ಲೇಪನವನ್ನು ರೂಪಿಸುವ ಪ್ರಕ್ರಿಯೆ
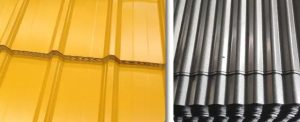
ಲೇಪನ-ರೂಪಿಸುವ ಪ್ರಕ್ರಿಯೆಯನ್ನು ಮೂರು ಹಂತಗಳಲ್ಲಿ ಲೆವೆಲಿಂಗ್ ಮಾಡುವ ಲೇಪನ ಫಿಲ್ಮ್ ಅನ್ನು ರೂಪಿಸಲು ಕರಗುವ ಕೋಲೆಸೆನ್ಸ್ ಆಗಿ ವಿಂಗಡಿಸಬಹುದು.
ನಿರ್ದಿಷ್ಟ ತಾಪಮಾನದಲ್ಲಿ, ನಿಯಂತ್ರಣ ಕರಗಿದ ಕೋಲೆಸೆನ್ಸ್ ದರವು ರಾಳದ ಕರಗುವ ಬಿಂದು, ಪುಡಿ ಕಣಗಳ ಕರಗಿದ ಸ್ಥಿತಿಯ ಸ್ನಿಗ್ಧತೆ ಮತ್ತು ಪುಡಿ ಕಣಗಳ ಗಾತ್ರವಾಗಿದೆ. ಲೆವೆಲಿಂಗ್ ಹಂತದ ಹರಿವಿನ ಪರಿಣಾಮಗಳನ್ನು ಪೂರ್ಣಗೊಳಿಸಲು ಹೆಚ್ಚಿನ ಸಮಯವನ್ನು ಹೊಂದಲು ಕರಗಿದ ಉತ್ತಮ ಸಂಯೋಜನೆಯನ್ನು ಸಾಧ್ಯವಾದಷ್ಟು ಬೇಗ ಮಾಡಬೇಕು. ಕ್ಯೂರಿಂಗ್ ಏಜೆಂಟ್ನ ಬಳಕೆಯು ಅಗತ್ಯವಿರುವ ಸಮಯದ ಹರಿವು ಮತ್ತು ಲೆವೆಲಿಂಗ್ಗೆ ಲಭ್ಯವಾಗುವಂತೆ ಸಂಕ್ಷಿಪ್ತಗೊಳಿಸಲಾಗಿದೆ ಮತ್ತು ಹೀಗಾಗಿ ಆ ಅತ್ಯಂತ ಸಕ್ರಿಯವಾದ ಪುಡಿಯಿಂದ ರೂಪುಗೊಂಡ ಲೇಪನ ಫಿಲ್ಮ್ ಸಾಮಾನ್ಯವಾಗಿ ಕಿತ್ತಳೆ ಸಿಪ್ಪೆಯನ್ನು ಪ್ರಸ್ತುತಪಡಿಸುತ್ತದೆ.
ಲೇಪನದ ಹರಿವು ಮತ್ತು ಲೆವೆಲಿಂಗ್ ಮೇಲೆ ಪರಿಣಾಮ ಬೀರುವ ಪ್ರಮುಖ ಅಂಶಗಳು ರಾಳದ ಕರಗುವ ಸ್ನಿಗ್ಧತೆ, ಸಿಸ್ಟಮ್ನ ಮೇಲ್ಮೈ ಒತ್ತಡ ಮತ್ತು ಫಿಲ್ಮ್ ದಪ್ಪವಾಗಿರುತ್ತದೆ. ಪ್ರತಿಯಾಗಿ, ಕರಗುವ ಸ್ನಿಗ್ಧತೆ, ನಿರ್ದಿಷ್ಟವಾಗಿ ಕ್ಯೂರಿಂಗ್ ತಾಪಮಾನ, ಕ್ಯೂರಿಂಗ್ ದರ ಮತ್ತು ತಾಪನ ದರವನ್ನು ಅವಲಂಬಿಸಿರುತ್ತದೆ.
