Kuumakastetun galvalume-pinnoitteen korroosionkestävyyden tutkimus
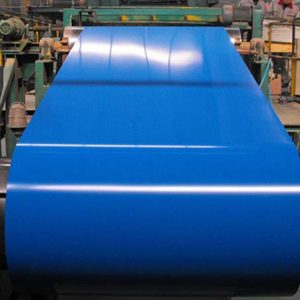
Kuumasutettuja Zn55Al1.6Si galvalumiinipinnoitteita on käytetty laajalti monilla aloilla, kuten autoteollisuudessa, laivanrakennuksessa, koneteollisuudessa jne., ei pelkästään sen paremman korroosionestokyvyn ansiosta kuin sinkkipinnoitteen, vaan myös sen alhaisten kustannusten vuoksi. Alin hinta on alhaisempi kuin Zn:n tällä hetkellä). Harvinaiset maametallit, kuten La, voivat estää kalkkikiven kasvua ja lisätä kalkkikiven tarttumista, joten niitä on käytetty suojaamaan teräksiä ja muita metallinen seokset hapettumista ja korroosiota vastaan. On kuitenkin vain vähän kirjallisuutta julkaistuja La:n käyttämisestä kuumakastettu galvalumiinipinnoitteessa, ja tässä artikkelissa on tutkittu La-lisäyksen vaikutuksia kuumaupogalvalumiinipinnoitteen korroosionkestävyyteen.
Kokeellinen
[1] Hot-dippingKuumasutetut Zn-Al-Si-La-seospinnoitteet, jotka sisälsivät 0,0.02 painoprosenttia, 0.05 painoprosenttia, 0.1 painoprosenttia ja 0.2 painoprosenttia La:ta, levitettiin Ф 1 mm:n pehmeälle teräslangalle. Prosessi oli seuraava: puhdistus ruosteen ja rasvan poistamiseksi yliääniaallon avulla (55 °C) → puhdistus vedellä → sulatus (85 °C) → kuivaus (100–200 °C) kuumakasto (640–670 °C, 3~5 s).
[2]PainonpudotustestiPainonpudotuskoe mitattiin kuparikiihdytetyllä etikkahapposuolasumutestauksella (CASS) ja upotuskorroosiokokeilla, jotka suoritettiin suolasumutuskammiossa ja 3.5 % NaCl-liuoksessa. Testien jälkeen syövyttävät tuotteet poistettiin mekaanisesti, huuhdeltiin juoksevalla vedellä, kuivattiin sitten kylmäpuhallusilmalla ja painon menetys mitattiin elektronisella vaa'alla. Molemmissa tapauksissa kolme paralOtettiin näytteitä tarkempien tulosten saamiseksi. Testausaika oli 120 tuntia CASS-testissä ja 840 tuntia upotuskokeessa.
[3]Sähkökemiallinen testiSähkökemiallinen testi suoritettiin Saksan toimittamalla IM6e-sähkökemiallisella työasemalla käyttämällä platinalevyä vastaelektrodina, kyllästettyä kalomelielektrodia vertailuelektrodina ja kuumakastettua Zn-Al-Si-La-pinnoitetta pehmeää teräslankaa työelektrodina. Syövyttävä väliaine oli 3.5 % NaCl-liuos. Testiliuokselle altistettu pinta-ala oli 1 cm2. Sähkökemiallisen impedanssispektroskopian (EIS) mittaukset suoritettiin taajuusalueella 10 kHz - 10 mHz, sinimuotoisen jännitesignaalin leveys oli 10 mV (rms). Heikkoja polarisaatiokäyriä tallennettiin jännitealueella -70 mV 70 mV:iin, pyyhkäisynopeus oli 1 mV/s. Molemmissa tapauksissa koe aloitettiin vasta, kun korroosiopotentiaali pysyi vakaana (vaihtelu alle 5 mV 5 minuutissa).
