Proceso de conformación de revestimentos
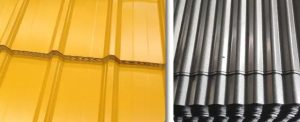
O proceso de formación de revestimento pódese dividir en coalescencia de fusión para formar unha película de revestimento que nivela tres etapas.
A unha determinada temperatura, a taxa de coalescencia fundida de control o factor máis importante é o punto de fusión da resina, a viscosidade do estado fundido das partículas de po e o tamaño das partículas de po. Co fin de mellor coalescencia de fundido debe o máis axiña posible, a fin de ter un tempo máis longo para completar os efectos de fluxo fase de nivelación. O uso dun axente de curado acurtado dispoñible para o fluxo e nivelación do tempo necesario, e, polo tanto, a película de revestimento formada por aqueles en po moi activos adoitan presentar casca de laranxa.
Os factores clave que afectan o fluxo e a nivelación do revestimento son a viscosidade da fusión da resina, a tensión superficial do sistema e o espesor da película. Pola súa banda, a viscosidade do fundido depende especialmente da temperatura de curado, da taxa de curado e da velocidade de quecemento.
Os diversos factores mencionados anteriormente, xunto coa distribución do tamaño das partículas e o grosor da película, adoitan estar determinados polas propiedades da película necesarias para pintar obxectos e decidir as condicións de construción do po. Recubrimento en po caudal e nivelación da potencia da tensión superficial do sistema, tamén se mencionou esta fronte. A forza aplicada á atracción entre as moléculas na película de revestimento pola contra, o resultado, como a viscosidade de fusión é maior, maior é a resistencia ao fluxo e nivelación. Así, a tensión superficial e o tamaño molecular da diferenza entre os gravitatorios determinan a extensión da nivelación da película de revestimento.
Para un revestimento con boa fluidez, está claro que a tensión superficial do sistema debe ser o máis alta posible e que a viscosidade do fundido é o máis baixa posible. Estes pódense conseguir engadindo aditivos á tensión superficial do sistema pódese mellorar e utilizar un punto de fusión baixo da resina de baixo peso molecular.
Proceso de formación de revestimento
Os revestimentos pódense preparar de acordo coas condicións anteriores, tendo excelentes propiedades de fluxo, pero debido á súa alta tensión superficial provoca o encollemento, debido á menor viscosidade de fusión, xerará flacidez e esquinas escasa capas. No traballo práctico, a tensión superficial e a viscosidade de fusión do sistema contrólanse dentro dun rango específico, polo que se pode obter un aspecto da superficie de revestimento cualificado.
O impacto da tensión superficial e da viscosidade de fusión do fluxo da película de revestimento móstrase na figura 2. Como se pode ver na figura, a tensión superficial dunha viscosidade de fusión demasiado baixa ou demasiado alta impedirá o fluxo de revestimento, o que provoca unha película de revestimento escasa fluidez, ea tensión superficial é demasiado alta, o proceso de formación de película aparecerá cráteres. A estabilidade física de almacenamento da viscosidade de fusión é demasiado baixa fará que o po se deteriore. Pobre capabilidade dunha construción de esquina, e a construción na fachada flacide.
En resumo, está claro que a condición final da superficie da película de recubrimento en po obtida, os defectos e as deficiencias (como a casca de laranxa, a escasa fluidez, os cráteres, os buratos, etc.) están estreitamente relacionados, e tamén no proceso de deposición implicado no proceso de deposición. cambio de fase no control da forza reolóxica. A distribución do tamaño das partículas do po tamén afecta o aspecto superficial da película de revestimento. Canto máis pequenas sexan as partículas, as partículas máis grandes de baixa debido á súa capacidade térmica, polo que o seu tempo de fusión é máis curto que o das partículas grandes, coalescentes tamén máis rápido, e fórmase mellor aspecto superficial da película de revestimento. Grandes partículas de po tempo de fusión que a lonxitude das partículas pequenas, a película de revestimento formada en pode ser xerada o efecto de casca de laranxa. Métodos de construción en po electrostático (descarga corona ou descarga por fricción), pero tamén leva á formación dun factor na casca de laranxa.
Como reducir ou evitar o efecto da casca de laranxa para promover o fluxo e a nivelación pode reducir ou evitar a casca de laranxa. O sistema utiliza unha baixa viscosidade de fusión, nivelación de tempo prolongado e unha maior tensión superficial no proceso de curado pode mellorar o fluxo e nivelación. Os parámetros importantes para controlar o gradiente de tensión superficial é a casca de laranxa reducida, mentres que tamén o control da tensión superficial da superficie da película de revestimento é uniforme, a fin de obter a menor área de superficie.
O axente promotor de fluxo ou un axente nivelador úsase a miúdo no traballo real para mellorar o aspecto do revestimento, a fin de eliminar defectos da superficie como casca de laranxa, cráteres, buratos. O bo rendemento dun axente promotor de fluxo pode reducir a viscosidade do fundido, contribuíndo así á mestura do fundido e á dispersión do pigmento, para mellorar a humectabilidade do substrato, o fluxo e a nivelación do revestimento, tamén axuda a eliminar os defectos da superficie. como para facilitar a liberación de aire.
Débese investigar a relación entre a dosificación e o efecto do modificador de fluxo. A cantidade insuficiente provocará encollemento e casca de laranxa, o consumo excesivo provocará unha perda de brillo, turbidez e producirá problemas de adhesión do revestimento na parte superior. Normalmente, engádese o modificador de fluxo na premestura. Ou feito dun lote mestre de resina (resina e proporción de aditivos de 9/1 a 8/2), ou adsorbido no soporte inorgánico en forma de po. A cantidade de aditivos na pintura en po é de 0.5 a 1.5% (en Aglutinantes calculado polímero efectivo), pero a baixas concentracións tamén pode ser bo.
As resinas modificadoras de fluxo de poliacrilato máis utilizadas, como o éster butílico de ácido poliacrílico (“Acronal 4F”), o copolímero de etil-etil-hexil acrilato de ácido acrílico e o copolímero de acrilato de butilo-ácido acrílico-acrilato de hexilo, etc. amplo rango de concentración. Normalmente poliacrilato pouco efecto sobre a tensión superficial, poden contribuír a que o revestimento forma unha superficie uniforme relativamente constante. En comparación cos aditivos redutores de tensión superficial (como silicona ou similares), non reducen a tensión superficial e, polo tanto, poden usarse para acelerar a nivelación. Reducir a tensión superficial dos aditivos inclúen axentes tensioactivos, ésteres de alquilo fluorados e silicona. Súmanse a cantidade é moi sensible. O benjuí é un axente desgasificador, tamén ten o efecto de reducir a tensión superficial, úsase amplamente para mellorar o aspecto superficial da película de revestimento do revestimento en po.
Proceso de conformación de revestimentos
Os comentarios están pechados