ಮೇಲೆ ತಿಳಿಸಿದ ವಿವಿಧ ಅಂಶಗಳು, ಕಣದ ಗಾತ್ರದ ವಿತರಣೆ ಮತ್ತು ಫಿಲ್ಮ್ ದಪ್ಪದ ಜೊತೆಗೆ, ಸಾಮಾನ್ಯವಾಗಿ ಚಿತ್ರಿಸಲು ಅಗತ್ಯವಾದ ಫಿಲ್ಮ್ ಗುಣಲಕ್ಷಣಗಳಿಂದ ನಿರ್ಧರಿಸಲಾಗುತ್ತದೆ ಮತ್ತು ಪುಡಿ ನಿರ್ಮಾಣದ ಪರಿಸ್ಥಿತಿಗಳನ್ನು ಚಿತ್ರಿಸಲಾಗುತ್ತದೆ. ಪೌಡರ್ ಲೇಪನ ವ್ಯವಸ್ಥೆಯ ಮೇಲ್ಮೈ ಒತ್ತಡದಿಂದ ಶಕ್ತಿಯ ಹರಿವು ಮತ್ತು ಲೆವೆಲಿಂಗ್, ಈ ಮುಂಭಾಗವನ್ನು ಸಹ ಉಲ್ಲೇಖಿಸಲಾಗಿದೆ. ವ್ಯತಿರಿಕ್ತವಾಗಿ ಲೇಪನ ಚಿತ್ರದಲ್ಲಿನ ಅಣುಗಳ ನಡುವಿನ ಆಕರ್ಷಣೆಗೆ ಅನ್ವಯಿಸುವ ಬಲವು, ಕರಗುವ ಸ್ನಿಗ್ಧತೆಯಂತಹ ಫಲಿತಾಂಶವು ಹೆಚ್ಚಾಗಿರುತ್ತದೆ, ಹರಿವು ಮತ್ತು ಲೆವೆಲಿಂಗ್ ವಿರುದ್ಧ ಹೆಚ್ಚಿನ ಪ್ರತಿರೋಧ. ಹೀಗಾಗಿ, ಮೇಲ್ಮೈ ಒತ್ತಡ, ಮತ್ತು ಗುರುತ್ವಾಕರ್ಷಣೆಯ ನಡುವಿನ ವ್ಯತ್ಯಾಸದ ಆಣ್ವಿಕ ಗಾತ್ರವು ಲೇಪನದ ಫಿಲ್ಮ್ ಲೆವೆಲಿಂಗ್ನ ವ್ಯಾಪ್ತಿಯನ್ನು ನಿರ್ಧರಿಸುತ್ತದೆ.
ಉತ್ತಮ ಫ್ಲೋಬಿಲಿಟಿ ಹೊಂದಿರುವ ಲೇಪನಕ್ಕಾಗಿ, ಸಿಸ್ಟಮ್ನ ಮೇಲ್ಮೈ ಒತ್ತಡವು ಸಾಧ್ಯವಾದಷ್ಟು ಹೆಚ್ಚಿರಬೇಕು ಮತ್ತು ಕರಗುವ ಸ್ನಿಗ್ಧತೆಯು ಸಾಧ್ಯವಾದಷ್ಟು ಕಡಿಮೆಯಾಗಿದೆ ಎಂದು ಸ್ಪಷ್ಟವಾಗುತ್ತದೆ. ವ್ಯವಸ್ಥೆಯ ಮೇಲ್ಮೈ ಒತ್ತಡಕ್ಕೆ ಸೇರ್ಪಡೆಗಳನ್ನು ಸೇರಿಸುವ ಮೂಲಕ ಸುಧಾರಿಸಬಹುದು ಮತ್ತು ಕಡಿಮೆ ಆಣ್ವಿಕ ತೂಕದ ರಾಳದ ಕಡಿಮೆ ಕರಗುವ ಬಿಂದುವನ್ನು ಬಳಸುವುದರ ಮೂಲಕ ಇವುಗಳನ್ನು ಸಾಧಿಸಬಹುದು.
