do revestimento da aliaxe, mentres que a de baixa frecuencia correspondía á do substrato de aceiro suave nos poros (é dicir, defectos de revestimento). A medida que aumentaba a adición de La, aumentaba o diámetro do arco de alta frecuencia, este efecto era máis pronunciado no caso do revestimento de aliaxe Zn55Al1.6Si0.05La. No entanto, ao aumentar aínda máis o contido de La, o diámetro do arco de alta frecuencia diminuíu inversamente. Mentres tanto, o centro de todos os arcos inclinouse cara ao cuarto cuadrante, o que indica que o efecto de dispersión ocorreu na superficie do electrodo. Baixo esta condición, pódense obter mellores resultados usando CPE (elemento de fase constante) en lugar da capacitancia pura que se demostrou mediante outros grupos de investigación.
Os comentarios están pechados