Processus de formation de revêtement
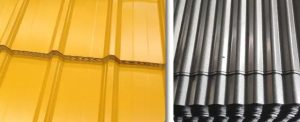
Le processus de formation de revêtement peut être divisé en coalescence à l'état fondu pour former un film de revêtement nivelant trois étapes.
A une température donnée, le contrôle du taux de coalescence fondue le facteur le plus important est le point de fusion de la résine, la viscosité à l'état fondu des particules de poudre et la taille des particules de poudre. Afin de mieux coalescence de fondu doit dès que possible, afin d'avoir un temps plus long pour terminer les effets de flux de phase de nivellement. L'utilisation d'un agent de durcissement raccourcit la disponibilité de l'écoulement et du nivellement du temps nécessaire, et donc le film de revêtement formé de ces poudres extrêmement actives présente souvent une peau d'orange.
Les facteurs clés qui affectent l'écoulement et le nivellement du revêtement sont la viscosité à l'état fondu de la résine, la tension superficielle du système et l'épaisseur du film. A son tour, la viscosité à l'état fondu dépend en particulier de la température de durcissement, de la vitesse de durcissement et de la vitesse de chauffage.
Les différents facteurs mentionnés ci-dessus, ainsi que la distribution granulométrique et l'épaisseur du film, sont généralement déterminés par les propriétés du film requises pour peindre les objets et les conditions de construction de la poudre décidées. Revêtement en poudre flux et nivellement de la puissance à partir de la tension superficielle du système, ce front a également été évoqué. La force appliquée à l'attraction entre les molécules dans le film de revêtement au contraire, le résultat, tel que la viscosité à l'état fondu est plus élevé, plus la résistance à l'écoulement et au nivellement est grande. Ainsi, la tension superficielle et la taille moléculaire de la différence entre la gravité déterminent l'étendue du nivellement du film de revêtement.
Pour un revêtement avec une bonne fluidité, il est clair que la tension superficielle du système doit être la plus élevée possible et la viscosité à l'état fondu la plus faible possible. Ceux-ci peuvent être obtenus en ajoutant des additifs à la tension superficielle du système qui peut être améliorée et l'utilisation d'un point de fusion bas de la résine de faible poids moléculaire.
Processus de formation de revêtement
Les revêtements peuvent être préparés selon les conditions ci-dessus ayant d'excellentes propriétés d'écoulement, mais en raison de sa tension superficielle élevée provoque le retrait, en raison de la viscosité à l'état fondu inférieure générera un affaissement et les coins Mauvaise aptitude au revêtement. Dans les travaux pratiques, la tension superficielle et la viscosité à l'état fondu du système sont contrôlées dans une plage spécifique, de sorte qu'un aspect de surface de revêtement qualifié peut être obtenu.
L'impact de la tension superficielle et de la viscosité à l'état fondu de l'écoulement du film de revêtement est illustré à la figure 2. Comme on peut le voir sur la figure, la tension superficielle d'une viscosité à l'état fondu trop faible ou trop élevée empêchera l'écoulement du revêtement, ce qui entraînera une fluidité médiocre du film de revêtement, et la tension superficielle est trop élevée, le processus de formation de film apparaîtra des cratères. La stabilité physique au stockage de la viscosité à l'état fondu est trop faible entraînera la détérioration de la poudre. Mauvaise aptitude au revêtement d'une construction d'angle et affaissement de la construction dans la façade.
En résumé, il est clair que l'état de surface final du film de revêtement en poudre obtenu, les défauts et les défauts (tels que la peau d'orange, la mauvaise coulabilité, les cratères, les trous d'épingle, etc.) sont étroitement liés, ainsi que dans le processus de dépôt impliqué dans le changement de phase dans le contrôle de la force rhéologique. La distribution granulométrique de la poudre affecte également l'aspect de surface du film de revêtement. Plus les particules sont petites, plus les particules sont grosses en raison de sa capacité thermique, donc son temps de fusion est plus court que celui des grosses particules, coalescent également plus rapidement, et un meilleur aspect de surface du film de revêtement se forme. Temps de fusion des grosses particules de poudre supérieur à la longueur des petites particules, le film de revêtement formé peut générer l'effet peau d'orange. Méthodes de construction de poudre électrostatique (décharge couronne ou décharge par frottement), mais conduit également à la formation d'un facteur dans la peau d'orange.
Comment réduire ou éviter l'effet peau d'orange pour favoriser l'écoulement et le nivellement peut réduire ou éviter la peau d'orange. Le système utilise une faible viscosité à l'état fondu, un temps de nivellement prolongé et une tension superficielle plus élevée dans le processus de durcissement peut améliorer le débit et le nivellement. Les paramètres importants pour contrôler le gradient de tension superficielle sont la peau d'orange réduite, tout en contrôlant également la tension superficielle de la surface du film de revêtement est uniforme, afin d'obtenir la plus petite surface.
Un agent favorisant l'écoulement ou un agent de nivellement est souvent utilisé dans le travail proprement dit pour améliorer l'aspect du revêtement, afin d'éliminer les défauts de surface tels que la peau d'orange, les cratères, les trous d'épingle. La bonne performance d'un agent favorisant l'écoulement peut réduire la viscosité à l'état fondu, contribuant ainsi au mélange à l'état fondu et à la dispersion des pigments, pour améliorer la mouillabilité du substrat, l'écoulement et le nivellement du revêtement, contribue également à éliminer les défauts de surface pour faciliter l'évacuation de l'air.
Le dosage du modificateur de débit et la relation entre les effets doivent être étudiés. Une quantité insuffisante entraînera un rétrécissement et une peau d'orange, une consommation excessive entraînera une perte de brillance, un voile et des problèmes d'adhérence du revêtement sur la tige. Typiquement, le modificateur d'écoulement dans le prémélange est ajouté. Soit constitué d'un mélange maître de résine (résine et rapport d'additif de 9/1 à 8/2), soit adsorbé sur le support inorganique sous forme de poudre. La quantité d'additifs dans la peinture en poudre est de 0.5 à 1.5% (dans les liants calculé polymère efficace), mais à de faibles concentrations peut également être bonne.
Les résines polyacrylates modificateurs de fluidité les plus utilisées, telles que l'ester butylique d'acide polyacrylique ("Acronal 4F"), le copolymère d'acide acrylique éthyle - acrylate d'éthyle hexyle et le copolymère d'acrylate de butyle - acide acrylique - acrylate d'hexyle, etc. large gamme de concentrations. Généralement les polyacrylates ont peu d'effet sur la tension superficielle, ils peuvent contribuer à ce que le revêtement forme une surface uniforme relativement constante. Par rapport à ceux des additifs réduisant la tension superficielle (tels que le silicone ou similaire), ils ne réduisent pas la tension superficielle et peuvent donc être utilisés pour accélérer le nivellement. Réduire la tension superficielle des additifs comprennent des agents tensioactifs, des esters d'alkyle fluorés et du silicone. Ils rejoignent le montant est très sensible. Le benjoin est un agent de dégazage, a également pour effet de réduire la tension superficielle, est largement utilisé pour améliorer l'aspect de surface du film de revêtement du revêtement en poudre.
Processus de formation de revêtement
Les commentaires sont fermés