ಲೇಪನ-ರೂಪಿಸುವ ಪ್ರಕ್ರಿಯೆ
ಅತ್ಯುತ್ತಮ ಹರಿವಿನ ಗುಣಲಕ್ಷಣಗಳನ್ನು ಹೊಂದಿರುವ ಮೇಲಿನ ಪರಿಸ್ಥಿತಿಗಳಿಗೆ ಅನುಗುಣವಾಗಿ ಲೇಪನಗಳನ್ನು ತಯಾರಿಸಬಹುದು, ಆದರೆ ಅದರ ಹೆಚ್ಚಿನ ಮೇಲ್ಮೈ ಒತ್ತಡದ ಕಾರಣದಿಂದಾಗಿ ಕುಗ್ಗುವಿಕೆಗೆ ಕಾರಣವಾಗುತ್ತದೆ, ಕಡಿಮೆ ಕರಗುವ ಸ್ನಿಗ್ಧತೆಯು ಕುಗ್ಗುವಿಕೆಗೆ ಕಾರಣವಾಗುತ್ತದೆ ಮತ್ತು ಮೂಲೆಗಳು ಕಳಪೆ ಕೋಟಬಿಲಿಟಿಗೆ ಕಾರಣವಾಗುತ್ತದೆ. ಪ್ರಾಯೋಗಿಕ ಕೆಲಸದಲ್ಲಿ, ಸಿಸ್ಟಮ್ನ ಮೇಲ್ಮೈ ಒತ್ತಡ ಮತ್ತು ಕರಗುವ ಸ್ನಿಗ್ಧತೆಯನ್ನು ನಿರ್ದಿಷ್ಟ ವ್ಯಾಪ್ತಿಯಲ್ಲಿ ನಿಯಂತ್ರಿಸಲಾಗುತ್ತದೆ, ಆದ್ದರಿಂದ ಅರ್ಹವಾದ ಲೇಪನ ಮೇಲ್ಮೈ ನೋಟವನ್ನು ಪಡೆಯಬಹುದು.
ಲೇಪನ ಫಿಲ್ಮ್ನ ಹರಿವಿನ ಮೇಲ್ಮೈ ಒತ್ತಡ ಮತ್ತು ಕರಗುವ ಸ್ನಿಗ್ಧತೆಯ ಪ್ರಭಾವವನ್ನು ಚಿತ್ರ 2 ರಲ್ಲಿ ತೋರಿಸಲಾಗಿದೆ. ಚಿತ್ರದಲ್ಲಿ ನೋಡಬಹುದಾದಂತೆ, ತುಂಬಾ ಕಡಿಮೆ ಅಥವಾ ಹೆಚ್ಚು ಕರಗುವ ಸ್ನಿಗ್ಧತೆಯ ಮೇಲ್ಮೈ ಒತ್ತಡವು ಲೇಪನದ ಹರಿವನ್ನು ತಡೆಯುತ್ತದೆ, ಪರಿಣಾಮವಾಗಿ ಒಂದು ಲೇಪನ ಫಿಲ್ಮ್ ಕಳಪೆ ಹರಿವು, ಮತ್ತು ಮೇಲ್ಮೈ ಒತ್ತಡವು ತುಂಬಾ ಅಧಿಕವಾಗಿದ್ದು, ಫಿಲ್ಮ್ ರಚನೆಯ ಪ್ರಕ್ರಿಯೆಯು ಕುಳಿಗಳು ಕಾಣಿಸಿಕೊಳ್ಳುತ್ತವೆ. ಕರಗಿದ ಸ್ನಿಗ್ಧತೆಯ ಭೌತಿಕ ಶೇಖರಣಾ ಸ್ಥಿರತೆಯು ತುಂಬಾ ಕಡಿಮೆಯಾಗಿದೆ, ಪುಡಿ ಹದಗೆಡುತ್ತದೆ ಮೂಲೆಯ ನಿರ್ಮಾಣದ ಕಳಪೆ ಕೋಟಬಿಲಿಟಿ, ಮತ್ತು ಮುಂಭಾಗವು ಕುಗ್ಗುವಿಕೆಯಲ್ಲಿ ನಿರ್ಮಾಣವಾಗುತ್ತದೆ.
