Préparation de Carboxylterminé pour le revêtement en poudre époxyde lié par fusion
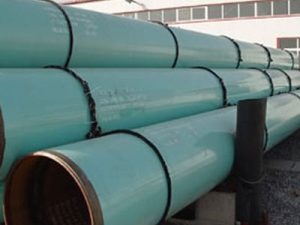
Préparation et caractérisation des prépolymères de résine époxy poly (butadiène-co-acrylonitrile) à terminaison carboxyle pour l'époxy liée par fusion Revêtement poudre
1 Présentation
Époxy lié par fusion (FBE) revêtements en poudre qui ont d'abord été développés par 3M Co., sont largement utilisés lorsque la protection contre la corrosion à long terme est essentielle, comme dans les industries des pipelines de pétrole, de métal, de gaz et d'eau. Cependant, les exigences de performance pour les revêtements en poudre FBE sont difficiles en raison de leur haute densité de réticulation. La fragilité inhérente des revêtements durcis est l'un des principaux obstacles empêchant une application plus large des époxydes dans les industries. Par conséquent, il peut être possible d'améliorer les performances des revêtements FBE en augmentant la ténacité du revêtement. De nombreuses méthodes de durcissement ont été utilisées pour durcir les systèmes époxy, souvent dans des applications composites, notamment le caoutchouc, l'élastomère, thermoplastique, un copolymère, des époxy modifiés par des nanoparticules et des combinaisons des éléments ci-dessus.
Bien qu'il y ait eu de nombreuses recherches sur les modifications de durcissement des systèmes époxy, la majorité des
les études impliquaient la modification chimique de la résine époxy avec du caoutchouc liquide réactif, en particulier du butadiène-co-acrylonitrile à terminaison carboxyle (CTBN). McGarry et al ont utilisé du CTBN de poids moléculaire 3000 et divers époxydes DGEBA durcis avec de la pipéridine. Kinloch et al ont révélé une dépendance dynamique dans le système DGEBA/CTBN/pipéridine en calculant la ténacité à la rupture par impact à différentes vitesses de frappe et en obtenant une augmentation de la ténacité presque doublée. Le CTBN pourrait être introduit dans les systèmes époxy tels que les résines époxy diglycidyl éther de bisphénol-A (DGEBA). Lorsque de telles résines époxy sont durcies avec le caoutchouc liquide, la ténacité des domaines peut être améliorée en absorbant l'énergie d'impact. Il est bien connu que les résines durcies comprennent des systèmes à deux phases [26] dans lesquels le caoutchouc liquide est dispersé dans une matrice d'époxyde avec une structure de domaine sphérique ou une structure continue.
Jusqu'à présent, le durcissement des résines époxy s'est principalement concentré sur les résines époxy liquides, et peu de recherches se sont concentrées sur le durcissement des résines époxy solides. Dans cet article, nous avons préparé des prépolymères CTBN-EP sans utiliser de solvants organiques. Ensuite, des composites de revêtements en poudre FBE remplis de prépolymères CTBN-EP ont été produits. Sur la base des propriétés mécaniques et de l'analyse morphologique, des tentatives ont été faites pour analyser les mécanismes de durcissement prévalant dans la matrice à phases séparées. L'analyse de la relation structure-propriété du système CTBN-EP est une nouvelle entreprise au meilleur de nos connaissances. Ainsi, cette nouvelle technologie de trempe peut élargir les domaines d'application des revêtements en poudre FBE dans l'industrie.
2 Expérimental
2.1 Matériaux
La résine époxy utilisée était de l'éther diglycidylique solide de bisphénol A (DGEBA) (DOW, DER663) avec un poids équivalent d'époxyde de 750-900. Poly(butadiène-co-acrylonitrile) liquide à terminaison carboxyle (CTBN) (Emerald, Hypro 1 300 x 1323) avec une teneur en acrylonitrile de 26 % a été utilisé. La triphénylphosphine a été utilisée comme catalyseur dans ce système. L'agent de durcissement (HTP-305) était un phénolique. La résine époxy phénolique (GT7255) a été achetée chez HUNTSMAN Co., Pigment (L6900), qui a été fourni par BASF Co., l'agent de dégazage et l'agent de nivellement ont été achetés chez Aisitelun.
