Karboksyylipäätetyn pinnoitteen valmistus fuusiosidos-epoksijauhemaalausta varten
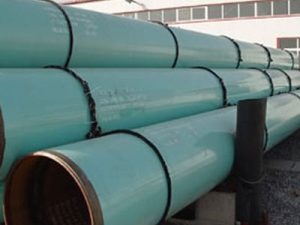
Karboksyylipäätettyjen poly(butadieeni-koakryylinitriili)-epoksihartsiesipolymeerien valmistus ja karakterisointi fuusiosidottua epoksia varten Tomukuorrute
1 Johdanto
Fuusiosidottu epoksi (FBE) jauhemaalit 3M Co.:n ensimmäisenä kehittämiä käytetään laajalti, kun pitkäaikainen korroosiosuojaus on kriittistä, kuten öljy-, metalli-, kaasu- ja vesiputkiteollisuudessa. FBE-jauhemaalien suorituskykyvaatimukset ovat kuitenkin haastavia niiden suuren silloitustiheyden vuoksi. Kovetettujen pinnoitteiden luontainen hauraus on yksi suurimmista esteistä, jotka estävät epoksien laajemman käytön teollisuudessa. Siksi FBE-pinnoitteiden suorituskykyä voi olla mahdollista parantaa lisäämällä pinnoitteen sitkeyttä. Epoksijärjestelmien karkaisuun on käytetty monia karkaisumenetelmiä, usein komposiittisovelluksissa, mukaan lukien kumi, elastomeeri, kestomuovi, kopolymeeri, nanohiukkasilla modifioidut epoksit ja edellä mainittujen yhdistelmät.
Vaikka epoksijärjestelmien karkaisuja on tutkittu paljon, suurin osa epoksijärjestelmistä
tutkimukset koskivat epoksihartsin kemiallista modifiointia reaktiivisella nestemäisellä kumilla, erityisesti karboksyylipäätteisellä butadieeni-koakryylinitriilillä (CTBN). McGarry ym. käyttivät CTBN:ää, jonka molekyylipaino oli 3000, ja erilaisia piperidiinillä kovetettuja DGEBA-epokseja. Kinloch ym. paljastivat dynaamisen riippuvuuden DGEBA/CTBN/piperidiinijärjestelmässä laskemalla iskumurtolujuuden eri iskunopeuksilla ja saamalla lähes kaksinkertaisen sitkeyden. CTBN voitaisiin lisätä epoksijärjestelmiin, kuten bisfenoli-A (DGEBA) -epoksihartsien diglysidyylieetteriin. Kun tällaiset epoksihartsit kovetetaan yhdessä nestemäisen kumin kanssa, domeenien sitkeyttä voidaan parantaa absorboimalla iskuenergiaa. On hyvin tunnettua, että kovetetut hartsit sisältävät kaksifaasijärjestelmän[26], joissa nestemäinen kumi on dispergoitu epoksimatriisiin, jossa on pallomainen domeenirakenne tai jatkuva rakenne.
Toistaiseksi epoksihartsien karkaisu on keskittynyt pääasiassa nestemäisiin epoksihartseihin, ja vähän tutkimusta on keskittynyt kiinteiden epoksihartsien karkaisuun. Tässä artikkelissa valmistimme CTBN-EP-esipolymeerejä käyttämättä orgaanisia liuottimia. Sitten valmistettiin CTBN-EP-esipolymeereillä täytetyt FBE-jauhemaalikomposiitit. Mekaanisten ominaisuuksien ja morfologisen analyysin perusteella yritettiin analysoida faasierotetussa matriisissa vallitsevia sitkeytysmekanismeja. CTBN-EP-järjestelmän rakenteen ominaisuussuhteen analyysi on parhaan tietämyksemme mukaan uusi yritys. Siten tämä uusi karkaisutekniikka voi laajentaa FBE-jauhemaalien käyttöalueita teollisuudessa.
2. Kokeellinen
2.1 Materiaalit
Käytetty epoksihartsi oli kiinteää bisfenoli A:n diglysidyylieetteriä (DGEBA) (DOW, DER663), jonka epoksidiekvivalenttipaino oli 750-900. Nestemäinen, karboksyylipäätteinen poly(butadieeni-koakryylinitriili) (CTBN) (Emerald, Hypro 1 300 × 1323), jonka akryylinitriilipitoisuus oli 26 %. Trifenyylifosfiinia käytettiin katalyyttinä tässä järjestelmässä. Kovete (HTP-305) oli fenoli. Fenoliepoksihartsi (GT7255) ostettiin yhtiöltä HUNTSMAN Co., Pigment (L6900), jonka toimitti BASF Co., kaasunpoistoaine ja tasoitusaine ostettiin Aisitelunilta.