ಸಂಕ್ಷಿಪ್ತವಾಗಿ ಹೇಳುವುದಾದರೆ, ಪಡೆದ ಪುಡಿ ಲೇಪನದ ಫಿಲ್ಮ್ನ ಅಂತಿಮ ಮೇಲ್ಮೈ ಸ್ಥಿತಿ, ದೋಷಗಳು ಮತ್ತು ಕೊರತೆಗಳು (ಕಿತ್ತಳೆ ಸಿಪ್ಪೆ, ಕಳಪೆ ಹರಿವು, ಕುಳಿಗಳು, ಪಿನ್ಹೋಲ್ಗಳು, ಇತ್ಯಾದಿ) ನಿಕಟವಾಗಿ ಪರಸ್ಪರ ಸಂಬಂಧ ಹೊಂದಿವೆ ಮತ್ತು ಶೇಖರಣೆ ಪ್ರಕ್ರಿಯೆಯಲ್ಲಿ ತೊಡಗಿಕೊಂಡಿವೆ. ಭೂವೈಜ್ಞಾನಿಕ ಬಲ ನಿಯಂತ್ರಣದಲ್ಲಿ ಹಂತದ ಬದಲಾವಣೆ. ಪುಡಿ ಕಣದ ಗಾತ್ರದ ವಿತರಣೆಯು ಲೇಪನ ಚಿತ್ರದ ಮೇಲ್ಮೈ ನೋಟವನ್ನು ಸಹ ಪರಿಣಾಮ ಬೀರುತ್ತದೆ. ಸಣ್ಣ ಕಣಗಳು, ಅದರ ಉಷ್ಣ ಸಾಮರ್ಥ್ಯದ ಕಾರಣದಿಂದಾಗಿ ಕಡಿಮೆ ದೊಡ್ಡ ಕಣಗಳು, ಆದ್ದರಿಂದ ಅದರ ಕರಗುವ ಸಮಯವು ದೊಡ್ಡ ಕಣಗಳಿಗಿಂತ ಚಿಕ್ಕದಾಗಿದೆ, ಕೋಲೆಸೆಂಟ್ಗಳು ಸಹ ವೇಗವಾಗಿ, ಮತ್ತು ಲೇಪನ ಫಿಲ್ಮ್ನ ಉತ್ತಮ ಮೇಲ್ಮೈ ರೂಪವು ರೂಪುಗೊಳ್ಳುತ್ತದೆ. ಸಣ್ಣ ಕಣಗಳ ಉದ್ದಕ್ಕಿಂತ ದೊಡ್ಡ ಪುಡಿ ಕಣಗಳು ಕರಗುವ ಸಮಯ, ಅದರ ಮೇಲೆ ರೂಪುಗೊಂಡ ಲೇಪನ ಫಿಲ್ಮ್ ಕಿತ್ತಳೆ ಸಿಪ್ಪೆಯ ಪರಿಣಾಮವನ್ನು ಉಂಟುಮಾಡಬಹುದು. ಸ್ಥಾಯೀವಿದ್ಯುತ್ತಿನ ಪುಡಿ ನಿರ್ಮಾಣ ವಿಧಾನಗಳು (ಕರೋನಾ ಡಿಸ್ಚಾರ್ಜ್ ಅಥವಾ ಘರ್ಷಣೆ ಡಿಸ್ಚಾರ್ಜ್), ಆದರೆ ಕಿತ್ತಳೆ ಸಿಪ್ಪೆಯಲ್ಲಿ ಅಂಶದ ರಚನೆಗೆ ಕಾರಣವಾಗುತ್ತದೆ.