2.2 Synthèse et caractérisation des prépolymères CTBNEP
Des quantités stoechiométriques de résines époxy, de CTBN et de catalyseur ont été placées dans un ballon qui a été chauffé et agité mécaniquement sous agitation à 150 ℃ pendant 3.0 h. La réaction a été arrêtée lorsque l'indice d'acide est tombé à 0. Les prépolymères ont été marqués comme C0, C5, C10, C15 et C20 (les indices sont le contenu du CTBN). La réaction possible est illustrée à la Fig.1.
La spectroscopie FTIR a été utilisée pour caractériser les structures. Les spectres FTIR ont été enregistrés par un spectrophotomètre FTLA2000-104 dans la gamme de longueurs d'onde de 4 500 à 500 cm-1 (ABB Bomem du Canada). Les poids moléculaires et la distribution des poids moléculaires des prépolymères CTBN-EP ont été déterminés par GPC. Le tétrahydrofurane (THF) a été utilisé comme éluant à un débit de 1.0 mL/min. Le système de colonne a été calibré en utilisant des polystyrènes standard monodispersés.
2.3 Préparation et caractérisation des films de durcissement
Cinq fi lms de durcissement contenant 0 % en poids à 20 % en poids de CTBN ont été préparés. Les quantités calculées de DGEBA (selon la formulation donnée dans le tableau 1) et de HTP-305 ont été agitées à 120 ℃ pendant 10 min pour obtenir un mélange homogène. Le mélange a été versé dans un moule en fer préchauffé durci dans un four à air chaud à 180 ℃ pendant 10 min puis post-durci pendant 30 min à 200 ℃.
Les essais de traction ont été réalisés sur une machine KD111-5 (KaiQiang Co., Ltd., Chine) à une vitesse de traverse de 1 mm/min. Les valeurs ont été prises à partir d'une moyenne de trois échantillons selon GB/2568-81. L'allongement à la rupture de l'éprouvette a été évalué. La résistance aux chocs de l'éprouvette a été déterminée sur une machine MZ-2056 en utilisant des éprouvettes rectangulaires de 40 mm × 10 mm × 2 mm. Les tests ont été effectués à température ambiante et les valeurs ont été prises à partir d'une moyenne de trois échantillons selon GB/T2571-1995.
Les températures de transition vitreuse des films de durcissement ont été déterminées à l'aide d'un analyseur mécanique dynamique (DMA). Les mesures ont été effectuées à une vitesse de chauffage de 2 ℃/min de -90 ℃ à 180 ℃ à un niveau de fréquence fixe de 1 Hz. Le module de stockage, le module de perte et le facteur de perte ont été obtenus en mode double porte-à-faux avec un échantillon de taille 30 mm × 10 mm × 2 mm.
Une microscopie électronique à balayage (SEM) a été réalisée (modèle Quanta-2000 SEM, FEI of Dutch) avec une tension électronique de 10 kV. Les échantillons ont été fracturés sous azote liquide et d'abord traités avec du toluène pour extraire la phase caoutchouc avant d'être séchés sous vide. La taille et la distribution des particules dispersées ont été déterminées au moyen de la prise d'une image semi-automatique.
Le pourcentage de perte de poids et les caractéristiques de dégradation thermique des échantillons préparés ont été évalués par un analyseur thermogravimétrique (TGA) enregistré sur Instrument (METTER Toledo of Switzerland). La quantité d'échantillon prélevé était d'environ 5 à 10 mg dans un porte-échantillon en platine. La vitesse de chauffage dans chaque cycle a été maintenue à 10 ℃/min et la plage de température était ambiante à 800 ℃.
Les commentaires sont fermés