2.2 CTBNEP-esipolymeerien synteesi ja karakterisointi
Stökiömetriset määrät epoksihartseja, CTBN:ää ja katalyyttiä laitettiin pulloon, jota kuumennettiin ja sekoitettiin mekaanisesti sekoittaen 150 °C:ssa 3.0 tuntia. Reaktio pysäytettiin, kun happoarvo laski nollaan. Esipolymeerit merkittiin C0, C0, C5, C10 ja C15 (alaindeksit ovat CTBN:n sisältöä). Mahdollinen reaktio on esitetty kuvassa 20.
Rakenteiden karakterisointiin käytettiin FTIR-spektroskopiaa. FTIR-spektrit tallennettiin FTLA2000-104-spektrofotometrillä aallonpituusalueella 4 500-500 cm−1 (ABB Bomem, Kanada). CTBN-EP-esipolymeerien molekyylipainot ja molekyylipainojakauma määritettiin GPC:llä. Tetrahydrofuraania (THF) käytettiin eluenttina virtausnopeudella 1.0 ml/min. Pylväsjärjestelmä kalibroitiin käyttämällä monodispersiota standardipolystyreeniä.
2.3 Kovetuskalvojen valmistus ja karakterisointi
Valmistettiin viisi kovetuskalvoa, jotka sisälsivät 0-20 paino-% CTBN:ää. DGEBA:n (taulukossa 1 annettujen formulaatioiden mukaisesti) ja HTP-305:n laskettuja määriä sekoitettiin 120 °C:ssa 10 minuuttia homogeenisen seoksen saamiseksi. Seos kaadettiin esilämmitettyyn rautamuottiin, joka kovetettiin kuumailmauunissa 180 ℃:ssa 10 min ja sitten jälkikovetettiin 30 min 200 ℃:ssa.
Vetokokeet suoritettiin KD111-5-koneella (KaiQiang Co., Ltd., Kiina) poikkipään nopeudella 1 mm/min. Arvot on otettu keskimäärin kolmesta näytteestä GB/2568-81:n mukaan. Näytteen murtokohdan venymä arvioitiin. Näytteen iskulujuus määritettiin MZ-2056-koneella käyttämällä suorakaiteen muotoisia näytteitä, joiden koko oli 40 mm × 10 mm × 2 mm. Testit suoritettiin huoneenlämmössä ja arvot otettiin keskimäärin kolmesta näytteestä GB/T2571-1995:n mukaisesti.
Kovetettujen kalvojen lasittumislämpötilat määritettiin dynaamisella mekaanisella analysaattorilla (DMA). Mittaukset suoritettiin kuumennusnopeudella 2 ℃/min -90 ℃ - 180 ℃ kiinteällä 1 Hz:n taajuustasolla. Varastointimoduuli, häviömoduuli ja häviökerroin saatiin käyttämällä kaksoisulokemoodia näytteen kokoisella 30 mm × 10 mm × 2 mm.
Pyyhkäisyelektronimikroskooppi (SEM) suoritettiin (Quanta-2000 malli SEM, FEI hollantilainen) elektronijännitteellä 10 kV. Näytteet murrettiin nestemäisessä typessä ja käsiteltiin ensin tolueenilla kumifaasin uuttamiseksi ennen kuin ne kuivattiin tyhjössä. Dispergoituneiden hiukkasten koko ja jakautuminen määritettiin ottamalla puoliautomaattinen kuva.
Valmistettujen näytteiden prosentuaalinen painohäviö ja lämpöhajoamisominaisuudet arvioitiin termogravimetrisella analysaattorilla (TGA), joka on tallennettu Instrumentille (METTER Toledo, Sveitsi). Otetun näytteen määrä oli noin 5-10 mg platinanäyteastiassa. Kuumennusnopeus kussakin ajossa pidettiin arvossa 10 ℃/min ja lämpötila-alue oli 800 ℃.
Kommenttien lisääminen on estetty