ಹರಿವನ್ನು ಉತ್ತೇಜಿಸಲು ಕಿತ್ತಳೆ ಸಿಪ್ಪೆಯ ಪರಿಣಾಮವನ್ನು ಕಡಿಮೆ ಮಾಡುವುದು ಅಥವಾ ತಪ್ಪಿಸುವುದು ಹೇಗೆ ಮತ್ತು ಲೆವೆಲಿಂಗ್ ಮಾಡುವುದರಿಂದ ಕಿತ್ತಳೆ ಸಿಪ್ಪೆಯನ್ನು ಕಡಿಮೆ ಮಾಡಬಹುದು ಅಥವಾ ತಪ್ಪಿಸಬಹುದು. ವ್ಯವಸ್ಥೆಯು ಕಡಿಮೆ ಕರಗುವ ಸ್ನಿಗ್ಧತೆಯನ್ನು ಬಳಸುತ್ತದೆ, ವಿಸ್ತೃತ ಸಮಯವನ್ನು ಲೆವೆಲಿಂಗ್ ಮಾಡುತ್ತದೆ ಮತ್ತು ಕ್ಯೂರಿಂಗ್ ಪ್ರಕ್ರಿಯೆಯಲ್ಲಿ ಹೆಚ್ಚಿನ ಮೇಲ್ಮೈ ಒತ್ತಡವು ಹರಿವು ಮತ್ತು ಲೆವೆಲಿಂಗ್ ಅನ್ನು ಸುಧಾರಿಸಬಹುದು. ಮೇಲ್ಮೈ ಒತ್ತಡದ ಗ್ರೇಡಿಯಂಟ್ ಅನ್ನು ನಿಯಂತ್ರಿಸುವ ಪ್ರಮುಖ ನಿಯತಾಂಕಗಳು ಕಿತ್ತಳೆ ಸಿಪ್ಪೆಯನ್ನು ಕಡಿಮೆಗೊಳಿಸುತ್ತವೆ, ಆದರೆ ಲೇಪನ ಫಿಲ್ಮ್ ಮೇಲ್ಮೈಯ ಮೇಲ್ಮೈ ಒತ್ತಡವನ್ನು ನಿಯಂತ್ರಿಸುವುದು ಚಿಕ್ಕದಾದ ಮೇಲ್ಮೈ ಪ್ರದೇಶವನ್ನು ಪಡೆಯಲು ಏಕರೂಪವಾಗಿರುತ್ತದೆ.
ಕಿತ್ತಳೆ ಸಿಪ್ಪೆ, ಕುಳಿಗಳು, ಪಿನ್ಹೋಲ್ಗಳಂತಹ ಮೇಲ್ಮೈ ದೋಷಗಳನ್ನು ತೊಡೆದುಹಾಕಲು, ಲೇಪನದ ನೋಟವನ್ನು ಸುಧಾರಿಸಲು ನಿಜವಾದ ಕೆಲಸದಲ್ಲಿ ಫ್ಲೋ-ಪ್ರೋಮೋಟಿಂಗ್ ಏಜೆಂಟ್ ಅಥವಾ ಲೆವೆಲಿಂಗ್ ಏಜೆಂಟ್ ಅನ್ನು ಹೆಚ್ಚಾಗಿ ಬಳಸಲಾಗುತ್ತದೆ. ಹರಿವು-ಉತ್ತೇಜಿಸುವ ಏಜೆಂಟ್ನ ಉತ್ತಮ ಕಾರ್ಯಕ್ಷಮತೆಯು ಕರಗುವ ಸ್ನಿಗ್ಧತೆಯನ್ನು ಕಡಿಮೆ ಮಾಡುತ್ತದೆ, ಹೀಗಾಗಿ ಕರಗುವ ಮಿಶ್ರಣ ಮತ್ತು ವರ್ಣದ್ರವ್ಯದ ಪ್ರಸರಣಕ್ಕೆ ಕೊಡುಗೆ ನೀಡುತ್ತದೆ, ತಲಾಧಾರದ ತೇವವನ್ನು ಸುಧಾರಿಸಲು, ಲೇಪನದ ಹರಿವು ಮತ್ತು ಲೆವೆಲಿಂಗ್, ಮೇಲ್ಮೈ ದೋಷಗಳನ್ನು ನಿವಾರಿಸಲು ಸಹಾಯ ಮಾಡುತ್ತದೆ. ಗಾಳಿಯ ಬಿಡುಗಡೆಗೆ ಅನುಕೂಲವಾಗುವಂತೆ.