Näytteiden pintamorfologiat tutkittiin SSX-550-pyyhkäisyelektronimikroskoopilla (SEM) suolasumutuskammiossa ja 3.5 % NaCl-liuoksessa suoritetun korroosiokokeiden jälkeen. Suolasumussa ja 3.5 % NaCl-liuoksessa näytteiden pinnalle muodostuneet korroosiotuotteet testattiin käyttämällä PW-3040160 röntgendiffraktiota (XRD).
tulokset ja keskustelu
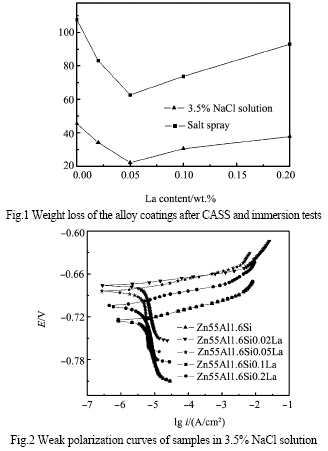
[1.1] Painonpudotus
Kuva 1 havainnollistaa suolasumutuskaapin ja 3.5 % NaCl-liuoksen painonpudotuskokeiden tuloksia. Näytteiden korroosionopeus molemmissa tapauksissa laski ensin La-pitoisuuden noustessa 0.05 painoprosenttiin ja sitten kasvoi La-pitoisuuden kasvaessa edelleen. Siksi paras korroosionkestävyys koettiin pinnoitteilla, jotka sisälsivät 0.05 paino-% La. Havaittiin, että upotuskokeessa punaruostetta havaittiin aikaisintaan 0 paino-% La-pinnoitepinnalla 3.5-prosenttisessa NaCl-liuoksessa, mutta upotuskokeen päättymiseen asti ei ollut punaista ruostetta 0.05-painoprosenttisella La-pinnoitepinnalla. .
2.1.2 Sähkökemiallinen testi
Kuvio 2 esittää heikot polarisaatiokäyrät Zn-Al-Si-La-lejeerinkipinnoitteille 3.5 % NaCl-liuoksessa. Voidaan nähdä, että heikkojen polarisaatiokäyrien muodossa oli vähän eroja, ja kaikenlaisten seospinnoitteiden korroosioprosessia ohjattiin katodisella reaktiolla. Kuvan 2 heikkoihin polarisaatiokäyriin perustuvat Tafel-sovitustulokset on esitetty taulukossa 1. Kuten painonpudotuskokeessa, havaittiin myös, että galvalumiinipinnoitteen korroosionkestävyyttä voitaisiin parantaa pienellä lisäyksellä La ja minimi korroosionopeus saatiin 0.05 paino-% La:lla.
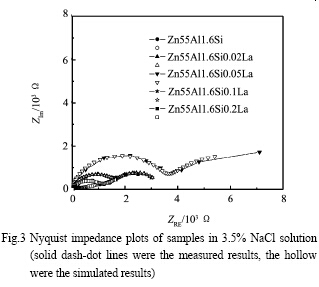
Kuvio 3 esittää Nyquist-diagrammeja, jotka on tallennettu pinnoitteille, joissa on eri määriä La-lisäystä altistettuna 3.5 % NaCl-liuokselle 0.5 tunnin ajan. Kaikissa tapauksissa oli kaksi kaarta, jotka tarkoittivat kaksiaikavakiota. Korkealla taajuudella esiintyvä edusti seospinnoitteen dielektristä ominaisuutta, kun taas matalataajuinen vastasi huokosissa olevan pehmeän terässubstraatin ominaisuutta (eli pinnoitevirheitä). La-lisäyksen kasvaessa suurtaajuuskaaren halkaisija kasvoi, tämä vaikutus oli selvempi Zn55Al1.6Si0.05La-seospinnoitteen tapauksessa. La-pitoisuuden kasvaessa edelleen korkeataajuisen kaaren halkaisija kuitenkin pieneni käänteisesti. Samaan aikaan kaikkien kaarien keskipiste kallistui neljänteen kvadranttiin, mikä osoittaa, että dispersiovaikutus tapahtui elektrodin pinnalla. Tässä tilanteessa parempia tuloksia voidaan saada käyttämällä CPE:tä (vakiofaasielementti) puhtaan kapasitanssin sijaan, mikä osoitti muut tutkimusryhmät.
Kommenttien lisääminen on estetty