ಹರಿವಿನ ಪರಿವರ್ತಕ ಡೋಸೇಜ್ ಮತ್ತು ಪರಿಣಾಮದ ಸಂಬಂಧವನ್ನು ತನಿಖೆ ಮಾಡಬೇಕು. ಸಾಕಷ್ಟು ಪ್ರಮಾಣವು ಕುಗ್ಗುವಿಕೆ ಮತ್ತು ಕಿತ್ತಳೆ ಸಿಪ್ಪೆಯನ್ನು ಉಂಟುಮಾಡುತ್ತದೆ, ಅತಿಯಾದ ಸೇವನೆಯು ಹೊಳಪು, ಮಬ್ಬು ನಷ್ಟಕ್ಕೆ ಕಾರಣವಾಗುತ್ತದೆ ಮತ್ತು ಮೇಲ್ಭಾಗದಲ್ಲಿ ರಿಕೋಟ್ ಅಂಟಿಕೊಳ್ಳುವಿಕೆಯ ಸಮಸ್ಯೆಗಳನ್ನು ಉಂಟುಮಾಡುತ್ತದೆ. ವಿಶಿಷ್ಟವಾಗಿ, ಪ್ರಿಮಿಕ್ಸ್ನಲ್ಲಿ ಫ್ಲೋ ಮಾರ್ಪಾಡು ಸೇರಿಸಲಾಗುತ್ತದೆ. ಅಥವಾ ರಾಳದ ಮಾಸ್ಟರ್ ಬ್ಯಾಚ್ನಿಂದ ಮಾಡಲ್ಪಟ್ಟಿದೆ (ರಾಳ ಮತ್ತು ಸಂಯೋಜಕ ಅನುಪಾತ 9/1 ರಿಂದ 8/2), ಅಥವಾ ಪುಡಿ ರೂಪದಲ್ಲಿ ಅಜೈವಿಕ ವಾಹಕದ ಮೇಲೆ ಹೀರಿಕೊಳ್ಳಲಾಗುತ್ತದೆ. ಪುಡಿ ಬಣ್ಣದಲ್ಲಿನ ಸೇರ್ಪಡೆಗಳ ಪ್ರಮಾಣವು 0.5 ರಿಂದ 1.5% (ಬೈಂಡರ್ಗಳಲ್ಲಿ ಪರಿಣಾಮಕಾರಿ ಪಾಲಿಮರ್ ಅನ್ನು ಲೆಕ್ಕಹಾಕಲಾಗುತ್ತದೆ), ಆದರೆ ಕಡಿಮೆ ಸಾಂದ್ರತೆಗಳಲ್ಲಿ ಸಹ ಉತ್ತಮವಾಗಿರುತ್ತದೆ.
ಪಾಲಿಯಾಕ್ರಿಲಿಕ್ ಆಸಿಡ್ ಬ್ಯುಟೈಲ್ ಎಸ್ಟರ್ ("ಅಕ್ರೋನಲ್ 4 ಎಫ್"), ಅಕ್ರಿಲಿಕ್ ಆಸಿಡ್ ಈಥೈಲ್ - ಈಥೈಲ್ ಹೆಕ್ಸಿಲ್ ಅಕ್ರಿಲೇಟ್ ಕೋಪಾಲಿಮರ್ ಮತ್ತು ಬ್ಯುಟೈಲ್ ಅಕ್ರಿಲೇಟ್ - ಅಕ್ರಿಲಿಕ್ ಆಸಿಡ್-ಹೆಕ್ಸಿಲ್ ಅಕ್ರಿಲೇಟ್ ಕೋಪಾಲಿಮರ್, ಇತ್ಯಾದಿಗಳಂತಹ ಪಾಲಿಯಾಕ್ರಿಲೇಟ್ ಫ್ಲೋ ಮಾರ್ಪಡಿಸುವ ರೆಸಿನ್ಗಳು ಹೆಚ್ಚು ವ್ಯಾಪಕವಾಗಿ ಬಳಸಲ್ಪಡುತ್ತವೆ. ವ್ಯಾಪಕ ಸಾಂದ್ರತೆಯ ಶ್ರೇಣಿ. ಸಾಮಾನ್ಯವಾಗಿ ಪಾಲಿಯಾಕ್ರಿಲೇಟ್ ಮೇಲ್ಮೈ ಒತ್ತಡದ ಮೇಲೆ ಕಡಿಮೆ ಪರಿಣಾಮ ಬೀರುತ್ತದೆ, ತುಲನಾತ್ಮಕವಾಗಿ ಸ್ಥಿರವಾದ ಏಕರೂಪದ ಮೇಲ್ಮೈಯನ್ನು ರೂಪಿಸುವ ಲೇಪನಕ್ಕೆ ಅವು ಕೊಡುಗೆ ನೀಡುತ್ತವೆ. ಮೇಲ್ಮೈ ಒತ್ತಡವನ್ನು ಕಡಿಮೆ ಮಾಡುವ ಸೇರ್ಪಡೆಗಳೊಂದಿಗೆ ಹೋಲಿಸಿದರೆ (ಉದಾಹರಣೆಗೆ ಸಿಲಿಕೋನ್ ಅಥವಾ ಹಾಗೆ), ಅವು ಮೇಲ್ಮೈ ಒತ್ತಡವನ್ನು ಕಡಿಮೆ ಮಾಡುವುದಿಲ್ಲ ಮತ್ತು ಆದ್ದರಿಂದ ಲೆವೆಲಿಂಗ್ ಅನ್ನು ವೇಗಗೊಳಿಸಲು ಬಳಸಬಹುದು. ಸೇರ್ಪಡೆಗಳ ಮೇಲ್ಮೈ ಒತ್ತಡವನ್ನು ಕಡಿಮೆ ಮಾಡುವುದು ಮೇಲ್ಮೈ ಸಕ್ರಿಯ ಏಜೆಂಟ್ಗಳು, ಫ್ಲೋರಿನೇಟೆಡ್ ಆಲ್ಕೈಲ್ ಎಸ್ಟರ್ಗಳು ಮತ್ತು ಸಿಲಿಕೋನ್ಗಳನ್ನು ಒಳಗೊಂಡಿರುತ್ತದೆ. ಅವರು ಸೇರುವ ಮೊತ್ತವು ತುಂಬಾ ಸೂಕ್ಷ್ಮವಾಗಿರುತ್ತದೆ. ಬೆಂಜೊಯಿನ್ ಒಂದು ಡಿಗ್ಯಾಸಿಂಗ್ ಏಜೆಂಟ್, ಇದು ಮೇಲ್ಮೈ ಒತ್ತಡವನ್ನು ಕಡಿಮೆ ಮಾಡುವ ಪರಿಣಾಮವನ್ನು ಹೊಂದಿದೆ, ಪುಡಿ ಲೇಪನದ ಲೇಪನದ ಮೇಲ್ಮೈ ನೋಟವನ್ನು ಸುಧಾರಿಸಲು ವ್ಯಾಪಕವಾಗಿ ಬಳಸಲಾಗುತ್ತದೆ.
ಲೇಪನವನ್ನು ರೂಪಿಸುವ ಪ್ರಕ್ರಿಯೆ
ಕಾಮೆಂಟ್ಗಳನ್ನು ಮುಚ್ಚಲಾಗಿದೆ